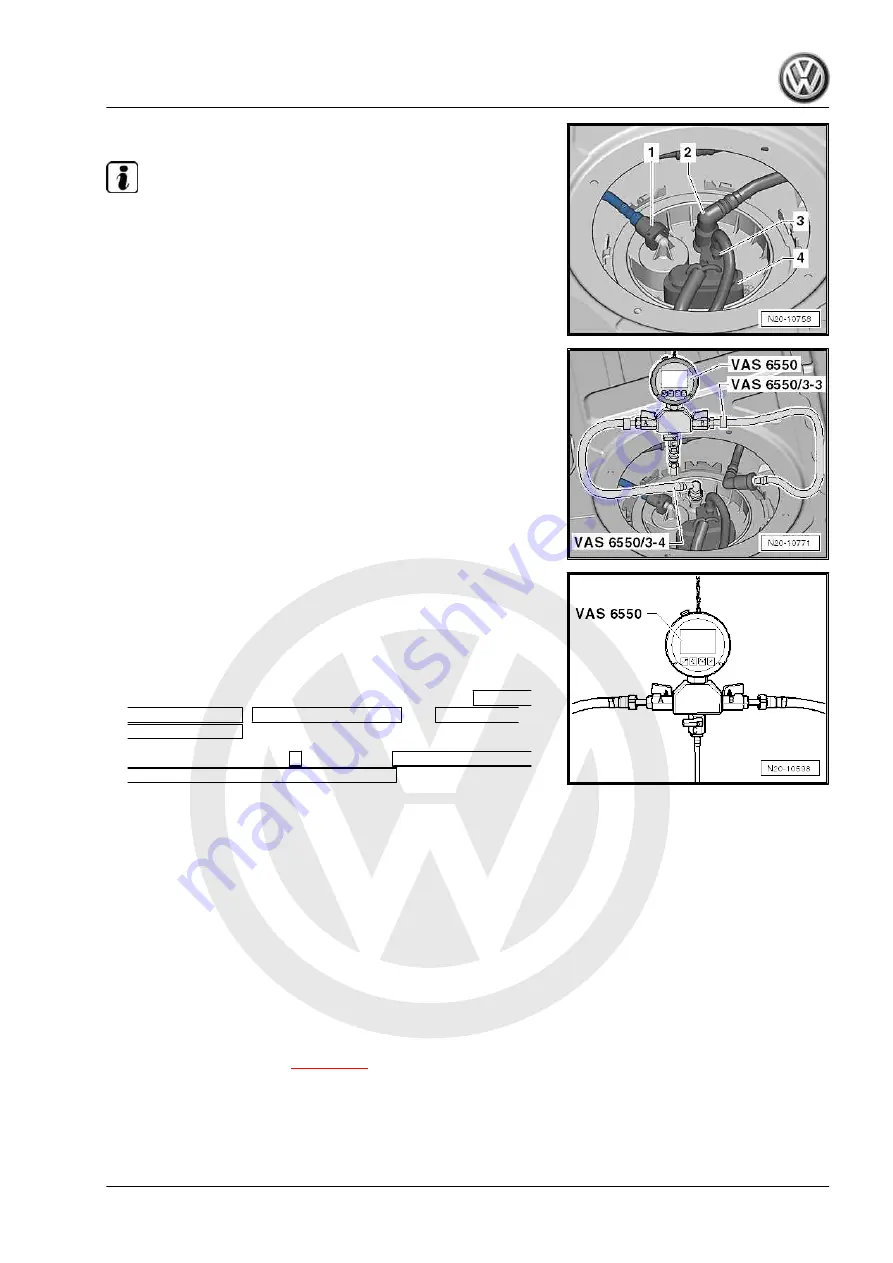
Pro
te
c
t
ed
b
y
co
p
y
rig
h
t.
C
o
p
y
in
g
fo
r
pr
iv
a
t
e
o
r
c
o
m
m
e
r
c
ia
l
p
u
rp
o
s
e
s
,
i
n
p
a
rt
o
r i
n
w
h
o
le
,
is
n
o
t
p
e
r
m
it
t
e
d
u
n
l
e
s
s
a
ut
ho
r
i
s
ed
b
y
V
olk
sw
a
ge
n AG
.
V
olk
s
w
a
g
en
AG do
es
n
ot g
uar
ante
e
or a
c
c
ep
t
a
ny
li
a
b
i
li
t
y
w
ith
r
e
s
p
e
c
t
t
o
th
e
c
o
rr
e
c
t
n
e
s
s
o
f
in
fo
r
m
a
tio
n
in
th
is
d
o
c
um
en
t.
C
o
py
rig
ht b
y
V
olk
sw
a
ge
n
A
G.
– Pull off fuel supply line -2-.
Note
Release connection by pressing button on hose coupling.
– Connect pressure tester - VAS 6550- to connecting line - VAS
6550/3-4- and connecting line - VAS 6550/3-3- as shown.
– Open shut-off taps “A” and “B” of pressure tester - VAS 6550-
and open in flow direction.
– Close shut-off tap “C”.
– Connect the vehicle diagnostic tester .
– Switch on ignition.
– Press one after the other in the display the buttons for
Vehicle
self-diagnosis
,
Engine electronics
and
Final con-
trol diagnosis
.
– Press right arrow button
►
on display to
Final control di-
agnosis for fuel pump electronics
.
The fuel pump must now run slowly up to maximum speed.
– Read pressure shown by pressure tester - VAS 6550- .
• Specification: 5.0 … 7.0 bar
– Switch off ignition.
If the specifications are now attained:
– Check fuel supply line from fuel tank to engine for possible
damage.
If the specifications are again not attained:
– Check all couplings and fuel lines in fuel tank and fuel delivery
unit to make sure they are firmly seated and are not leaking.
If no fault is found:
– Renew fuel delivery unit
⇒ page 188
.
Touareg 2010 ➤ , Touareg 2015 ➤
6-cylinder direct-injection engine (3.6 l engine, 4V) - Edition 12.2019
3. Checking fuel pump
199