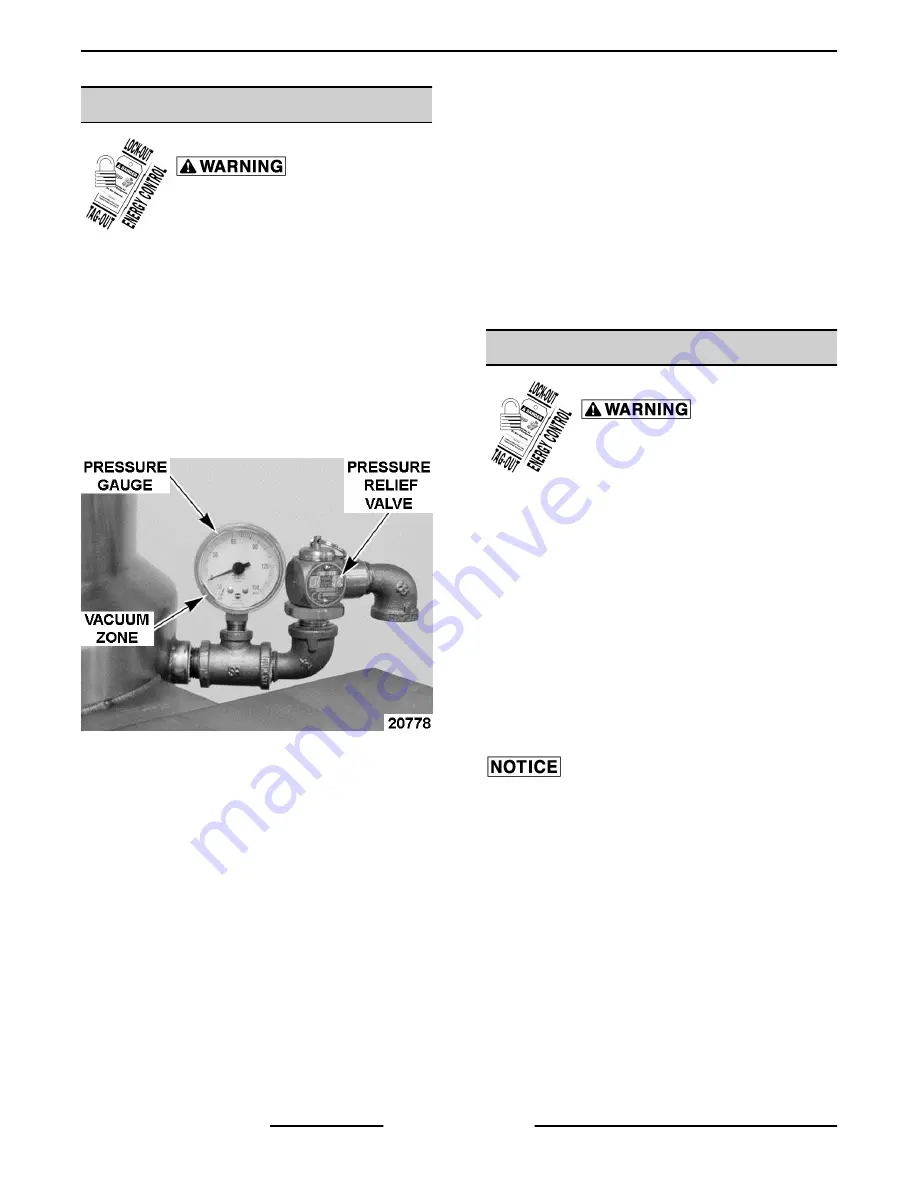
VENTING
Certain procedures in this section
require electrical test or
measurements while power is
applied to the machine. Exercise
extreme caution at all times and
follow Arc Flash procedures. If test
points are not easily accessible,
disconnect power and follow
Lockout/Tagout procedures, attach
test equipment and reapply power to
test.
NOTE:
This procedure outlines venting the reservoir
jacket to remove air for proper heat transfer to the
kettle contents.
Fig. 33
1.
With the kettle at room temperature, verify
pressure gauge is in the vacuum zone and
reading 25 to 30 in. Hg.
A.
If vacuum is below minimum listed, air must
be removed from reservoir jacket. Continue
with procedure to vent as necessary.
2.
Place kettle in full upright position.
3.
Turn power switch on.
4.
Set temperature dial to highest setting. Allow
kettle to heat until the heat indicator light turns off.
5.
Open pressure relief valve for approximately 10
seconds.
6.
Turn power switch off and allow kettle to cool
(room temperature).
7.
Verify pressure gauge reading is within the
correct vacuum range.
A.
If reading is below minimum listed or will not
maintain proper vacuum, check all threaded
fittings extending from the kettle couplings
(right and rear) for leaks and tightness.
1)
Check pressure relief valve for leaks
from poor valve seating or built up
debris. Manually operate the valve
several times to reseat. Repeat venting
procedure.
2)
If pressure relief valve is
malfunctioning, install a replacement
and check for proper operation.
FILLING THE RESERVOIR JACKET
Certain procedures in this section
require electrical test or
measurements while power is
applied to the machine. Exercise
extreme caution at all times and
follow Arc Flash procedures. If test
points are not easily accessible,
disconnect power and follow
Lockout/Tagout procedures, attach
test equipment and reapply power to
test.
NOTE:
The reservoir water level must be maintained
high enough to submerge the heating element. If low
water light comes on during use, the level may be
below water level probe (LLCO) and must be
replenished before heating can continue. The low
water light will come on when kettle is tilted.
When filling reservoir jacket, use only distilled water.
Partial Refill
1.
Place kettle in full upright position.
2.
Turn power switch on. If low water light is on,
continue with procedure.
3.
Set temperature dial to lowest setting.
4.
Open pressure relief valve until reservoir jacket
is completely vented.
5.
Remove ½" pipe plug from the reservoir jacket fill
elbow at back of kettle.
A.
Insert funnel into the opening and slowly
add water until low water light turns off
(LLCO probe is satisfied).
B.
Turn power switch off.
Electric Countertop Tilting Kettles, K6ETT, K12ETT, K20ETT - SERVICE PROCEDURES AND ADJUSTMENTS
F35496 Rev. A (1117)
Page 18 of 28