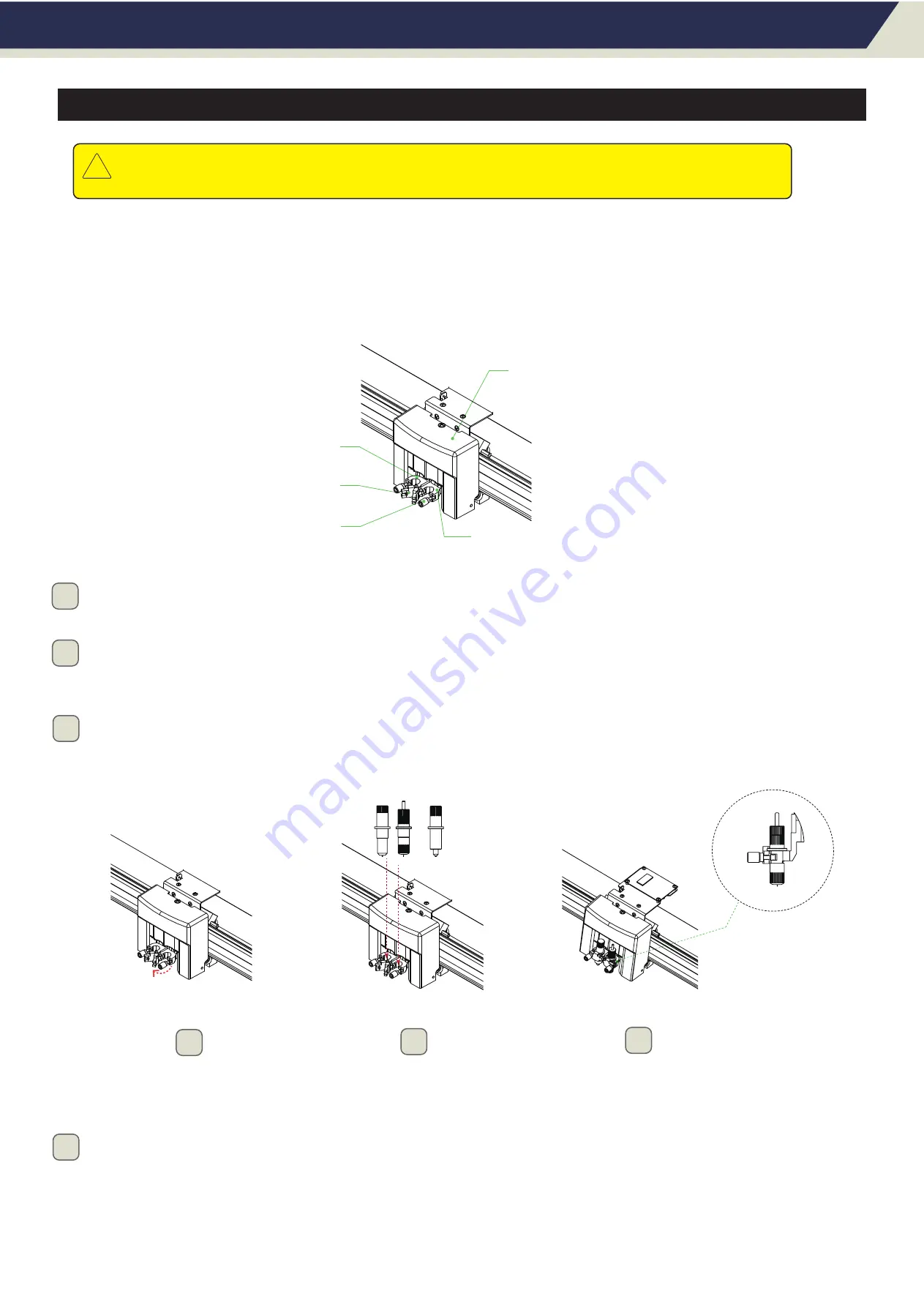
Chapter 2: Installation Equipment
2.4 Attaching a tool
1
1
2
2
3
3
First,Loosen the tool holder screw.Release tool cover.
Finally, make sure that the tool bracket is engaged on the tool's flange, and then tighten the screw.
Second,while pushing up the tool holder, push the tool into the holder until the flange of tool completely
touches the upper part of the holder
.
When pushing the tool holder with your fingers, the blade tip may be protruding.
Take care not to cut your fingers.
!
caution
When mounting the tool in the tool holder, please note the following.
• Push the tool all the way into the holder until its flange contacts the upper part of the holder and then tighten
the screw firmly.
• To prevent injury, avoid absolutely touching the tool immediately after the cutting plotter is turned on or whenever
the tool is moving.
* Removing the tool
When removing the tool, turn the tool holder screw counterclockwise to remove the tool.
Tool Carriage
Tool holder 1
Tool holder 2
Tool holder screaw
Bracket hold tool
...
4
Page 16