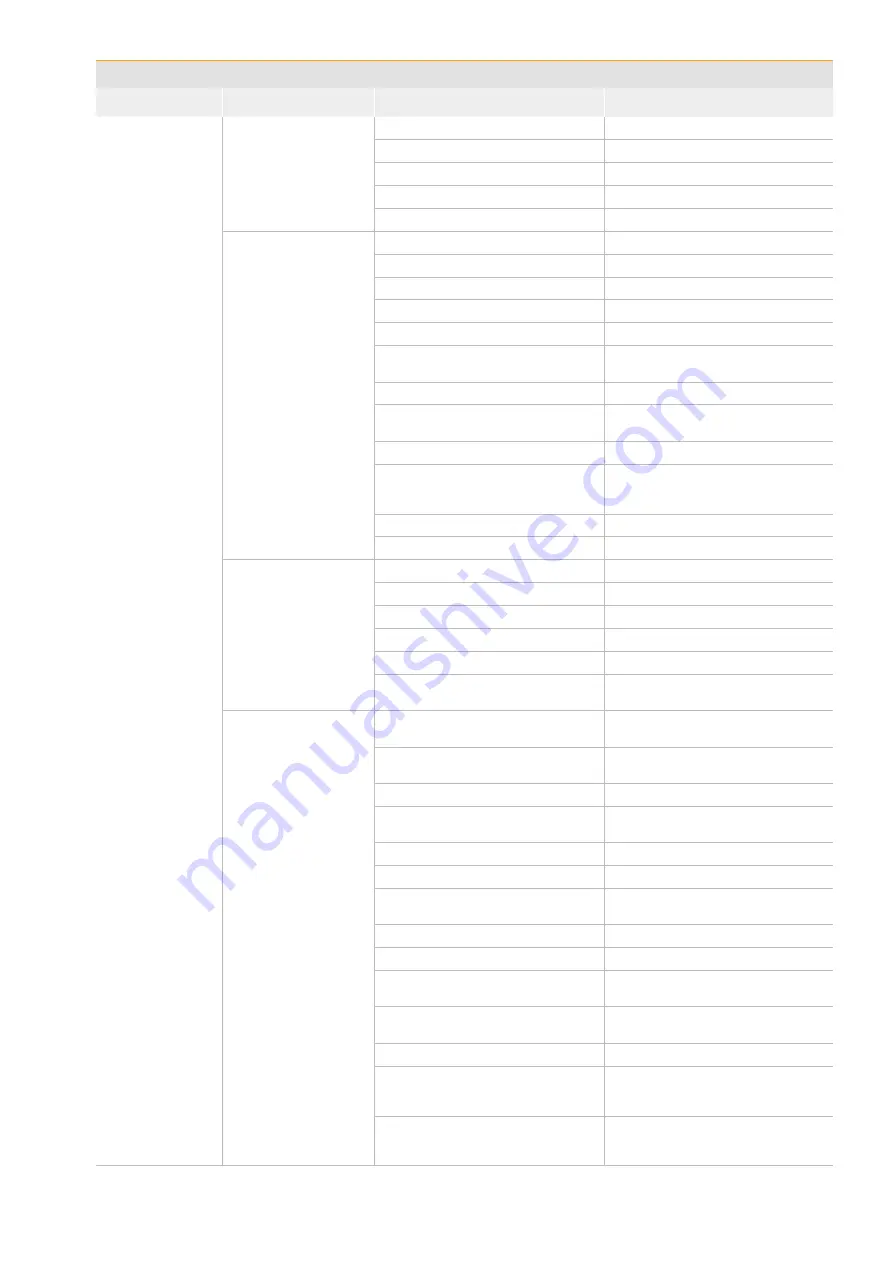
31
32
OIMM – VENTUS PRO
TROUBLESHOOTING
PROBLEM
SYMPTOMS
POSSIBLE CAUSE
OTHER CAUSES OR ACTION
NOISE
Impeller hits inlet ring
Damaged impeller
Correct or change impeller
Damaged inlet ring
Correct or change inlet ring
Impeller not centered on shaft
Center the impeller
Shaft loose in bearing
Tighten shaft
Impeller loose on shaft
Tighten impeller
Noise from drive
system
Belts too loose
Adjust belt tension
Belts too tight
Adjust belt tension
Belts wrong section
Install correct section belts
Belts worn
Change belts
Belts oily or dirty
Clean belts
Belts length different (multi-belt
drives)
Install correct belts.
Drive systems hits drive guard
Check drive system and drive guard.
Fan, motor or motor base fixing
bolts loose
Tighten bolts
Pulleys misaligned.
Align pulleys
Variable speed pulleys not adjusted
so each groove has different
diameter.
Adjust each groove to same
diameter for required air flow
Fan shaft bent
Correct or change shaft
Motor bearings damaged
Change bearings
Noise from bearings
Loose on support
Tighten bearings
Loose on shaft
Tighten shaft
Bearings worn or damaged
Change bearings
Bearings need lubrication
Lubricate bearings
Foreign material inside bearing
Clean bearings
Corrosion between shaft and
bearings
Clean corrosion, if the shaft worn
change shaft
High air velocity
Ductwork undersized for application Check duct size and revise if
necessary
Fan size is too small for application Change size of equipment, revise if
necessary
Coil with insufficient face area
Registers and/or grilles undersized
for application
Worn or damaged impeller
Change impeller
Unbalanced impeller
Balance impeller
Foreign material in fan housing or
inside the unit
Clean fan housing
Vibrating ductwork
Stiffen ductwork
Vibrating casing parts
Isolate vibrating parts properly
Vibrating parts not isolated from
building
Obstruction in dampers, registers,
grilles
Check and remove any obstructions
Leaks in casing and ductworks
Seal leaks
Sharp elbows
Remove sharp elbows, install
elbows with proper radius and
turning vanes
Sudden expansion or reduction in
ductwork
Install expansion/reduction sections
with proper expansion/reduction
angles