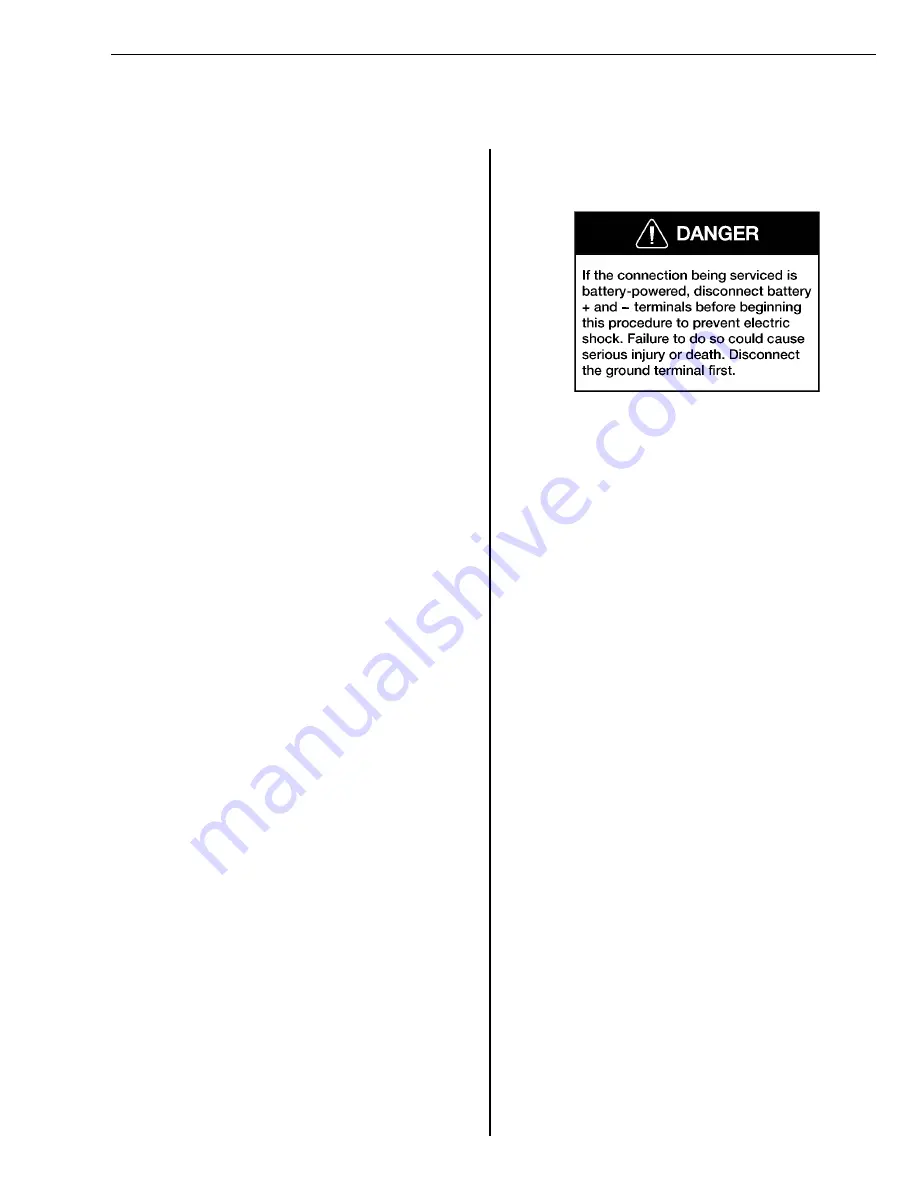
Group 30 Electrical System—VNL, VNM
Service Procedures
Service Procedures
General Work Practices and
Cautions
General Recommendations
This manual provides electrical reference information, as
well as suggested methods for service and maintenance.
The recommended schedule for maintenance is outlined
in the Operator’s Manual for each vehicle.
Continual electrical problems may be the result of incom-
plete or inadequate diagnosis and improper repairs. Un-
less the root cause of a problem is determined, it will fail
again, i.e., a blown fuse will blow again unless the cause
of the overload is located. A battery damaged by over-
charging will fail again if the regulator is not reset. Make
every effort to determine the root cause of a failure.
Checking the following items will help to eliminate some
of the most common problems found in heavy duty trucks.
•
Shorts in cables and harnesses: The mechanic must
be concerned about proper routing and the security of
cables and harnesses. Cables that rub and chafe ob-
jects or flap around will ultimately lead to short circuit
or open circuit conditions (see
Circuit Malfunctions in
this manual).
•
Corrosion in sockets and connectors is caused by
acids and road salt reacting with the copper. Con-
nections exposed to concentrated splash, spray and
wheel wash should be sealed tightly. Periodically
check to see that all wiring connections are clean
and tight.
•
Corrosion is due mainly to poor wire splicing. Wires
should not be spliced by twisting them together and
wrapping with tape. The proper way to splice two
wires together is outlined in Service Procedures.
Several hand crimped connectors are available on
the market which will result in a good joint or union,
but most do not provide a water tight seal.
Important: To splice a wire or repair one that is
frayed or broken, always use rosin flux solder to
bond the splice and sealant shrink tubing to cover
all splices, joints or bare wires. Never use acid core
solder.
•
The use of dielectric grease is recommended for all
terminals exposed to the weather: salt, dirt, or water.
Dielectric grease is needed to provide protection
against moisture and the elements.
W3000821
To apply dielectric grease, remove the connector
from the connection. If corroded, clean with a wire
brush. After cleaning, spray a light film of dielectric
grease on the terminal to seal out salt, dirt, and
moisture.
•
When replacing wires, it is important that the correct
size wire be used as shown on the applicable wiring
diagram or parts book. Each harness or wire must be
held securely in place to prevent chafing or damage
to the insulation due to vibration. Never replace a wire
with one of a smaller size; never replace a fusible link
with a wire that is larger, or of a different length.
•
A high resistance condition in a circuit is often dif-
ficult to find. Symptoms of high resistance include
dim or flickering lamps or inoperative components
(since current decreases when resistance increases,
the components may not be receiving enough current
to operate properly). The first step in finding a high re-
sistance problem should be a visual check of all con-
nectors and wires in the circuit. Corrosion or loose,
dirty connections could cause a high resistance prob-
lem.
If a problem is found, repair it and verify correct circuit
operation. If this does not fix the problem, use a digital
multimeter to check for voltage drop at each of the
components in the circuit.
•
Many problems are the result of poor grounds. Poor
grounds can cause open circuits or intermittent fail-
ures.
•
Do not use test probes. Pricked holes from test
probes/test lights cause future problems (corrosion)
by piercing wire insulation.
43