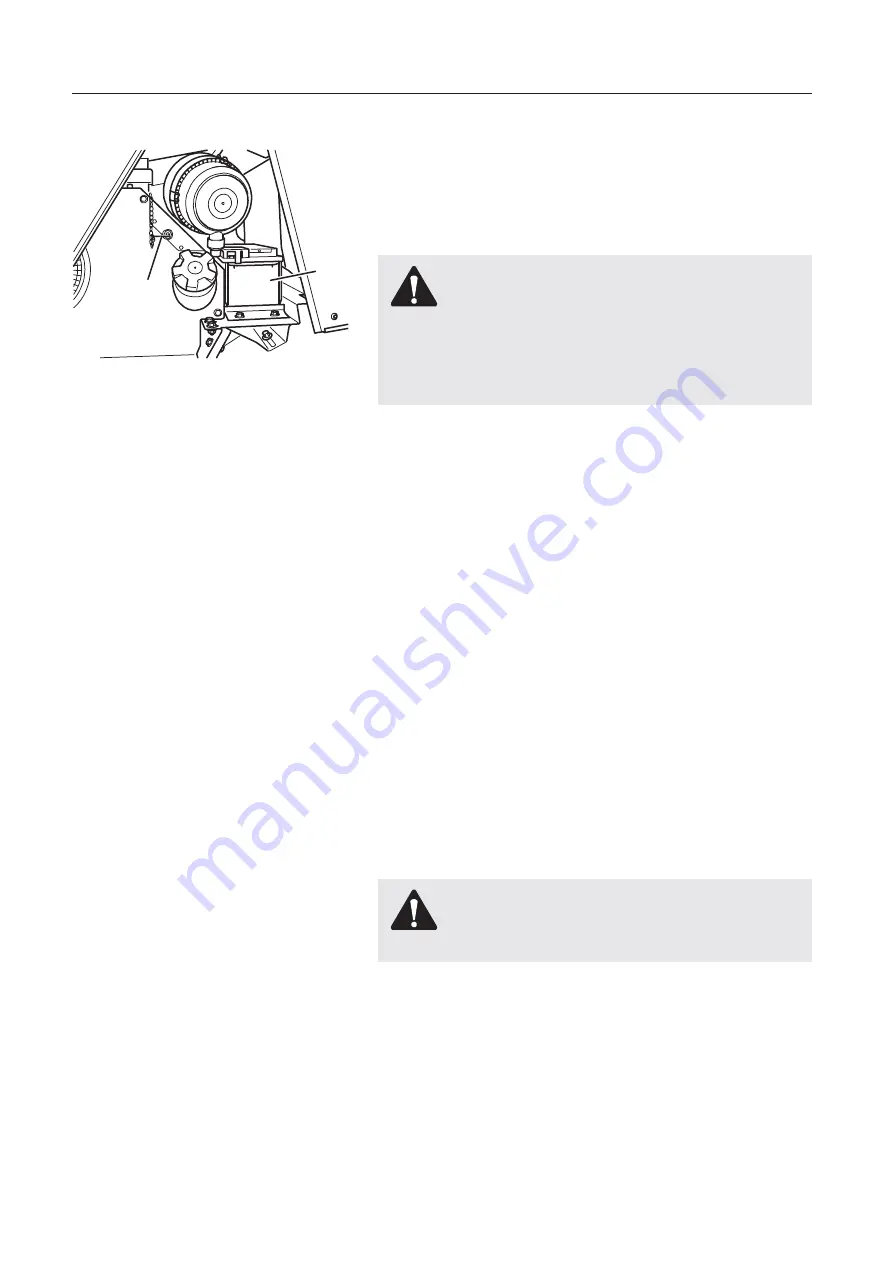
Maintenance
90
Electrical system
Battery
The battery (1) is located on the right hand side in the engine com-
partment. The battery is maintenance-free and environmentally
friendly. Its double cover with acid separator does not allow any
acid mists to escape to the outside.
Battery disconnecting switch
For longer resting periods of the machine and during repair
work on the electric system the battery disconnecting switch
(2) must be switched off.
Three-phase generator
The engine is fitted with a three-phase generator. The battery
disconnect switch must therefore be switched on when the
engine is running. When switching the battery disconnecting
switch or the starter switch off while the engine is running,
this may cause damage to the generator.
– The connecting poles of the battery must never be mixed up by
mistake. The poles are distinctly marked with (+) or (-). Incor-
rect connection immediately damages the rectifier in the gener-
ator. Before disconnecting battery cables shut down the electric
power by the battery disconnecting switch.
– In case of a fault in the electric system, e.g. a faulty regulator,
compensate the increased water consumption of the battery.
– Unscrew the caps and fill in distilled water up to approx.
10...15 mm / 0.4-0.6' in above the lead plates.
– Turn the plugs back in hand tight.
– Check whether cable lugs and poles are clean, well tightened
and greased with vaseline or similar.
Electric welding
For electric welding the earth terminal must be connected
directly to the part to be welded. Disconnect the battery com-
pletely and pull of or unscrew all plug connections from the
central electric system.
ATTENTION!
Keep sparks and open fire away from the battery!
DANGER OF EXPLOSION
In case of contact with battery acid flush off immediately
with lots of water. In case of caustic injury of the eyes con-
tact a doctor for medical advice.
ATTENTION!
Dispose of old batteries environmentally.
M200091A
1
2
Summary of Contents for L20B
Page 1: ...OPERATOR S MANUAL Ref No VOE21A1000083 English CST Printed in Sweden ...
Page 26: ...Safety 24 Transport ...
Page 40: ...Indicators and control elements 38 Levers and switches ...
Page 48: ...Travel 46 Starting the engine ...
Page 90: ...Maintenance 88 Maintenance every 1500 operating hours ...
Page 110: ...Alphabetic register 108 Ref No VOE21A1000083 English CST Volvo Konz Printed in Sweden ...