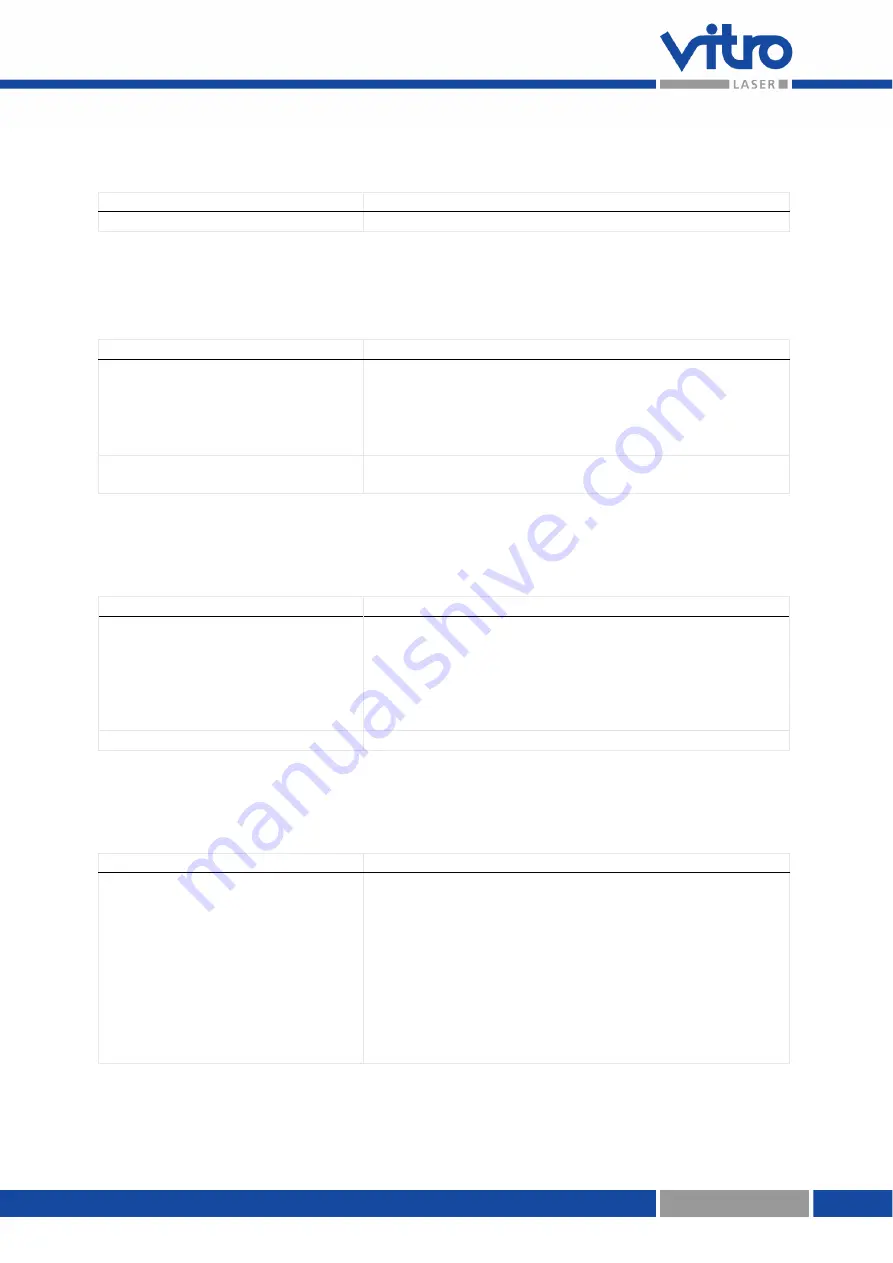
Vitrolux E / F
Troubleshooting
Stand 5/12
Page 50 of 58
6.2.5 Software massage „Door open“ in closed
Possible cause:
Check/fix:
Broken door contact
Replace or contact technician
6.2.6 Engraving moved in glass
Possible cause:
Check/fix:
Legoboard moved/loosened
Drive table on start position and check whether pilot
laser appears in the right place.
Check if the Legoboard is still firmly connected with the
table.
Start position values changed
Redefine values for starting position - see software
manual
6.2.7 Motives with defects always in the same place
Possible cause:
Check/fix:
Dirt particles on the lens
The clean the optics with soft cloth and alcohol.
Engrave flat glass with white pattern over the entire
scan area without tiling (approx. 70 mm Ø), to
determine whether the error is resolved.
If error still exists then
Optics defekt
Replace lens, must by made service technicians
6.2.8 Motives with streaks or strips
Possible cause:
Check/fix:
Tension in the glass or surface
badly polished
Stresses inside the glass can be checked with the glass
tension tester (see special equipment).
Continuous strip can be caused by light waves in the
surface of the glass, which deflect the laser beam.
You can check this by mirroring straight edges - e.g.
fluorescent tubes - in the surface can and watch for
deformations.
If deformation or tension is noticed, the glass is not
useable for subsurface engraving.