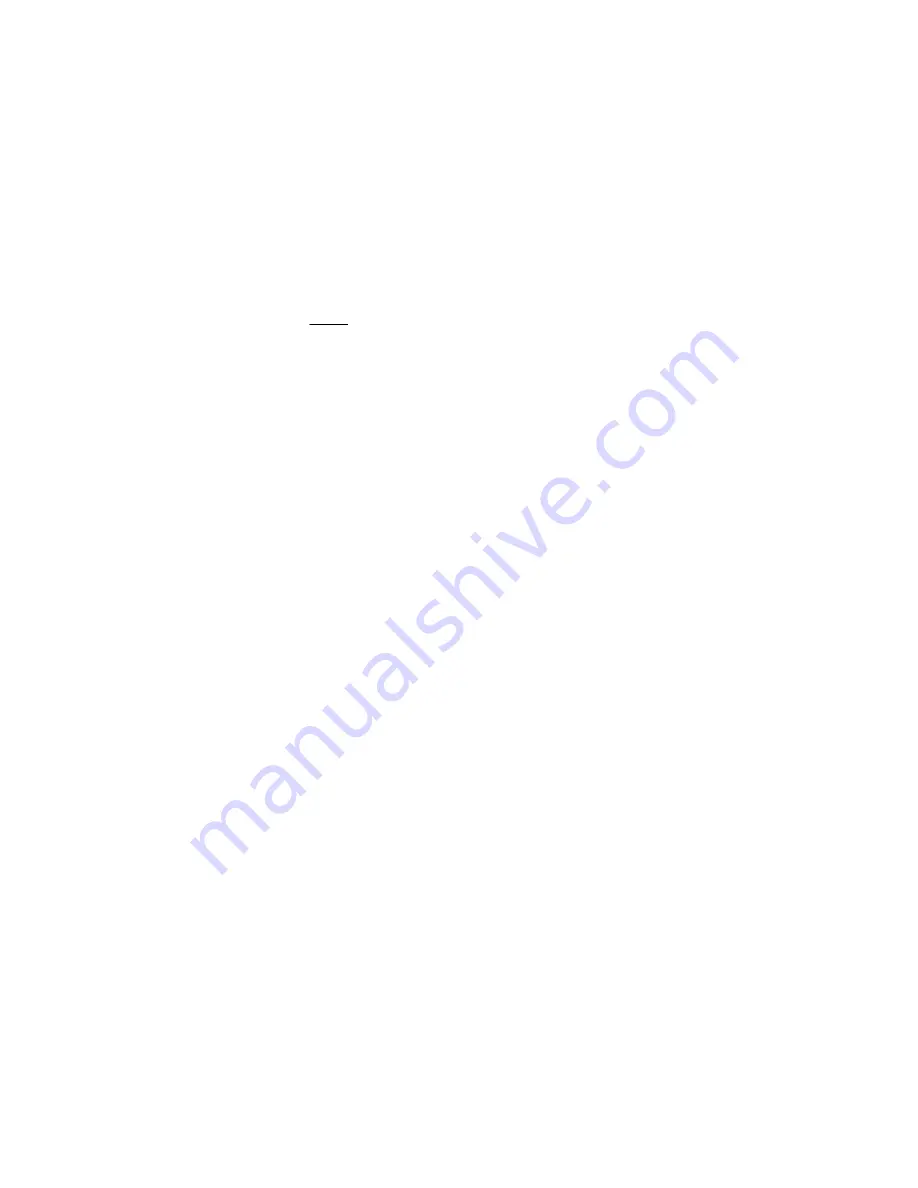
12
socket’s notch should be aligned with the sensor’s orientation tab. Should a solvent leak occur
in the TDA module, the chemical sensor’s output signal will increase and exceed a set threshold
level. This will cause the vapor bar LED on the front panel to flash and it turn activate a solid-
state relay. This relay will provide a contact closure to shut down the external solvent pump.
VISCOMETER PLUMBING AND FLOW PATH
Refer to the Viscometer Plumbing Diagram in
Figure 3
for the flow through the system.
Poiseulle’s Law of flow through tubes requires that the pressure drop across any tube is
inversely proportional to the diameter raised to the fourth power.
[A.1-6]
P
LQ
R
∝
8
4
π
where
L
= length,
Q
= flowrate, and
R
= radius
Note that some of the tubing shown in
Figure 3
is small bore (shown with fine line width)
and other tubing is wide bore (shown with wide line width). The wide bore tubing is 0.040”
diameter and the fine bore tubing is 0.010” diameter. Although the pressure drop also depends
on length, the strong dependence on bore radius or diameter means that the wide bore tubes
shown have negligible resistance compared to the narrow bore tubes. Only with this
relationship clearly in mind can one understand the flow patterns described below.
The viscometer differential pressure transducers, having positive and negative cavities,
are purged using electronic solenoids from the front panel of the instrument. These purge
procedures must be carried out independently
to properly redirect the flow through the
transducer cavities and remove air bubbles and/or purge the cavities with new mobile phase
solvent. Normal flow is directed into the viscometer and split at a tee connecting capillaries R
1
and R
2
. After closing the DP purge ports, the flow is directed only through the four capillary
bridge R
1
- R
4
. The IP
+
cavity is in series before the bridge and is purged by the Refractometer
Purge valve. The IP
-
cavity is in series after the bridge and is continuously purged by the
viscometer waste flow.