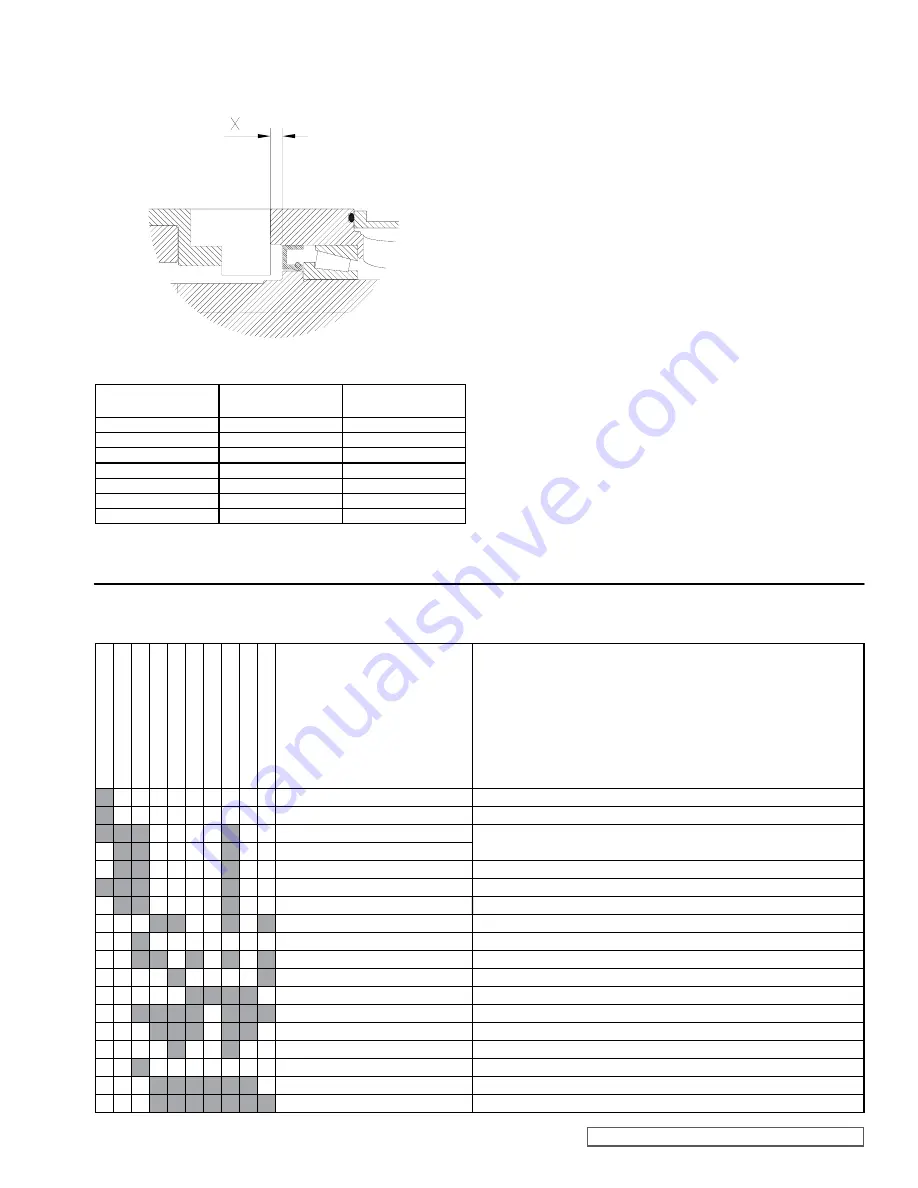
fIGURE 128
SECTION TSM 288
ISSUE
A
PAGE 33 OF 36
6.3 lIP-sEal sETTING
dIsTaNCEs
Pump
Model
dimension
“X” (mm)
dimension
“X” (inch)
SLAS
4
0.16
SLBL
6
0.24
SLCS
5
0.20
SLDL
6
0.24
SLES
3
0.12
SLFL
8
0.31
SLGS
7
0.28
6.4 lUbRICaNTs
The recommended lubricant for use in the SL Series is an
EP00 grade, lithium based, extreme pressure grease intended
for ‘sealed for life’ units. Suitable for operating temperatures
between –30°C and 120°C (-22°F to 266°F) and a base
viscosity in the region of 200 cSt at 40°C (104°F).
The unit is shipped as standard with the recommended grade
listed above. Refer to manufacturers recommended operating
conditions concerning limitations, servicing and application. In
case of doubt, please consult the factory for details.
SLA = 0.25 Liters .......... (0.066 US gallons)
SLB = 0.7 Liters ............ (0.184 US gallons)
SLC = 1.1 Liters ............
(0.29 US gallons)
SLD = 2.2 Liters ............ (0.58 US gallons)
SLE = 4.6 Liters ............ (1.21 US gallons)
SLF = 8.2 Liters ............ (2.16 US gallons)
SLG = 12 Liters ............ (3.16 US gallons)
During the filling operation, lubricant should be directed at
the
front bearings to ensure good circulation and coverage in this
area.
Care should be taken not to overfill the gearbox.
6.5 MaTERIal sPECIfICaTION
Rotors ............................ 316L Stainless Steel
Casing ........................... 316L Stainless Steel
Shafts ............................ 316L Stainless Steel
Head .............................. 316L Stainless Steel
Rotor Retainer ............... 316L Stainless Steel
Bearing Housing ............ Grade 220 Grey Cast Iron, Coated
No
flow
Irregular
flow
Under Capacity
Pump Overheats
Motor Overheats
Excessive Rotor W
ear
Excessive
seal W
ear
Noise / V
ibration
seizure
Pump
stalls on
startup
Causes
action
Incorrect Direction of Rotation
Reverse Motor
Pump Not Primed
Expel Gas From Suction Line / Pump Chamber & Prime
Insufficient NPSH Available
Increase Suction Line & Static Suction Head Diameter. Simplify Suction
Line & Reduce Length. Reduce Pump Speed & Product Temperature
Product Vaporizing in Suction Line
Air Entering Suction Line
Remake Pipework Joints
Gas in Suction Line
Expel Gas From Suction Line / Pump Chamber
Insufficient Static Suction Head
Raise Product Level to Increase Static Suction Head
Product Viscosity Too High
Decrease Pump Speed / Increase Product Temperature
Product Viscosity Too Low
Increase Pump Speed / Increase Product Temperature
Product Temperature Too High
Cool Product / Pumping Chamber
Product Temperature Too Low
Heat Product / Pumping Chamber
Unexpected Solids in Product
Clean System / Fit Strainer on Suction Side of Pump
Discharge Pressure Too High
Check for Blockages / Simplify Discharge Line
Casing Strained by Pipework
Check Pipe Alignment / Support Pipework
Pump Speed Too High
Decrease Pump Speed
Pump Speed Too Low
Increase Pump Speed
Seal Flush Inadequate
Increase Seal Flush to Required Pressure / Flow
Bearing / Timing Gear Wear
Replace Worn Components
6.6 TROUblE sHOOTING