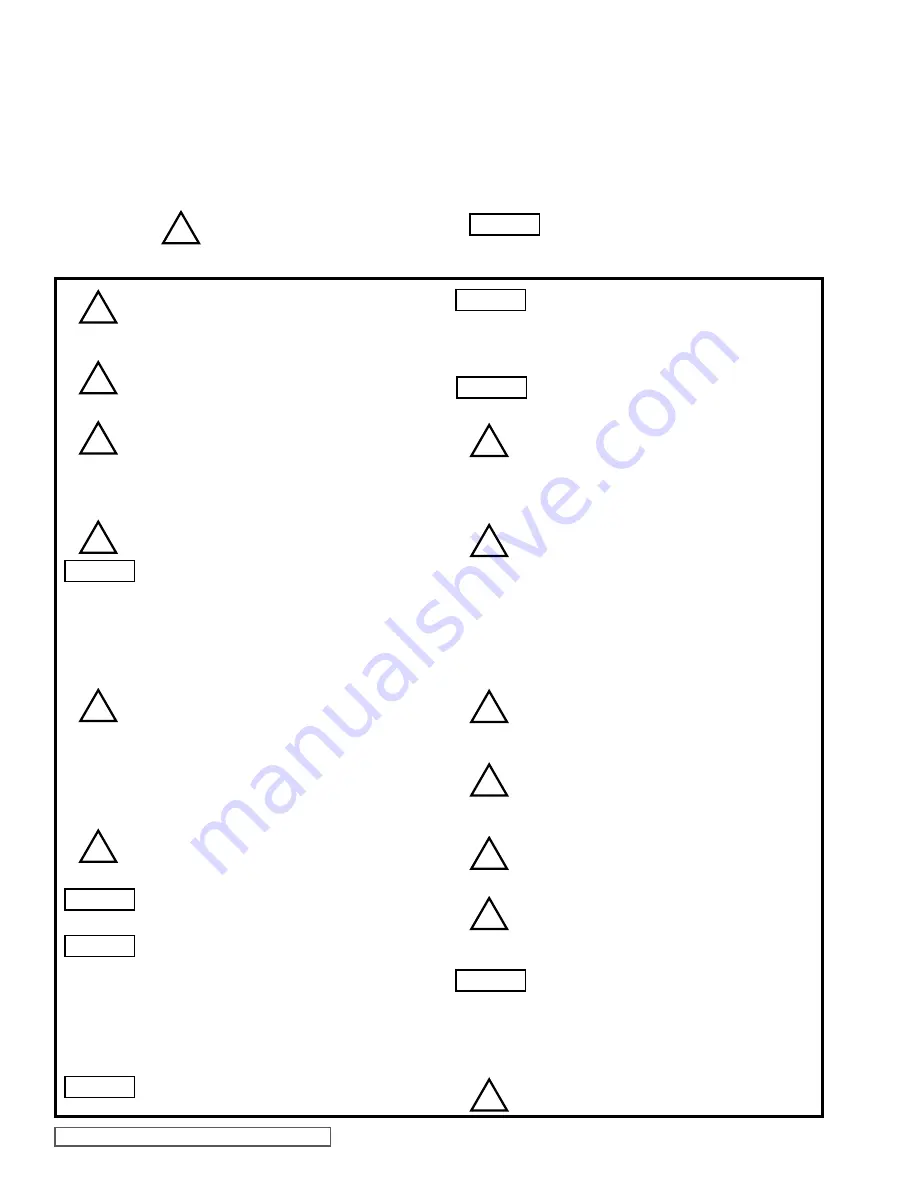
SECTION TSM 288
ISSUE
A
PAGE 2 OF 36
dO NOT OPERaTE PUMP If:
- The head is not installed correctly.
- Any guards are missing or incorrectly installed.
- The suction or discharge piping is not connected.
dO NOT
place fingers, etc. into the pumping chamber
or its connection ports or into any part of the gearbox if
there is
aNY
possibility of the pump shafts being rotated.
Severe injury will occur.
dO NOT
exceed the pumps rated pressure, speed, and
temperature, or change the system/duty parameters
from those for which the pump was originally supplied,
without confirming its suitability for the new duty. Running
the pump outside of its operating envelope can cause
mechanical contact in the pump head, excessive heat
and can represent a serious risk to health and safety.
Installation and operation of the pump must always
comply with health and safety regulations.
A device must be incorporated into the pump, system,
or drive to prevent the pump exceeding its stated duty
pressure. It must be suitable for both directions of pump
rotation where applicable. Do not allow pump to operate
with a closed/blocked discharge unless a pressure
relief device is incorporated. If an integral relief valve is
incorporated into the pump, do not allow re-circulation
through the relief valve for extended periods, refer to
section 3.8
The mounting of the pump or pump unit should be solid
and stable. Pump orientation must be considered in
relation to drainage requirements. Once mounted, shaft
drive elements must be checked for correct alignment.
Rotate pump shaft by at least one full revolution to ensure
smoothness of operation. Incorrect alignment will produce
excessive loading and will create high temperatures and
increased noise emissions. It may also be necessary to
earth the pump to avoid the build up of a potential charge
difference that could cause a spark.
The installation must allow safe routine maintenance and
inspection (to check for leakage, monitor pressures, etc)
and provide adequate ventilation necessary to prevent
overheating.
SL series pumps are shipped fully lubricated with a lithium
based extreme pressure Grease suitable for sealed for
life units.
Before operating the pump, be sure that it and all parts
of the system to which it is connected are clean and
free from debris and that all valves in the suction and
discharge pipelines are fully opened. Ensure that all piping
connecting to the pump is fully supported and correctly
aligned with its relevant connections. Misalignment
and/or excess loads will cause severe pump damage.
This could result in unexpected mechanical contact in
the pump head and has the potential to be a source of
ignition.
Be sure that pump rotation is correct for the desired
direction of flow
(refer to section 3.1).
Do not install the pump into a system where it will run
dry (i.e. without a supply of pumped media) unless it is
equipped with a flushed shaft seal arrangement complete
with a fully operational flushing system. Mechanical seals
require a thin fluid film to lubricate the seal faces. Dry
running can cause excessive heat and seal failure.
Pressure gauges/sensors are recommended, next to
the pump suction and discharge connections to monitor
pressures.
Caution must be taken when lifting the pump. Suitable
lifting devices should be used as appropriate. Lifting eyes
installed on the pump must only be used to lift the pump,
not pump with drive and/or base plate. If pump is base
plate mounted, the base plate must be used for all lifting
purposes. If slings are used for lifting, they must be safely
and securely attached.
dO NOT
attempt any maintenance or disassembly of the
pump or pump
unit without first ensuring that:
- The pump is fully isolated from the power source
(electric, hydraulic, pneumatic).
- The pumping chamber, pneumatic relief valve and
any shaft seal support system are depressurized and
purged.
- Any temperature control devices (jackets, heat-tracing,
etc) are fully isolated, that they are depressurized and
purged, and components are allowed to reach a safe
handling temperature.
dO NOT
attempt to dismantle a pressure relief valve,
which has not had the spring pressure relieved, is still
connected to a pressurized gas/air supply or is mounted
on a pump that is operating. Serious personal injury or
death and/or pump damage may occur.
dO NOT
loosen or undo the head, any connections to the
pump, shaft seal housings, temperature control devices,
or other components, until sure that such action will not
allow the unsafe escape of any pressurized media.
Pumps and/or drives can produce sound power levels
exceeding 85dB (A) under certain operating conditions.
When necessary, personal protection against noise must
be taken
Avoid any contact with hot parts of pumps and/or drives
that may cause injury. Certain operating conditions,
temperature control devices (jackets, heat-tracing, etc.),
bad installation, or poor maintenance can all promote
high temperatures on pumps and/or drives.
When cleaning, either manually or by an in-line cleaning
method, the operator must ensure that a suitable
procedure is used in accordance with the system
requirements. During a in-line cleaning cycle, a pump
differential pressure of between 2 and 3 bar (30 and 45
psi) is recommended to ensure suitable velocities are
reached within the pump head. The exterior of the pump
should be cleaned periodically.
Surface temperature of pump is also dependent on the
temperature of pumped medium.
1.0 safETY INfORMaTION
danger -
Failure to follow the listed
precautionary measures identified by
this symbol may result in serious injury
or death.
Warning -
Safety instructions which
shall be considered for reasons of safe
operation of the pump or pump unit and/
or protection of the pump or pump unit
itself are marked by this symbol.
INCORRECT INsTallaTION, OPERaTION OR MaINTENaNCE Of EQUIPMENT MaY CaUsE sEVERE
PERsONal INJURY OR dEaTH aNd/OR EQUIPMENT daMaGE aNd MaY INValIdaTE THE WaRRaNTY.
This information must be read fully before beginning installation, operation or maintenance and must be
kept with the pump. all installation and maintenance must be undertaken by suitably trained or qualified
persons only.
symbol
legend :
!
!
!
!
!
!
!
!
!
!
!
!
!
!
WaRNING
WaRNING
WaRNING
WaRNING
WaRNING
WaRNING
WaRNING
WaRNING