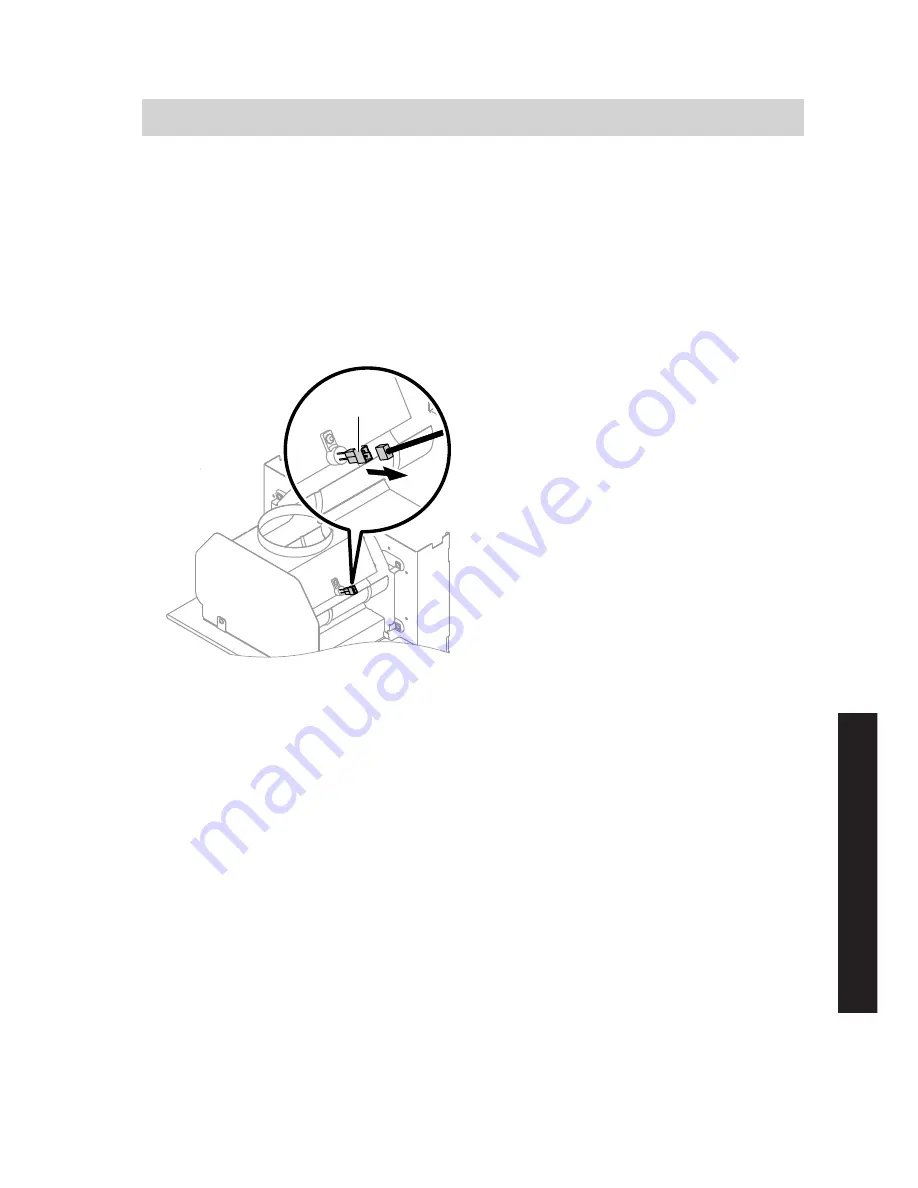
29
Note
After no later than approx. 2 min, the
flue gas monitoring device should
switch off the burner and should not
switch it on again automatically until
at least 15 min later. For safety rea-
sons, the burner will be locked out for
between 18 to 20 min.
5.
A
■ If the flue gas monitoring device
switches the burner off later than
after 2 min, check flue gas monitor-
ing sensor
A
(see page 38) and
replace it if required, e.g. if there
are signs of corrosion.
■ If the flue gas monitoring device still
does not shut down the burner even
after a new flue gas monitoring sen-
sor has been installed, or if the
burner does not start, replace the
control unit.
6.
Shut down the boiler.
7.
Clear the aperture and push the flue
pipe onto the draught hood.
Commissioning, inspection, maintenance
Further details regarding the individual steps
(cont.)
5441 514 UAE
Service