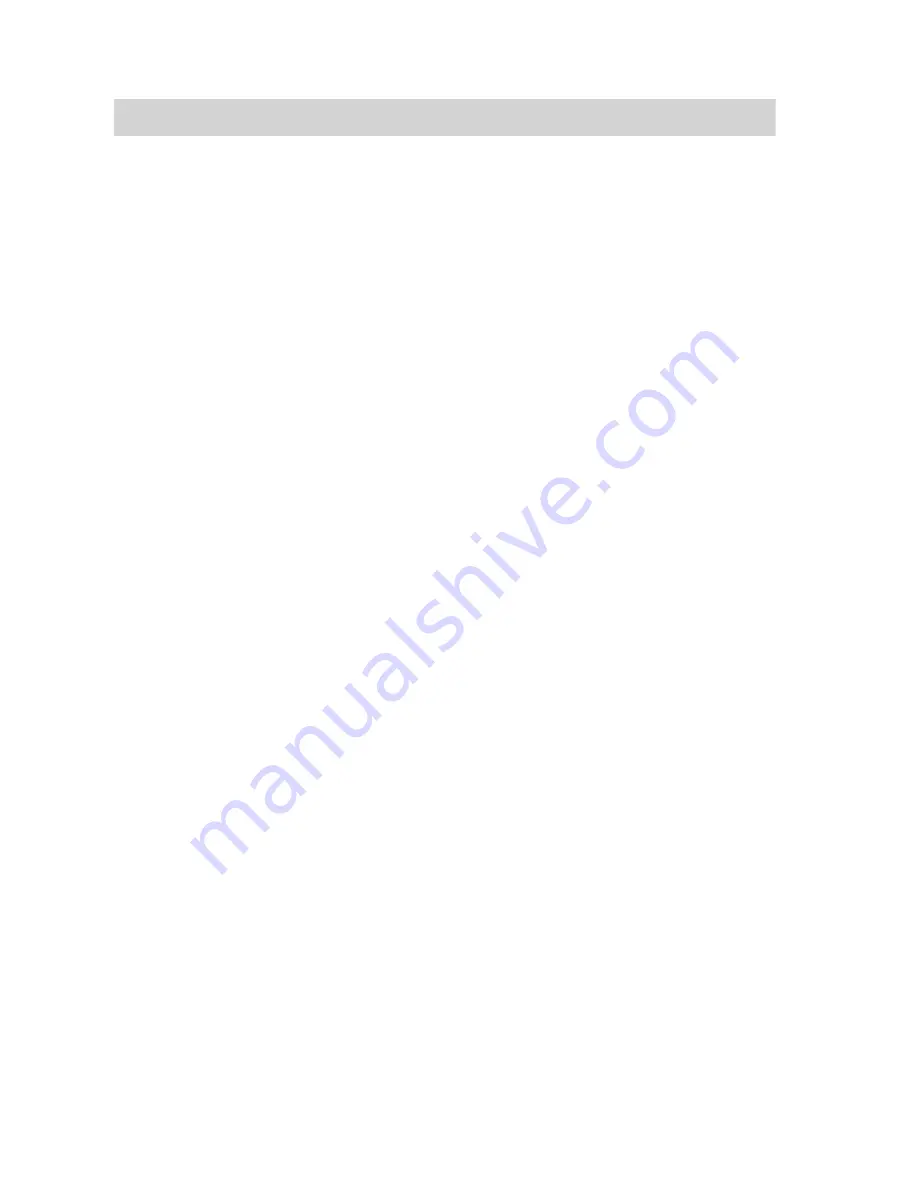
192
A
Acknowledging a fault display..........120
Actuator test.....................................118
Anode, checking................................60
Anode, replacing................................60
Assembly.........................................171
B
Boiler, draining on the DHW side.......58
Boiler water temperature sensor......140
Boosting DHW heating.....................151
Brief scans.......................................113
Burner gasket.....................................51
Burner gauze assembly.....................51
Burner installation..............................52
Burner removal..................................50
C
Calling up fault messages................121
Calling up the service level..............111
Calling up the service menu.............111
Cleaning the heating surfaces.....52, 55
Code 1
■ Calling up........................................77
Code 2
■ Calling up........................................89
Codes for commissioning...................64
Combustion chamber, cleaning. . .52, 55
Combustion controller......................166
Combustion quality, checking............63
Commissioning..................................35
Condensate drain...............................53
Connection diagrams.......................168
Control unit.......................................149
Control unit maintenance position....137
Cylinder cleaning...............................59
Cylinder temperature sensor............140
D
Date, setting.......................................38
Diaphragm expansion vessel.............36
E
Electronic combustion controller......166
Extension
■ AM1..............................................154
■ EA1...............................................156
■ Internal H1....................................152
■ Internal H2....................................153
Extension kit for heating circuit with
mixer ...............................................146
External blocking..............................159
External demand..............................160
F
Fault codes......................................122
Fault history.....................................120
Fault manager....................................74
Fault memory...........................120, 121
Fault messages, calling up..............120
Faults...............................................120
Fill function.......................................161
Fill water.............................................35
Flow temperature sensor.................140
Flue gas temperature sensor...........144
Function descriptions.......................149
Function testing................................118
Fuse.................................................146
G
Gas supply pressure..........................45
Gas train ...........................................45
Gas type.............................................43
Gas type conversion..........................44
H
Heating circuit allocation..................166
Heating curve.....................................70
Heating curve level............................72
Heating curve slope...........................72
Heating output setting........................48
Heating program changeover..........158
Heat-up time....................................164
Keyword index
Keyword index
5773 216 GB
Summary of Contents for Vitodens 222-F B2TA series
Page 12: ...12 2 5 1 4 2x 3 Installing the boiler Removing the front panels 5773 216 GB...
Page 13: ...13 1 2 SW17 Installing the boiler Siting and levelling the boiler 5773 216 GB Installation...
Page 31: ...31 4 1 5 2 2x 3 Installing the boiler Fitting the front panels 5773 216 GB Installation...
Page 194: ...194 5773 216 GB...
Page 195: ...195 5773 216 GB...