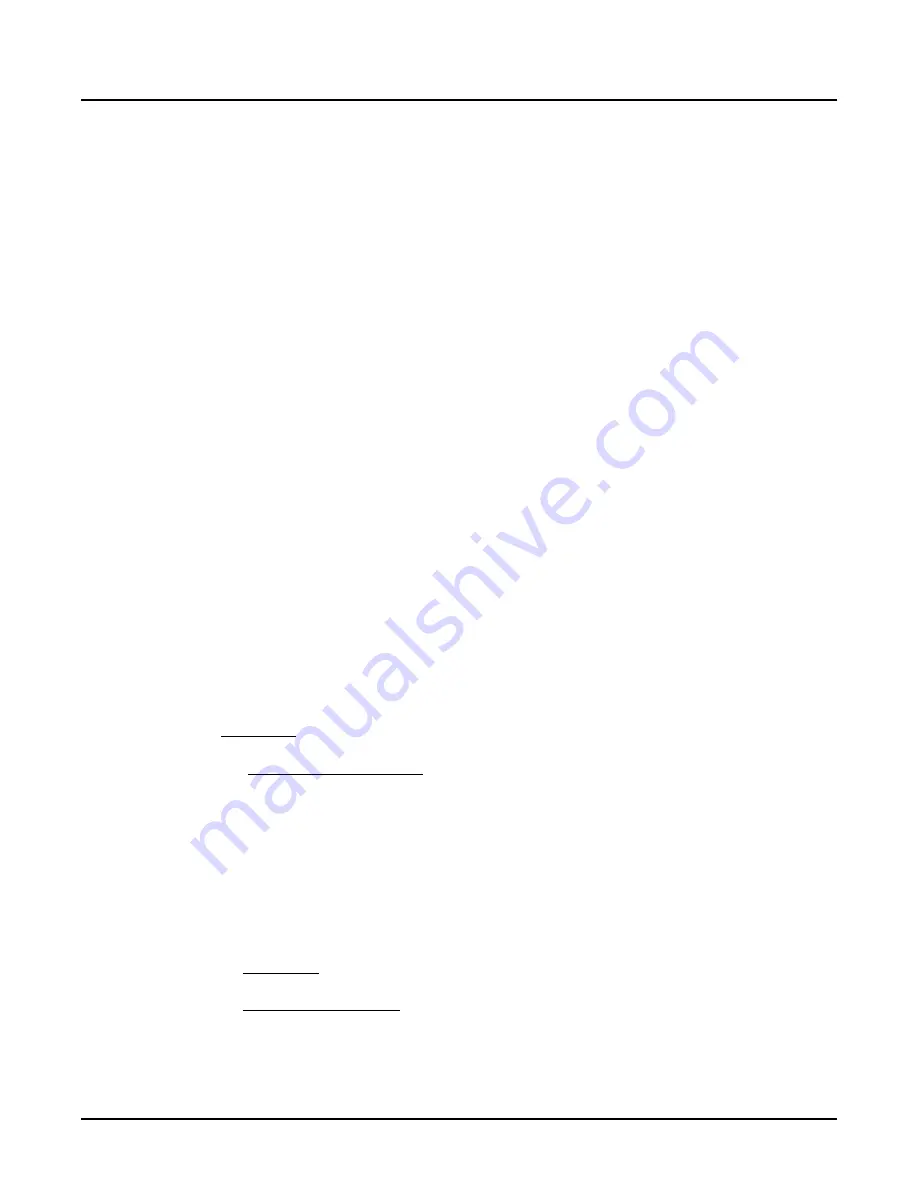
Vertiv
™
NetSure
™
802 and Vertiv
™
NetSure
™
8200 -48 VDC Power System
System Application Guide
Spec. No: 582140000
SAG582140000
Model Nos: 802
NLDB
, 802
NLEB
, 802
NL
-
B
,
Proprietary and Confidential © 2022 Vertiv Group Corp.
Revision BH, September 28, 2022
8200
NLDB
, 8200
NLEB
and 8200
NL
-
B
Page 124
4.1.15
External Control Circuits
(A)
Remote Test/Equalize: All rectifiers can be placed into the test/equalize mode by applying a loop closure
signal. The rectifiers operate in the float mode when the loop closure signal is absent.
(B)
Remote High Voltage Shutdown: The high voltage shutdown circuit on all rectifiers, as described in Paragraph
3.4.6 (E), can be activated by applying a loop closure signal.
(C)
Rectifier Emergency Shutdown and Fire Alarm Disconnect: The rectifiers can be inhibited by applying a loop
closure signal. Manual restart is required.
(D)
External "System Voltage" Meter Reading: Leads can be extended from the MCA to an external voltage source.
This is the voltage source the MCA monitors for system alarms and displays as "System Output Voltage".
(E)
Test Input: The High Voltage Shutdown and/or rectifier Emergency Stop circuits can be tested without
affecting the system by applying a test loop closure signal before applying the Remote High Voltage Shutdown
or rectifier Emergency Shutdown loop closure signal.
4.1.16
Optional MCA Relay Circuit Card, P/N 514348: Each circuit card adds six (6) Form-C external alarm relay contacts
to the system. Plugs into seven-slot card cage provided in each bay for optional MCA and LMS I/O cards.
(A)
Contact Rating: 2A at 30 VDC.
(B)
Description of Operation: The MCA provides 25 programmable function channels. Program each function
channel to alarm for selected conditions, then program each external alarm relay to activate if a specific
function channel alarms.
MCA relays can also be programmed to activate if an LMS LED channel activates.
4.1.17
Optional MCA Input/Output (I/O) Circuit Card, P/N 524550: This I/O card provides capability for monitoring of
external shunts and binary signals. Plugs into seven-slot card cage provided in each bay for optional MCA and LMS
I/O cards. Provides 1 analog input, 1 analog output (for remote plant output current monitoring), and 4 binary
inputs.
(A)
One analog input with a range of 0-50mV can be used to provide monitoring of additional load shunt or a plant
load shunt.
(B)
Four binary inputs can be used to monitor dry contact closures. When the “Alternate Current Limit” feature is
used, binary input #4 is assigned to monitor the signal used to trigger the MCA to place the rectifiers in the
Alternate Current Limit mode.
(C)
One analog output with a 50mV full scale output provides a value to indicate the “Total Load Current”
parameter of the NPS system.
(D)
The reading displayed for the NPS system parameter “Total Load Current” is derived from one of two
algorithms using multiple data sources. The algorithm and its data sources used are determined by the
presence and configuration of CAN I/O card(s) in the system.
1)
Algorithm #1: This source is used when there are no CAN I/O cards installed OR when the configuration of
all installed CAN I/O cards is set to “Distribution” mode.
“Distribution” Mode Operation:
“Total Load Current” =
NPS bay distribution node current readings,
+ CAN I/O card analog input readings,
+ LMS function channel 63 reading.
The VPS ‘
Total System Current’
reading (LMS channel A9002) will be passed to the NPS through
LMS function channel sixty-three. The function channel configuration will default to provide the
reading of the associated LMS channel for the VPS Total System Current. The NPS controller will
include the value of LMS function channel sixty-four when summing the distribution load currents
to determine its Total Load Current reading to display. (associated LMS channel A9903).
Channel F63 program line is ‘F63 = A9002’ (Vortex Total Load Current).
2)
Algorithm #2: This source is used when the configuration of at least one installed CAN I/O card is set
to “Auxiliary” mode.
“Auxiliary” Mode Operation:
“Total Load Current” =
Sum of CAN I/O card analog input readings (only input readings of cards configured for
“Auxiliary” operation are summed),
+ LMS function channel 63 reading.