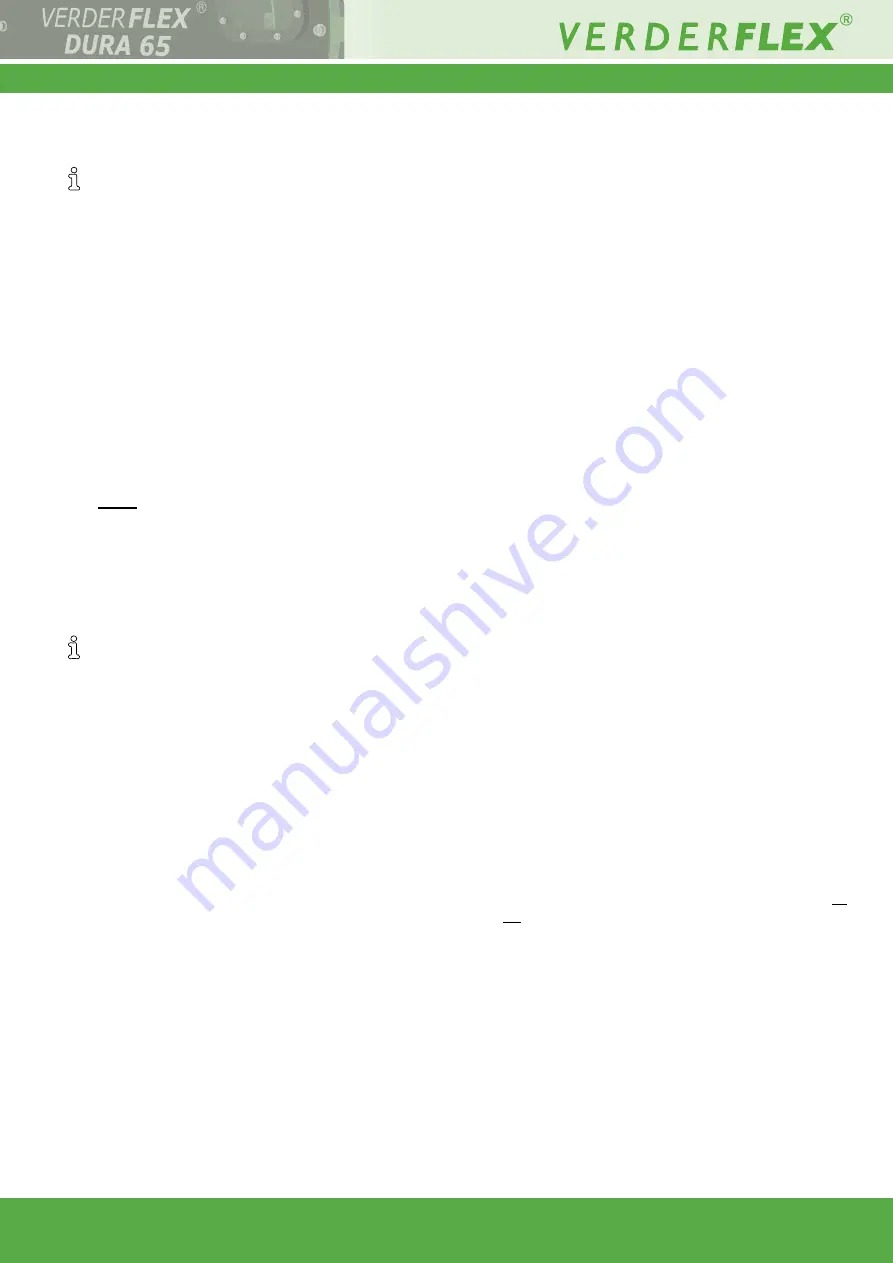
Dura 65
5 | Page
Version 1.0v-05/2021
© Verder International B.V
2 Safety
The manufacturer does not accept any liability
for damage resulting from disregard of this
documentation.
2.1 Intended Use
u
Only use the pump to handle compatible fluids as
recommended by the manufacturer (
g
Appendix A).
u
Adhere to the operating limits.
u
Consult the manufacturer regarding any other use of the
pump.
u
Pumps delivered without a motor must be fitted with a mo
-
tor in accordance with the provisions of EC Machinery Di-
rective 2006/42/EC.
Prevention of obvious misuse (examples)
u
Note the operating limits of the pump with regard to tem-
perature, pressure, flow rate and motor speed (
g
Appen-
dix A).
u
Do not operate the pump with any inlet/outlet valves closed
u
Only install the pump as recommended in this manual.
For example, the following are not allowed:
– Installing the pump without proper support.
– Installation in the immediate vicinity of extreme hot or
cold sources.
2.2 General Safety Instructions
Observe the following regulations before carrying
out any work.
2.2.1 Product Safety
•
These operating instructions contain fundamental infor-
mation which must be complied with during installation,
operation and maintenance. Therefore this operating
manual must be read and understood both by the
installing personnel and the responsible trained personnel
/ operators prior to installation and commissioning, and it
must always be kept easily accessible within the operating
premises of the machine.
Not only must the general safety instructions laid down
in this chapter on “Safety” be complied with, but also the
safety instructions outlined under specific headings.
•
Operate the pump only if it and all associated systems are
in good functional condition.
•
Only use the pump as intended, fully aware of safety and
risk factors involved and the instructions in this manual.
• Keep this manual and all other applicable documents
complete, legible and accessible to personnel at all times.
•
Refrain from any procedure or action that would pose a
risk to personnel or third parties.
•
In the event of any safety-relevant faults, shut down the
pump immediately and have the malfunction corrected by
qualified personnel.
•
The installation of the pump must comply with the require
-
ments of installation given in this manual and any local,
national or regional health and safety regulations.
2.2.2 Obligation of the Operating Company
Safety-conscious operation
• Ensure that the following safety aspects are
observed and monitored:
– Adherence to intended use
– Statutory or other safety and accident-prevention
regulations
– Safety regulations governing the handling of
hazardous substances if applicable
– Applicable standards and guidelines in the country
where the pump is operated
•
Make personal protective equipment available
pertinent to operation of the pump.
Qualified personnel
•
Ensure that all personnel tasked with work on the pump
have read and understood this manual and all other
applicable documents, including the safety,
maintenance and repair information, prior to use or
installation of the pump.
•
Organize responsibilities, areas of competence and
the supervision of personnel.
•
Have all work carried out by specialist technicians
only.
• Ensure that trainee personnel are under the
supervision of specialist technicians at all times when
working with the pump.
Safety equipment
Provide the following safety equipment and verify its
functionality:
–
For hot, cold and moving parts: safety guarding
should be provided by the operating company.
–
For potential build up of electrostatic charge: ensure
appropriate grounding if and when required.
Warranty
The warranty is void if the customer fails to follow any
Instruction, Warning or Caution in this document. Verder
has made every effort to illustrate and describe the prod
-
uct in this document. Such illustrations and descriptions
are however, for the sole purpose of identification and
do
not
express or imply a warranty that the products are mer
-
chantable or fit for a particular purpose, or that the prod
-
ucts will necessarily conform to the illustration or descrip-
tions.
Obtain the manufacturer’s approval prior to carrying out
any modifications, repairs or alterations during the war
-
ranty period. Only use genuine parts or parts that have
been approved by the manufacturer.
For further details regarding warranty, refer to terms and
conditions.