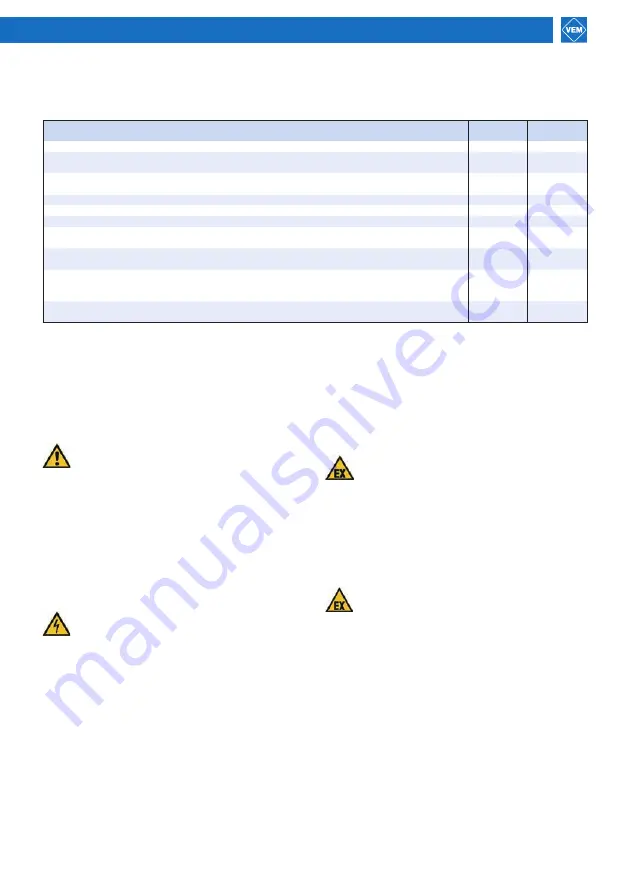
11
10
08.2017
50229 01
50229 01
08.2017
Main Inspection
The main inspection of the motor must be organized
annually after approximately 8,000 hours of operation.
The following examinations will be done at the motor:
Measure
During
operation
At
standstill
Check of the electric characteristics
X
Check of the running noises. When the motor is running, it is checked if the quiet running
has changed for the worse.
X
Check of the bearing temperatures. It is examined if the permissible bearing temperatures
will be exceeded during operation of the motor.
X
Check the intakes of the cooling air. There must be no damages.
X
X
Check of the foundations. There must be no cracks or other damages like depressions.
X
X
Check of the motor alignment. The motor alignment must be within the given tolerances.
X
Check of the fastening bolts. All bolts used for fixing mechanical and electrical connections
must be tight with the required torque.
X
Check of the insulation resistance. The insulation resistance of the winding must be sufficiently high,
according to the requirements in the maintenance manual.
X
Check of the potential, the earth and the shield connections. The examination must check if the
cables and used insulation materials are in good conditions. They must not be broken, cracked
or faulty in any other way.
X
Check the cleanness oft he surface of the motor and examine that the dust depositions are not
higher than 5mm.
X
Inspection at faults
Extraordinary operating conditions like overload or short
circuit are faults which overload the motor in electrical
and/or mechanical kind. Even natural disasters may
be a cause for extraordinary operating conditions and
faults. After all such events main inspections have to be
carried out immediately.
The necessary relubrication intervals for
anti-friction bearings are different to these
inspection intervals. They have to be ob-
served as well!
The motors up to size 315M are equipped as standard
with anti-friction bearings with life-time lubrication. From
size 315MX upwards they are equipped with relubrica-
tion devices which can be ordered for smaller motors as
option. Information about bearings and relubrication can
be found in the general installation, maintenance and
operation manual or on the name plate or relubrication
sign.
Maintenance works (without relubrication)
has to be done at standstill of the motor.
It has to be assured that the machine is
secured against reconnection and labelled
with an appropriate sign.
In addition the security advices and accident prevention
regulations of the manufacturers for the use of oils,
lubricants and detergents has to be observed!
Adjacent live parts have to be covered or secured! It
has to be assured that the auxiliary circuits like anti-
condensation heating are dead (zero potential).
For design versions with condensate drain hole please
observe that the drain plug screw has to be lubricated
with a suitable sealant (for example Epple 28) before
relocking.
The work has to be marked with an additional repair
sign including the following information:
– date,
– executive company,
– if necessary type of repair,
– if necessary marking of the person legally authorised
in accordance with the BetrSichV.
If the operations are not done by the manu-
facturer, they must be approved by a person
legally authorised in accordance with the
BetrSichV. He has to issue a written confir-
mation or mark the machine with his test
mark. Outside of Germany the relevant state
regulations have to be observed.
Painting and impregnation after repair or
maintenance work
After repainting of explosion-protected
motors or after impregnation of a complete
stator that has been rewinded, bigger layers
of paint or resin can be found on the surface
of the motors. (This can result in electro-
static charges with risk of explosion during
discharge). Nearby charging processes can
also result in electrostatic charge of com-
plete surfaces or parts of the surface. There
is the risk of explosion due to discharge.
Therefore the requirements according to
IEC/EN 60079-0: Equipment - General re-
quirements, article 7.4 and TRBS 2153 must
be observed under all circumstances: