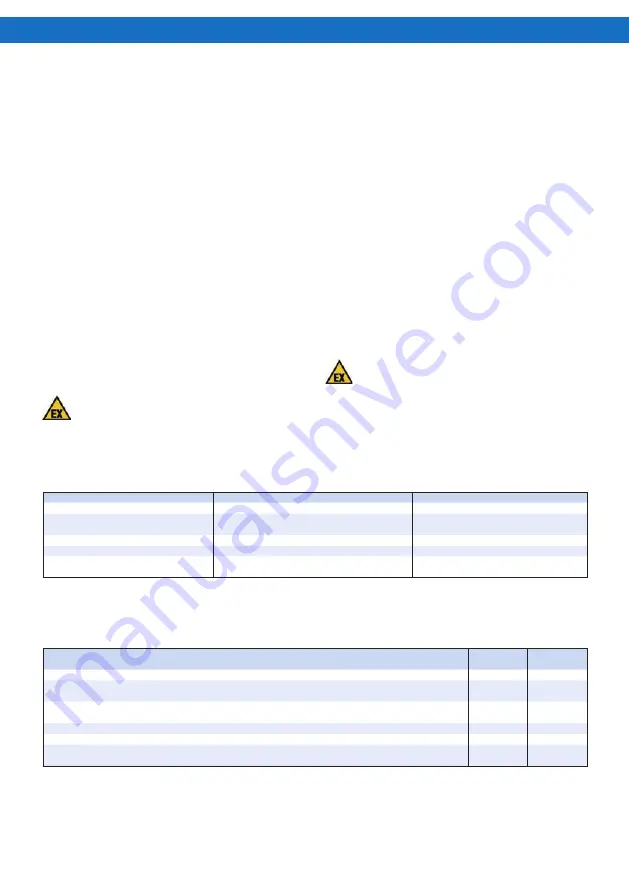
English
11
10
08.2017
50229 01
50229 01
08.2017
Maintenance and repair
In Germany maintenance, repair and changes of
explosion-protected machines have to be done taking
the workplace safety ordinance (BetrSichV), the explosi-
on protection ordinance (ExVO,11.GSGV), the security
advices and the description of the general maintenance
manual into account.
Outside of Germany the required national standards
must be applied.
More information about testing and maintenance of
electrical systems or repair and reconditioning of elec-
tric equipment can be found in IEC/EN 60079-17 and
IEC/EN 60079-19. Activities that will influence the
explosion protection such as:
– repair of the stator winding and of the terminals,
– repair of the ventilation system
– repair of the bearings and of the sealing of dust explo-
sion protected motors (Ex 2D, 3D).
This must only be done by VEM service personnel or by
authorized workshops with trained personnel which is
qualified for such tasks by industrial training, experience
and special schooling.
For dust explosion-protected motors the dust explosion
protection is depending very much on the local environ-
mental conditions. For that reason the motors have to
be checked and maintained regularly.
Thick layers of dust will result in a tempera-
ture rise on the surface of the motor due to
thermal insulation. Layers of dust on the
motors or even the total coverage should be
avoided as far as possible by suitable
installation and constant maintenance.
The indicated surface temperature of the motor is only
valid, if the dust layer on the motor is max. 5 mm. The
securing of these conditions (dust type, maximum layer
thickness and other) has to be assured. The motor shall
not be opened before a suitable time has passed to re-
duce the inner temperatures to values that are not igni-
table. If the motors have to be opened for maintenance
or repair, the work has to be done in a dust-free room if
possible. If this is not possible suitable measures have
to be taken to prohibit that dust can collect inside of
the enclosure. At disassembly take extra care that the
sealing parts like sealing, end faces and other are not
damaged.
Careful and regular maintenance, inspections and
revisions are necessary to detect and clear faults in
time, before consequential damages will happen. As
individual operating conditions can not be defined for all
applications the listed terms represent a general advice
for undisturbed operation. Individual local conditions
(degree of pollution, load, etc.) must be taken into
account when adjusting these terms. The advices within
the standards EN 60079-17 and EN 60079-19 have to
be considered as well.
Inadmissible deviations detected during
the inspections have to be eliminated imme-
diately.
What to do?
Time Periode
Terms
First inspection
After about 500 operating hours
½ year at the latest
Control of air circulation and
surface of motor
Depending on local environmental pollution
Relubrication (as option)
See name plate or relubrication sign
Main inspection
After about 8,000 operating hours
Once a year
Remove condensate water
Depending on the local environmental
conditions
First Inspection
An initial inspection of the motor must be organized
after approximately 500 hours of operation, but not later
Measure
During
operation
At
standstill
Check of the electric characteristics
X
Check of the running noises. When the motor is running, it is checked if the quiet running
has changed for the worse.
X
Check of the bearing temperatures. It is examined if the permissible bearing temperatures
will not be exceeded during operation of the motor.
X
Check the intakes of the cooling air. There must be no damages.
X
X
Check of the foundations. There must be no cracks or other damages like depressions.
X
X
Check of the fastening bolts. All bolts used for fixing mechanical and electrical connections
must be tight with the required torque.
X
than half a year after start of operation. The following
examinations will be done at the motor: