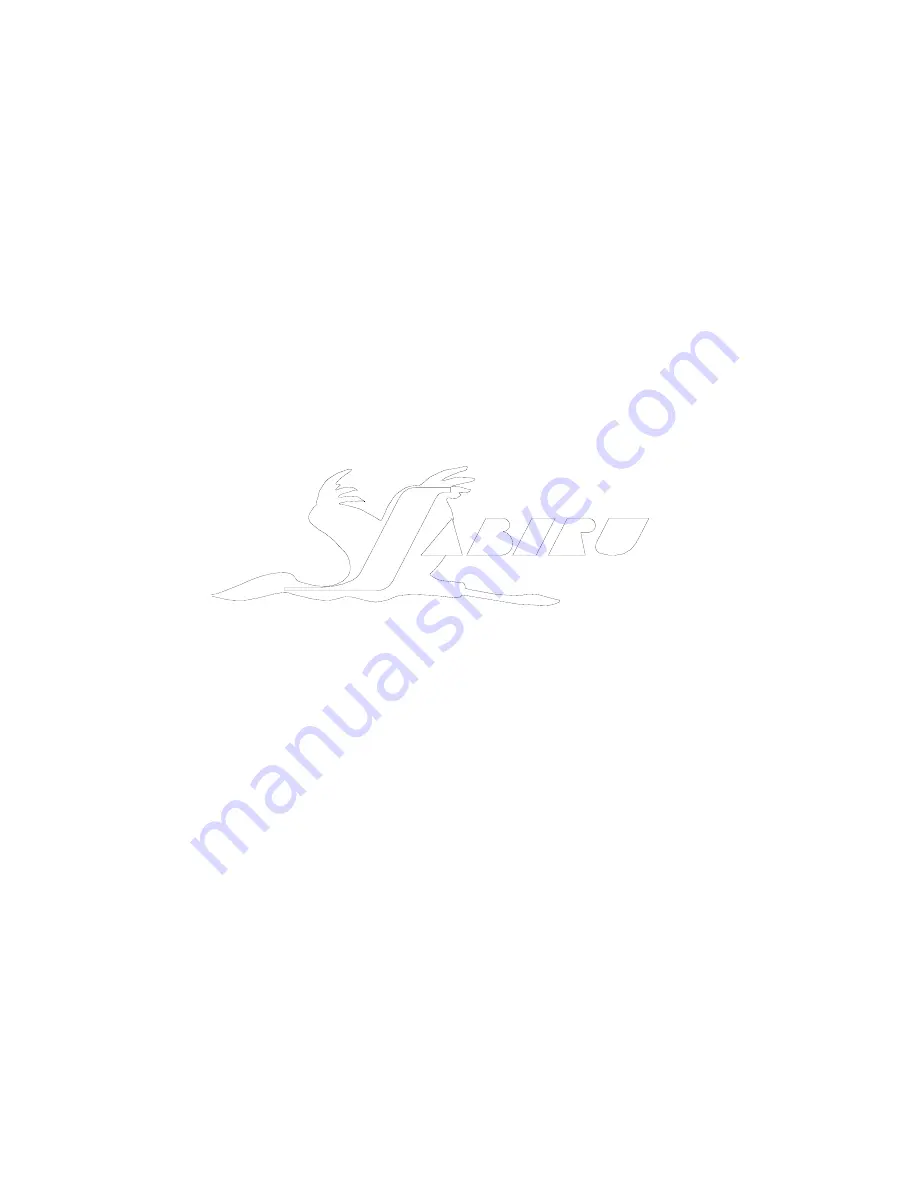
Page No: 1
Issue No: 1
Date: 031100
Issued By: PJA
INSTRUCTION AND MAINTENANCE MANUAL
FOR
JABIRU 3300 AIRCRAFT ENGINE
This Manual has been prepared as a guide to correctly operate, maintain and
service the Jabiru 3300 engine.
Should you have any questions or doubts about the contents of this manual, please contact
Jabiru Aircraft Pty Ltd.
Summary of Contents for 3300
Page 4: ...Page No 4 Issue No 1 Date 031100 Issued By PJA List of Amendments Page Amendment Date Issue...
Page 8: ...Page No 8 Issue No 1 Date 031100 Issued By PJA 1 1 Denomination of Cylinders...
Page 11: ...Page No 11 Issue No 1 Date 031100 Issued By PJA 3 0 PERFORMANCE GRAPHS...
Page 48: ...Page No 48 Issue No 1 Date 031100 Issued By PJA...
Page 52: ...Page No 52 Issue No 1 Date 031100 Issued By PJA...
Page 67: ...Page No 67 Issue No 1 Date 031100 Issued By PJA Drawing 9430064...
Page 89: ...Page No 89 Issue No 2 Date 031100 Issued By PJA...