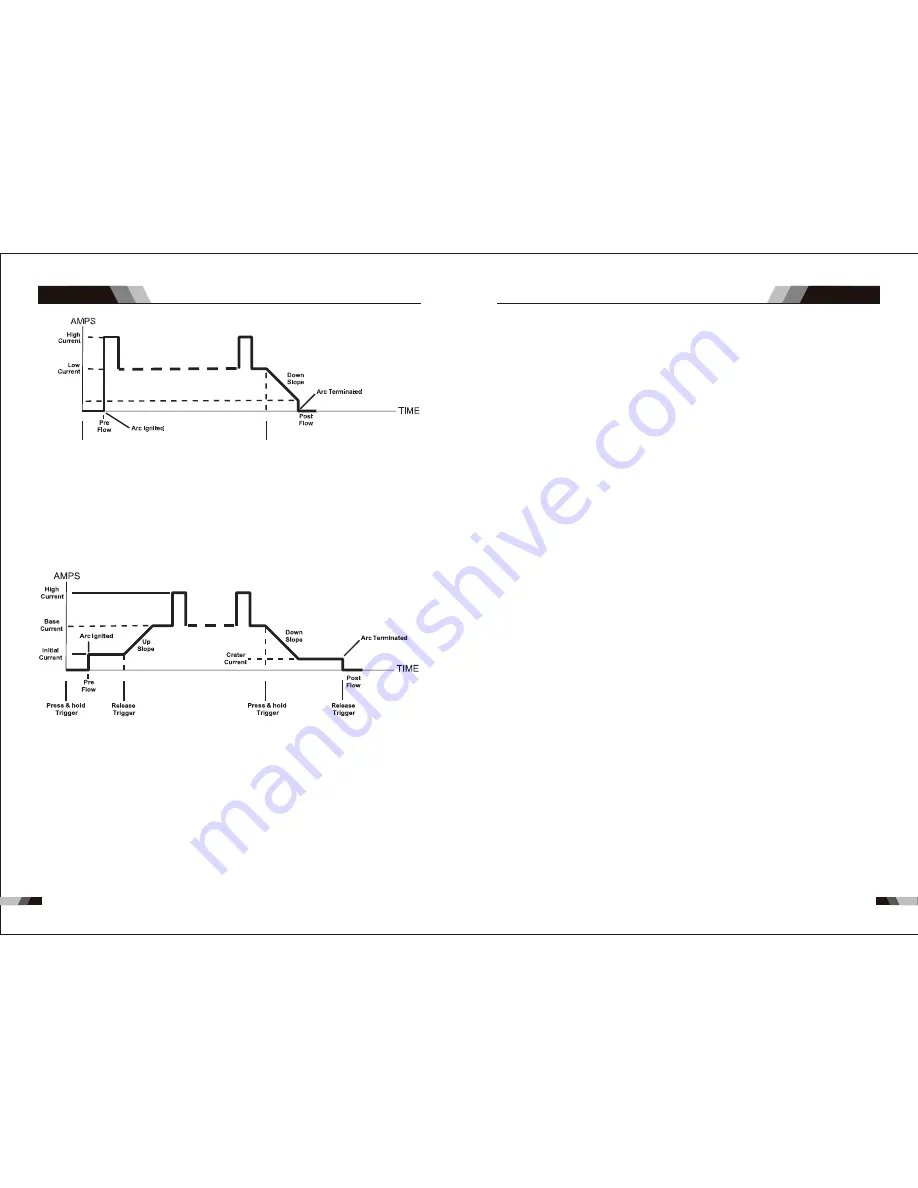
96
97
Operation
Operation
MULTIFUNCTION
SERIES
EQUIPMENT
MULTIFUNCTION
SERIES
EQUIPMENT
4. Process Selection Button
The process selection control is used to select the desired welding mode. Three
modes are available, GTAW (TIG), MMA (Stick) and CUT modes.
Note: that when operating in GTAW (HF and LIFT TIG modes), the power source will
remain activated until the selected down slope time has elapsed
Minimum
Current
Press & hold
Trigger
Release
Trigger
current of the power source.
At times of non-welding, the amperage meter will display a pre-set (preview) amperage
value. This value can be adjusted by varying the multifunction control when the
Programming Parameter Indicator light shows BASE CURRENT.
5. Digital Ammeter
The digital amperage meter is used to display both the pre-set current and actual output
4T Latch mode this mode of welding is mainly used for long welding runs to reduce
operator fatigue. In this mode the operator can press and release the torch trigger and
the output will remain active. To deactivate the power source, the trigger switch must
again be pressed and released, thus eliminating the need for the operator to hold the
torch trigger.
6. Digital Voltmeter / Parameter Meter
The digital volt meter is used to display the actual output voltage of the power source. It is
also used to display Parameters in Programming Mode.
Depending on the Programming Parameter selected, the status indictor adjacent to the
volt meter will illuminate to show the units of the programming parameter.
When welding, the volt meter will display actual welding voltage.
7. Power ON Indicator
The POWER ON indicator illuminates when the ON/OFF switch is in the ON position and
the correct mains voltage is present.
8. Thermal Overload Indicator Light
This welding power source is protected by a self resetting thermostat. The indicator will
illuminate if the duty cycle of the power source has been exceeded. Should the thermal
overload indicator illuminate the output of the power source will be disabled. Once the
power source cools down this light will go OFF and the over temperature condition will
automatically reset. Note that the mains power switch should remain in the on position
such that the fan continues to operate thus allowing the unit to cool sufficiently. Do not
switch the unit off should a thermal overload condition be present.
9. JOB and SAVE
You can press JOB to select the memory records that you have saved before from 1-9.
For the new setting of present base current Amps ,just press SAVE.
10. Programming Parameter Indicators
These indicator lights will illuminate when programming.
12. Mode Button
Press the MODE button to toggle AC and DC output in LIFT TIG, HF TIG and STICK.
13. Forward Programming Button
Pressing this button will advance to the next step in the programming sequence.
14. Back Programming Button
Pressing this button will go back to the previous step in the programming sequence.
15. Positive Control
16. Negative Control
17. Positive Welding Terminal
Positive Welding Terminal. Welding current flows from the Power Source via heavy
duty bayonet type terminals. It is essential, however, that the male plug is inserted
and turned securely to achieve a sound electrical connection.
11. HF Button
Press and hold the HF button to purge the gas line in LIFT TIG and HF TIG modes. To HF
the shielding gas line in LIFT TIG and HF TIG modes press the HF button and release.
18. 5 Pin Control Socket
The 5 pin receptacle is used to connect a trigger switch or remote control to the welding
Power Source circuitry:
To make connections, align keyway, insert plug, and rotate threaded collar fully clockwise.
The positive control is used to plus setting parameter for selected function from 10.
The negative control is used to minus setting parameter for selected function from 10.