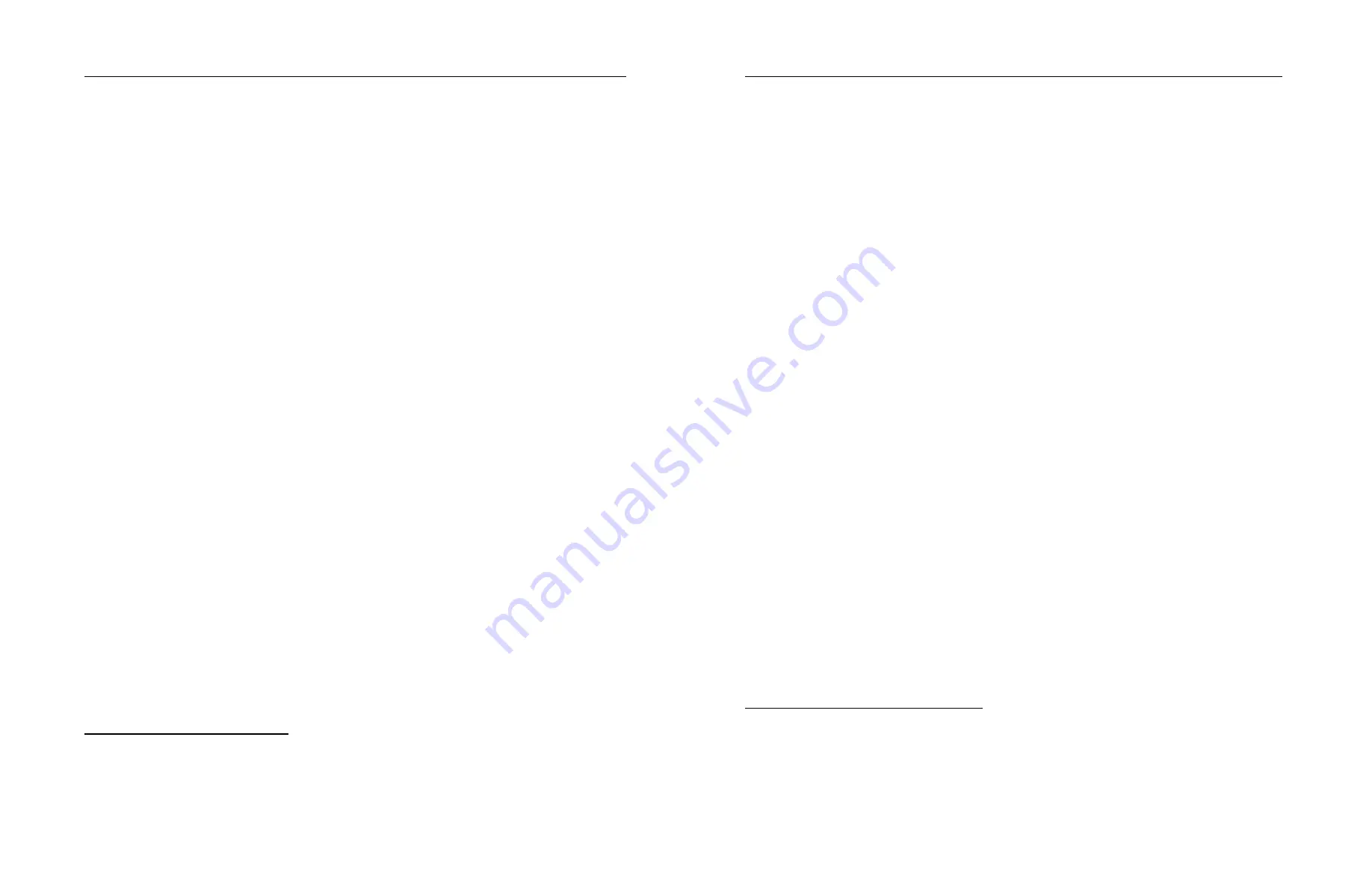
SECTION 7
RV-8/8A
7-7
8s7-1r11 06/13/11
construction with adequate ventilation. Use a respirator, gloves (which also keep oil from your skin off the surfaces
to be sealed) and protective cream when sealing the tanks. Why expose your skin and lungs if you can prevent it?
Roughen all mating surfaces using a scotchbrite pad. Don't be bashful; score the aluminum well, so the sealing
compound will have more surface to grip.
Clean the manufacturing residues and oils off all the rivets by sloshing them in a jar of solvent and drying them on a
clean rag. Clean the mating surfaces of the skin, stiffeners and ribs. Clean every surface that the sealer is applied.
Recommended cleaners include naphtha or MEK. Builders have also reported excellent results with etching using a
light phosphoric acid (brand names include AlumaPrep or Twin Etch).
It is essential that the surface of the aluminum be clean when the sealer is applied. Not just kind-of-clean or clean
enough. Clean.
After cleaning, do not pollute the areas to be sealed. Don't even touch them. Oils from your skin will affect the bond
of the sealant.
The tank sealant should be mixed as accurately as possible. This is done by weight. Follow the instructions
supplied with the sealant. When mixing sealant, do not mix too much at one time. A batch the size of four or five
golf balls is usually enough for one work session. The sealant provides 45 to 90 minutes of working time (less in
warmer temperatures). Measure by volume or weight as accurately as possible and mix thoroughly before applying.
To use the sealant as soon a possible, have all the work well planned and tools all laid out. Have a container of
acetone, MEK, or lacquer thinner nearby for the frequent tool cleanings necessary during riveting. You can peel
away overflow on areas you want to keep clean by strategically applying plastic tape before spreading the sealant
(such as along any areas of the skin that have to mate flush with the wing spar or W-423 splice plate).
After thoroughly mixing the sealant, use Popsicle sticks to apply an approximately 1/16" thick layer to the parts being
riveted. In the first work session rivet on the T-711 stiffeners. Back-riveting works well here, so spread a thin layer
of sealant on the inside of the skin, covering the area the stiffener will contact, then insert the rivets into the skin from
the outside and tape them in. Press the stiffener into place. Sealant will ooze out around all the stiffener edges.
When the stiffener is firmly seated, back rivet it permanently into place. Even more sealant will squeeze out as the
rivets set. Clean this away, making neat fillets around all the edges of the stiffener with the curved end of the
Popsicle stick. Dab a bit of sealant over every rivet head.
Rivet the VA-112 drain flange, T-406B fuel cap flange and T-714 clip to the skin, using sealant in the same way.
Cover the aft tooling holes in the outboard T-703 end ribs by riveting on a small plate, or by filling the hole with an
AN470AD6 rivet. (See Figs. 7-8, 7-11.) After each session clean everything that you do not want to have a
permanent coat of sealant. It is much easier to clean up before the sealant sets.
For the next session, rivet all the interior ribs to the skin (if you can only do a few ribs at a time, that's fine.) Work in
the “cradle." When assembling the tank, cleco all ribs to the skin. This keeps the assembly straight. You may want
to start riveting with the rib next to the outboard one. After this rib is clecoed in place with sealant you can remove
the outer end rib for easy riveting access. Remove the ribs one at a time, apply sealant, and rivet. When riveting
the ribs to the skin work from the leading edge to the trailing edge.
Insert the rivets and set them with a squeezer or a rivet gun, as appropriate. Use the Popsicle sticks to form the
squeezed-out sealant into fillets in the rib/skin joint. Apply extra sealant to the rivet heads.
Next, install the inboard end rib. After the rivets joining this rib to the skin are squeezed, install the T-405 and the T-
410 (fitted to the inside contour of the skin as shown on DWG 16A) on the leading edge. Put a thin layer of sealant
on the sealing surfaces. (If T-405 were installed on the rib before riveting the rib to the skin, the skin rivets around
the leading edge would be very difficult to set.)
Seal and rivet the other T-410 to the outboard end rib. Three or four AN470 rivets is sufficient.
Apply a generous fillet of sealant around the inside of the end ribs where they join the skin, particularly at the very
leading edge. Also make sure the outboard end rib aft tooling hole has been sealed. Finally, clean any excess
sealant from the rear of the ribs and skin where the baffle will later rest and clean any sealant smeared on the outer
surfaces. Once cured, it is difficult to remove.
CLOSING AND FINISHING THE TANK
If you are using a float type fuel sender, adjust and check it before closing the tank. Dimensions for the float arm of
the IE F-385 B/C sender in VAN'S ACCESSORIES CATALOG are shown on DWG 16A. Make an electrical check
with a 12-volt battery and a fuel gauge, or a multimeter should show about 32 ohms when the sender is in the "full"
position and about 240 ohms in the “empty” position.
RV-8/8A
SECTION 7
7-8
8s7-1r11 06/13/11
Install the fuel pick-up tube and position it so it lies on the bottom of the tank.
Check all final details before installing the baffle and closing the tank. Check that the tank vent line is in, and its
outlet is at the tank high-point. Check the vent line bulkhead fitting to see that it is tight and that it has been
installed with sealant.
Assured that everything is in order, apply sealant to the tank skin from the rivet holes forward. Upon installation the
baffle acts as a squeegee and the bead of sealant will be pushed ahead as the baffle is moved forward. Use a
maximum of 3/16' bead of sealant. Too much, and the thickness can start to build up, making the tank difficult to
install on the wing. Put a bead of sealant along the inside edge of the flange on each end rib. Put a heavy glob of
sealant where each corner of the baffle will meet the end ribs (this is one of the most common locations for leaks).
Put a very thin smear of sealant around each of the rivet holes on the back flanges of the T-703/4 ribs.
With the tank sitting in the cradle, install the T-702 rear baffle assembly by dropping it straight down onto the rear
flanges of the ribs.
Put a cleco in every hole of the T-701 skin to T-702 baffle joint. After clecoing, inspect the skin to see if it is pillowed
out between the clecoes. The contact surface of the tank baffle flange may require pressure to force out excess
sealant. The easiest method is to apply a c-clamp or strong spring clamp between each set of rivets and squeeze
out the excess. If you are unsure, clamp the flange in a couple of spots and see if it makes a difference.
Twirl the AD-41 H closed end blind rivets in sealant and set them in the top and bottom baffle-to-rear rib-flange
holes. The T-712 brackets are installed last. Check to be sure the platenuts have been installed on them because
it is much more difficult to do once they are riveted to the tank. Put a very light smear of sealant over each hole for
mounting the T-712 brackets. While double-checking with DWGs 16A and 10A, cleco each T-712 bracket in place.
Be sure you get them oriented correctly because they will shortly be very difficult to change. Install the AD-42H
blind rivets in the T-712 brackets after twirling them in sealant. This may require modifying a blind rivet tool by
grinding enough of the puller “nozzle” away to get into the corner of the Z angle.
Finish all riveting and clean any excess sealant off the tank.
To mount the T-708 cover plate use an 1/8” inch thick bead of fuel tank sealant between the cover plate and the
inboard rib. Dab a small blob of sealant on threads of each attach screw, insert into the holes, and tighten them
sequentially until sealant bulges evenly about 1/32” from underneath the perimeter of the sender plate. Some
builders may optionally seal the T-407 gasket to the tank with sealant as well, viewing the cork ring as sacrificial if
the cover is removed. The sealant will also form a small gasket around each screw head.
Install the IE F-385 Sending Units with sealant using the appropriate hardware. DO NOT install the rubber gasket
supplied by the manufacturer. Use the same procedure for sealing the sending unit as was accomplished above.
A continuous electrical path is necessary between the airframe and the sender plate so be sure that at least one of
the screw heads is making metal to metal contact with the outside of the sender plate. Conduct a final electrical
continuity test for the sender units with an Ohm Meter by probing the tank body and the sender center screw to
ensure proper operation.
Wait at least 24-48 hours and then conduct a fuel tank leak check using the FUEL TANK TEST KIT available in the
VAN'S ACCESSORIES CATALOG.
RIVETING THE WING SKINS
There is a definite order in installing the wing skins. First, the leading edge (built off the wing) is installed. Then the
top main skins are installed. The wing is then rigid enough to remove from the stand and install the ailerons, flaps
and work on the internal details. After that is complete, the wing is laid, top down, on a large table and the bottom
skins are riveted.
WING SKIN PREPARATION AND ASSEMBLY
Remove the skins, deburr and dimple them. Complete OP46-02 Steps 5-6 deburring and dimpling (complete
riveting when riveting the skins).
Prepare the skeleton while it is still fastened to the stand. Drill a 7/16" hole in the left W-701 leading edge skin and
the left main spar flange for the pitot tube fitting (see DWG 15A.)