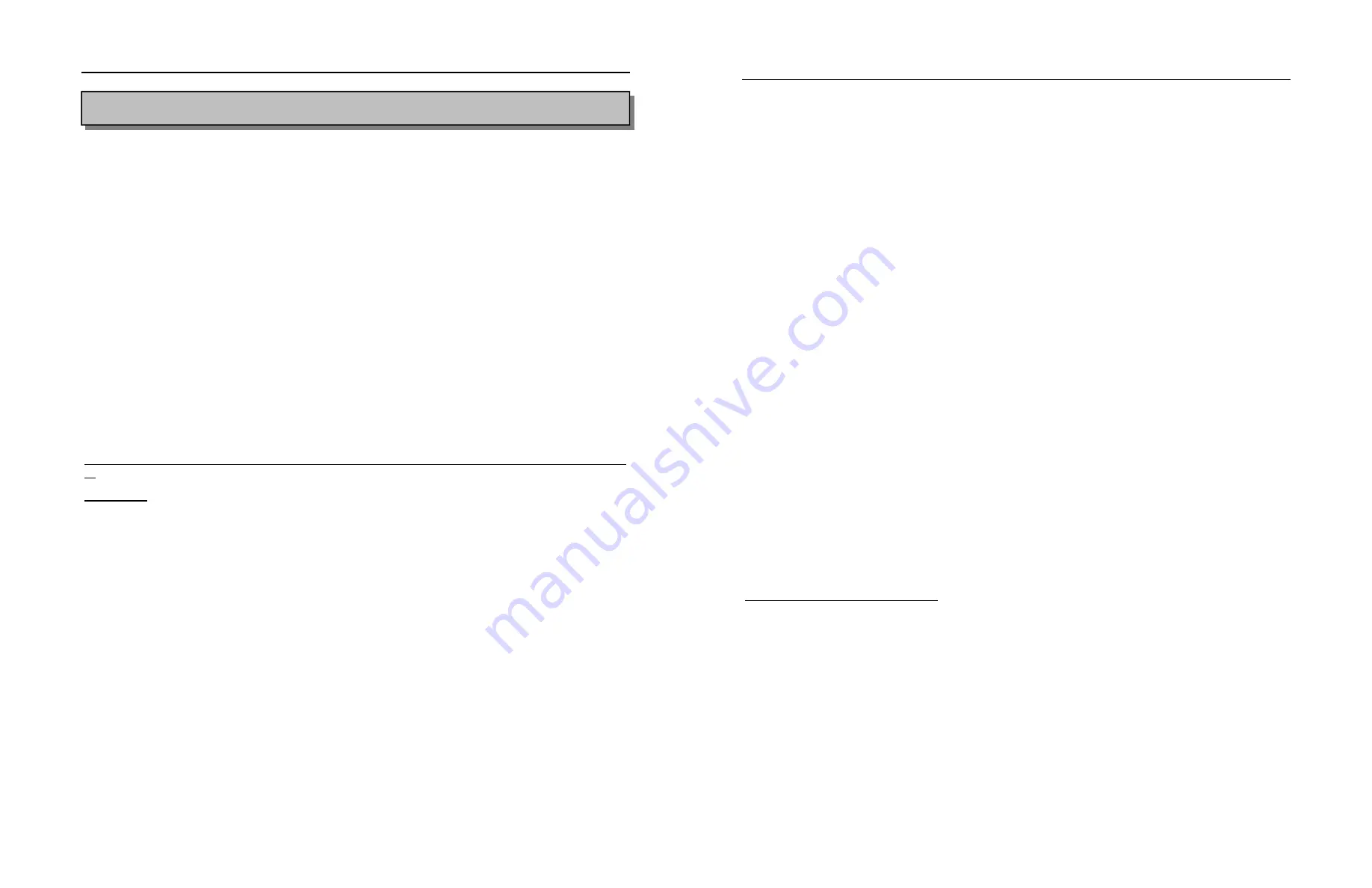
SECTION 8
THE FUSELAGE
RV-8/8A
8-1
8s8PP-1 r1 06/23/11
The RV-8/8A fuselage is a semi-monocoque or stressed-skin structure. The strength of a monocoque fuselage is
very similar to nature’s most perfect monocoque structure, the egg. Like the egg, the fuselage can withstand
tremendous loads when properly applied, but is subject to localized failure when subjected to concentrated loads.
The shape of the skin is determined and maintained by internal frames, bulkheads, longeron angles and skin
stiffener strips. The longerons and bulkheads also provide localized strength for the attachment of wings,
empennage, controls, canopy, etc.
All the ribs, bulkheads, and skins are prepunched at Van’s factory. No jigs or alignment fixtures are required.
When the holes align, the fuselage must be straight. The only required assembly fixtures are a sturdy, level table to
assemble the bulkheads and other subassemblies, and two, sturdy saw horses to support the fuselage while
riveting. Once the skins are riveted in place, the fuselage becomes very rigid and self-supporting.
The final fuselage assembly process will require approximately 350 3/32-inch (silver) clecos and 125 1/8 (copper)
clecos.
NOTE: This section contains instructions for both the RV-8 and RV-8A. For areas of major difference
between the RV-8 and RV-8A an entire subsection will be designated “This section RV-8 (or 8A) Only:”. In
areas with minor differences, single steps will be designated “RV-8 Only:” or “RV-8A Only:”. Any text
without a designation pertains to both models. Steps or Subsections with an “only” statement should only
be used if it corresponds to the model you are building.
For ease of tooling and forming, larger RV-8/8A bulkheads and fuselage ribs are formed in two or more pieces and
then riveted together to form the complete part. Before assembly, round and smooth all edges and corners of the
parts. The fuselage bulkheads are straightened using flutes similar to those on the wing and empennage ribs, by
fluting between the pre punched rivet holes as needed to make the part flat and straight. The one exception is the
firewall. Its flanges must not be fluted, to provide a flat surface for mounting the cowling attach hinges. Some
fuselage parts are made of 2024-T4 bar stock or 6061-T6 extruded angle, neither of which are alclad, and must be
primed before assembly. Priming the parts made from alclad aluminum sheet stock is optional. If you desire good
paint adhesion to the powder coated parts, remove the gloss with a Scotch-bright™ pad or fine sandpaper.
IF BUILDING WITH AN RV-8 OR 8A QUICKBUILD FUSELAGE KIT, BEGIN CONSTRUCTION ON PAGE
42
FIREWALL
CAUTION: Stainless steel parts are very sharp, handle the Firewall with care
!
NOTE: Stainless steel will quickly dull cutting tools (drills, Deburring tools, and Unibits™). Use plenty of
lubricant (Van’s Aircraft sells and uses Boelube™), and keep the cutting speed low. Use a Unibit or hole
saw (place a piece of wood on the back side of the firewall) to make any holes over 1/4 inch diameter.
Remove the tab from the F-801E-L-1 & -R-1 Side Angles, and both sides of the F-801C-1 Upper Angle (See
“Exploded View Aft”, DWG 60). Break apart the four gussets and the four spacers that are joined together on F-
801JKWY. File or sand off the excess flashing from each of the eight parts. Deburr the edges of the stainless
steel and aluminum firewall parts shown on DWG 60.
Cleco the F-801C-1 Upper Angle, F-801D-1 Lower Angle, F-801E-L-1 & -R-1 Side Angles, F-801F-1 Middle
Angle, and the F-801H-R-1 & -L-1 Center Angles to the aft side of the F-801A-1 Firewall.
Cleco the two F-801J-1 Spacers, and the WD-802-L-1 & -R-1 Engine Mount Brackets to the two upper corners
of the firewall. Cleco the two F-801K-1 Spacers, and the WD-803-L-1 & -R-1 Lower Engine Mount Brackets to
the two lower corners of the firewall.
Cleco the two W-801W Gussets, and the two W-801Y Gussets in place on the aft side of the firewall.
Cleco the two F-801L Backing Plates in place on the fwd side of the firewall (See “Exploded Iso View Fwd”,
DWG 60). Be sure the backing plates are positioned with the large hole nearer to the bottom of the firewall.
CAUTION: In this step, do not match-drill the 13 holes at each end of the F-801C-1 common to
each of the WD-
802-L-1 & -R-1 engine mount brackets. These holes will be drilled later in construction when the
fuselage longerons are in place.
SECTION : 8 THE FUSELAGE
RV-8/8A
SECTION 8
THE FUSELAGE
8-2
8s8PP-1 r1 06/23/11
From the front side of the firewall, final-drill #30 all of the 1/8 holes. Final-Drill #40, the 3/32 holes used for
installing the six nutplates that rivet on through the firewall. The 1/4 hole in each backing plate should be
match-drilled through the firewall if In-flight Adjustable Rudder Pedals are being used. Do not drill if using
ground adjustable rudder pedals.
Uncleco all parts. Final-Drill the 3/32 nutplate attachment holes in the flanges of the F-801F-1 Middle Angle,
and F-801H-R-1 Center Angle.
Put an 8-degree fwd bend in the top portion of the firewall. Place the firewall, flange side up, on a worktable
with the bend line aligned with the edge of the table. The bend line is centered on the flange notch at each end
per the dimensions in the “Exploded Iso View Fwd”, on DWG 60. Clamp a sharp cornered board (cut to fit
inside the firewall flanges) along the bend line, and bend the firewall per “View A-A”, DWG 60.
Deburr all rivet holes in the stainless steel firewall.
Dimple countersink all the #30 rivet holes in the web of the stainless steel firewall for flush heads on the fwd
side, except the four holes used to attach the two F-801L Backing Plates.
CAUTION: In the following step do not dimple countersink the four holes that attach the two nutplates
at the bottom of the firewall.
Dimple countersink the #40 holes in the stainless steel firewall that attach nutplates through the F-801F-1
Middle Angle, and the F-801C-1 Upper Angle
.
Machine-countersink the holes in all the aluminum Firewall Assembly parts that match with dimpled holes in the
F-801A-1 Firewall.
Machine countersink the #30 rivet attach holes on each F-801L Backing Plate for a flush head on the fwd side
(See “Plan View”, DWG 60).
Machine countersink the #40 nutplate attachment holes on the F-801F-1 Middle Angle, and the F-801H-R-1
Center Angle for flush rivets (See “Exploded Iso View Aft”, DWG 60). Countersink the side opposite the
nutplate location.
Machine countersink the four nutplate attachment rivet holes on the
aft
side of the F-801D-1 Lower Angle for
flush rivets (See “Plan View”, DWG 60).
Deburr all rivet holes in all the Firewall Assembly parts.
Prime the aluminum parts if/as desired.
Rivet the four nutplates to the F-801H-R-1 Center Angle and the six nutplates to the top flange of the F801F-1
Middle Angle.
Re cleco all Firewall Assembly parts to the F-801A-1 Firewall (See “Exploded Iso View Aft”, DWG 60). Rivet all
parts to the firewall. Back riveting works well for most of the rivets if you space a plate off of the worktable to
allow for the firewall flange.
RV-8A Only:
– Install rivets in the two rivet holes at each end of the row designated “leave open”, near the
bottom of the firewall in the “Plan View”, DWG 60.
RV-8 FORWARD FUSELAGE FLOOR
(This section RV-8 Only)
Final-Drill #40, the 3/32 nutplate attachment holes on the F-802K-1 L. G. Fwd Crossmember, and the F-802L-1
L. G. Aft Crossmember lower flanges (DWG 61). Machine countersink #40, the nutplate attach rivet holes
drilled in this step for flush rivets.
Cleco the F-802K-1 L. G. Fwd Crossmember, F-802L-1 L. G. Aft Crossmember, F-836-L-1 & -R-1 Floor Ribs,
and the F-802M-L-1 & -R-1 Intercostal Ribs to the F-822-1 Fwd Floor Panel (DWG 61). Temporarily label the
skins bottom and top sides.
Final-Drill #30, all 1/8 holes common between the F-822-1 Fwd Floor Panel and all clecoed parts. Final-Drill #30, all 1/8
holes common between the F-802K-1 L. G. Fwd Crossmember, the F-802L-1 L. G. Aft Crossmember, the F-802M-L-1 & -
R-1 Intercostal Ribs, and the F-836-L-1 & -R-1 Floor Ribs.
(Parts can be removed temporarily to improve access).
Final-Drill #30, the 1/8 holes (with no parts clecoed to them) on the fwd portion of the F-822-1 Fwd Floor Panel,
that are designated for dimple countersinking on the Dimpling the Fwd Floor Panel diagram (DWG 61).
Final-Drill #40, all the nutplate attachment holes in the fwd floor panel.