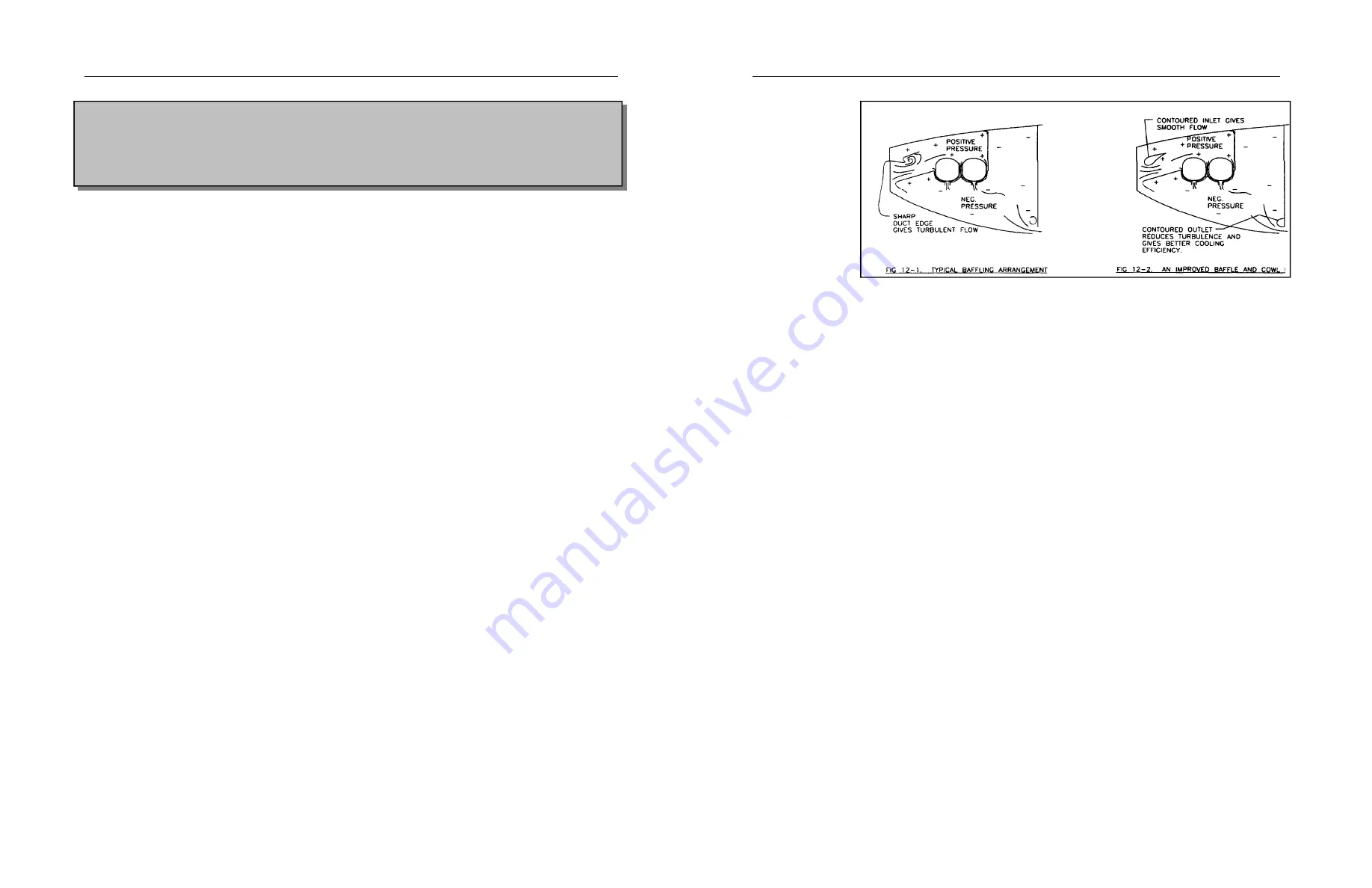
SECTION 12:
FITTING THE COWL, SPINNER & COOLING BAFFLES
12-1
12 11/29/12
We believe the RV cowls to be an attractive and efficient design. Its smooth contours streamline the engine for low
drag, and, in addition, it has been designed internally to reduce engine cooling drag; something often overlooked in
homebuilts. It is light and mounts with no external fasteners to cause drag or detract from appearance. The cowls
are designed to fit nearly all versions of the Lycoming O-320 and 0-360 engines and 200 HP I0-360 engines with
forward injectors. Either fixed-pitch and Hartzell Compact Hub model constant-speed propellers may be installed.
The cowl is supplied in five separate fiberglass pieces; the top half, lower half, a pair of upper inlet ducts, and an oil
filler door. The lower cowl half includes an air intake scoop appropriate to the engine. Installing the cowl requires
attaching the two cowl halves to each other and to the firewall. The inlet duct moldings must be bonded in place
and an oil access door cut out and mounted. These points and more will be covered later, but first, let's review
some engine cooling theory so that we can better understand why these installation procedures need to be
followed.
All engines recommended for use in the RVs were designed for pressure cooling. The pressure is supplied by the
velocity of the aircraft moving through the air, but it is probably easier to understand if we assume the engine to be
stationary and the air is moving past it. In Fig. 12-1 we try to show just what pressure cooling consists of. It is
much more involved than just letting “wind'' in through a hole in the front of the cowl to “blow'' on the engine. As the
drawing shows, the incoming air, because of the forward velocity of the aircraft, forms a high pressure parcel of air
on the upstream or “cold air plenum'' side of the engine. A properly designed air outlet tends to act as a vacuum
pump and cause the air in the downstream or “warm air plenum'' area to have a lower air pressure than that
upstream. It is this pressure differential which causes the air to flow past the cooling fins of the engine and carry
away the excess heat. Cooling baffles are required on the engine to direct the air past the cylinder cooling fins, and
to serve as a barrier between the “intake'' and “outlet'' air plenum chambers. The air inlet and outlet openings
should be carefully designed and constructed to maximize the pressure differential between the two portions of the
cooling system.
Aircraft engines are designed to require a certain volume of air per minute to operate within temperature limits. This
is about 2500 cubic feet of air per minute for the O-320 and O-360 engines. From this we have determined the area
required for the inlets to provide this volume of air at a full throttle climb speed of 90-100 mph; the flight mode which
will impose the greatest cooling requirements. Then for higher speeds and/or lower power settings, cooling will be
assured.
There are three basic components we must consider in designing an efficient cooling system: inlet, baffling, and
outlet. In the inlet we seek to pass air into the engine compartment with the minimum pressure loss and the
minimum internal and external drag. With the baffles we attempt to direct the air over the cooling fins of the
cylinders as evenly as possible and with a minimum of “waste” or loss through holes, gaps, or other unnecessary
openings. The outlet is designed to cause the heated air to exit at a speed as near to slipstream velocity as is
possible.
Fig. 12-1 shows that the area of the inlets is much less than the cross section area of the cold air plenum inside the
cowl. This means that the air must decelerate as it enters the engine compartment. As it slows down, its energy of
motion is converted into pressure. The purpose of the contoured inlet ducts is to maintain a smooth flow during
deceleration and thus maximize the pressure recovery. According to theory, a sharp edge inlet would cause a
disturbed airflow resulting in energy being lost in conversion to heat rather than pressure. It is very important that
the engine baffle is properly designed and fitted so that the only openings for this air to escape are those past the
cylinder cooling fins. This means the area around the front of the engine must be baffled as well, to prevent air
escaping forward around the starter ring gear.
Fig. 12-1 shows a typical cowl and engine compartment. Fig. 12-2 shows the same cowl with improved contours on
the inlets and outlets which make a significant difference in engine cooling and cooling drag. These consist mainly
of inlet and outlet ducts with improved contours for smoother air flow. Also important, but not shown here, is a
portion of the baffle near the front of the engine which blocks the cooling air from flowing forward over the front
center of the engine and starter ring gear, and then out the bottom. This would be “wasted” air and cannot be
tolerated in an efficient cooling system.
The object of a pressure cowl baffle is to maximize the air pressure differential between incoming and outgoing air,
and to provide the tightest possible seal between these two air chambers. Air entering the cowl openings which
SECTION 12: FITTING THE COWL, SPINNER
& COOLING BAFFLES
SECTION 12:
FITTING THE COWL, SPINNER & COOLING BAFFLES
12-2
12 11/29/12
does not pass over the
cylinder cooling fins, or
serve some other
a c c es s o r y c o o l in g
function, is wasted.
“Wasted air” will cause
e i t h e r e n g i n e
overheating because
there is not enough air
remaining to provide
cooling, or the need for
larger inlets and outlets
t o p r o v i d e t h e
necessary cooling air
plus the wasted air.
This means more drag
and less speed. While
it is difficult to completely seal an engine baffle, the combined area of these “waste air” leaks should be held to not
over 1 or 2 square inches.
Further improvements of the baffle are possible. Since the fit of the aluminum baffle to the engine will not be air-
tight, high temp. RTV Silicone Rubber can be used to seal these small gaps. The fabric airseal material used as a
seal between the baffle and cowl, often “puckers” away from the aluminum and permits air to escape. This may be
sealed with RTV as well.
AIR FILTER SYSTEMS
The RVs are designed to accept Lycoming engines from 115-200 horsepower. These engines may be fitted with a
wide range of induction devices including carburetors, fuel injection systems by different manufacturers, throttle
body injectors like those made by Ellison, and more. Just to make it more complicated, these devices may be
mounted in a variety of places on the engine. The cowls supplied with kit for 115-180 hp engines have an induction
scoop molded onto the bottom. This scoop is designed to fit the “standard” carburetor location on the bottom of the
sump (as used on new engines ordered through Van’s.)
Filtered air induction systems for the various engines and induction devices are offered in Van’s Accessories
Catalog and used by a vast majority of RV builders. These systems improve induction efficiency, filter all the air
entering the engine and include provisions for alternate air or carb heat. Installation instructions are included.
The cowl supplied for the 200 hp IO-360 angle valve engine has no scoop. Instead, it is designed to work with the
Horizontal Induction filtered air induction system in Van’s Accessories Catalog. Air is inducted through a filter
mounted in the left “nostril” of the cowl and routed through a molded fiberglass duct to the forward-facing injection
servo on the sump. In this case the engine cooling baffles should be fitted before the induction system.
BEFORE FITTING THE COWL
The following instructions are meant to cover all RV models. Some may not apply to your particular RV.
Before attempting to install the cowl, the engine (without the exhaust system installed) must be mounted. Check to
see that the engine mount bolts are tight, the rubber mounts are properly seated, and anything else which might
effect engine positioning or alignment is resolved. Some builders run the engine for a few minutes to “shake”
everything into place. We
do not
recommend this: Engines are designed to run with baffles and cowls in place and
will not cool properly without them. We have also received reports that running the engine on partial airframes
(without wings, etc., installed) has caused vibration damage to the airframe itself.
If you have chosen a fixed pitch prop, install the propeller extension on the front of the crankshaft.
(NOTE: All RV
cowls are designed to use a 2 ¼” propeller extension or a constant-speed prop with an equivalent hub. See Section
11 and DWG C4).
Install the spinner or at least the spinner back plate to use as a reference for positioning the front
of the cowl. If you are installing a constant-speed propeller, it is best if the prop is installed, because, in this case,
the spinner back plate mounts to the prop. If the prop is not available, a spacer 2 1/4” thick, attached to the front of
the crankshaft (be sure the starter ring gear is installed!) may be used to simulate it.
INSTALLING THE HINGES
The RV cowls use piano hinges as attachment fasteners. This offers several advantages: evenly distributed loads
along the attachment line, smooth cowl lines with no external fasteners, and easy installation and removal.