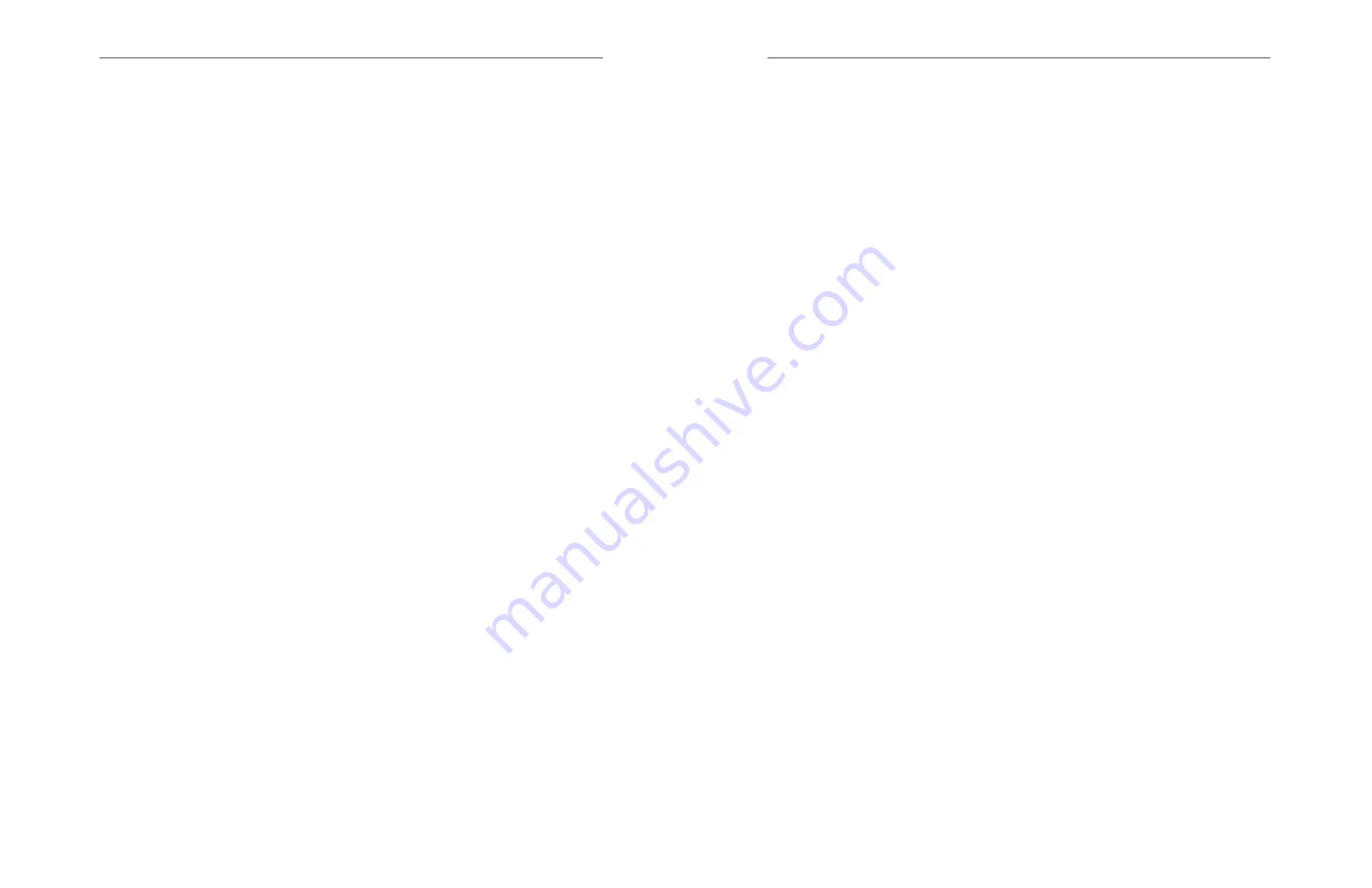
RV-8/8A
SECTION 9
FITTING THE CANOPY
9-3
8s9r3.pub 6/19/01
point, the “inside” person can gently raise the Wd-819 frame, sliding it upward along the shanks of the Wd-
844 roller mounts until it contacts the canopy. C-clamp (or adjust with shims) the frame to the roller mount
and mark its position. Should the WD-819 frame need to be lowered, remove material as required from the
bottoms of the canopy frame front bow tube. The next time the canopy is removed, double-check to be sure
the rollers are aligned and parallel to the tracks, then drill and bolt the frame to the roller mount.
Finish the edges of the canopy.
When the canopy fits the frame and the forward fuselage, clamp it to the frame with a multitude of spring
clamps and duct tape.
Carefully mark the separation line between the windshield and the sliding canopy. To help make a planar
cut, carefully mark and trim a piece of corrugated cardboard to match the outside diameter of the WD-814
windscreen support weldment. Sandwich the cardboard between the windscreen support and canopy
frame, push it up into contact with the inside of the canopy, and it shows exactly where to cut. Take a deep
breath and make the cut, running the cutting wheel directly into the cardboard template. This cut does not
have to be perfect; the fiberglass fairing will cover it, but the neater the cut is, the easier it is to do a good
job on the fairing. After separating the windscreen and canopy, smooth the cut edges and set the wind-
screen aside.
Clamp and/or tape the canopy back onto the frame and drill the canopy to the frame per the following se-
quence: Drill the through the canopy and into the frame using a regular #40 drill bit, cleco as you go. Re-
move the canopy and enlarge the holes to final size using a #27 Plexiglas drill bit. Back-up each hole with a
block of wood to prevent “break through” cracking as the bit finishes the hole. Enlarge the holes in the can-
opy frame to #30. De-burr holes and cleco the canopy to the frame.
Rivet the canopy to the frame with temporary AACQ rivets every 10-12”. These will be drilled out later, but
for now the canopy must be held in place so the skirts can be fitted accurately.
FITTING THE CANOPY SKIRT
The sequence we used for fitting the skirt to the canopy and frame is quite a bit different from the way
things have been done until now. First the frame is drilled and then the canopy skirt is set on top and the
holes underneath are located with a hole duplicator and templates. Then the builder drills through the can-
opy skirt and into the existing hole in the canopy or canopy frame. I know it sounds goofy but our prototype
builders swear it is the best way to prevent the drill from running off the side of a tube because it wasn't
centered. One of our prototype canopy skirts has several "worm tracks" where the side of the drill tore into
the skirt as the tip of the drill ran off the side of the tube. Along the bottom of the canopy, at each hole draw
two lines up the side, intersecting on the hole. Make the lines long enough to leave 4 to 5 inches visible with
the canopy skirt in place. When the skirt is in place, continue the lines down onto the skirt and drill at the
intersection.
Along the bottom of the canopy skirt, pre-drill #40 holes into the center of the canopy frame lower tube. Af-
ter fitting the canopy skirt use a hole duplicator to drill matching holes. See DWG 46 for the hole finding
tool.
For the canopy frame ribs, pre-drill #40 holes into the centers of the ribs, then for each rib, make a hole pat-
tern transfer template out of scrap aluminum. The transfer template should also pick-up two or three holes
on the canopy frame lower tube adjacent to each canopy frame rib. After fitting the canopy skirt cleco the
template in place over the canopy skirt using the existing canopy frame lower tube holes and drill.
Before fitting, block the canopy 1/8 inch open. Use a scrap piece of 0.125 material between C-806 and C-
661. Blocking the canopy open before fitting ensures a tight fit between skirt and fuselage when the canopy
is pulled fully closed.
Trim the canopy skirt to ¼ inch outside of the scribe line before fitting. Place the skirt over the canopy and
frame assembly and tape it in place. Make a notch in the aft end of the skirt to allow the skirt to fit over the
center canopy slide. The notch should be the minimum size required to clear the slide to minimize air leaks.
The aft 1/3 of the skirt should be nicely and evenly in contact with the aft fuselage skin. With the canopy
skirt now taped in its near final position, cut a hole in the left side of the skirt for the canopy latch handle to
pass through. Re-tape the skirt in place. Look at how the skirt fits the fuselage and consider trimming up to
the scribe line to improve the fit.
Drill and cleco the skirt to the frame, beginning at the rear and working forward pulling the skirt tight as you
go. Shim gaps between the skirt and canopy frame ribs to preserve the molded-in shape of the skirt rather
than letting the rivets pull little depressions in the skirt. The shims can be scraps of aluminum or they can be
local build-ups of fiberglass and epoxy. For initial fitting, scraps of aluminum will be easier and can be re-
placed later with fiberglass/epoxy.
NOTE:
The canopy skirt is made with epoxy resin, and only epoxies should be used when shimming or
filling. Polyester resin will not give satisfactory results over epoxy.
With the skirt drilled and clecoed to the frame, trim any excess material away from the edges of the skirt.
SECTION 9
FITTING THE CANOPY
RV-8/8A
9-4
8s9r3.pub 6/19/01
Carefully countersink the skirt for blind rivets. The rivets have 120 degree countersink heads, so if you have
a rare and expensive 120 degree countersink cutter this is the place to use it, otherwise a 100 degree coun-
tersink cutter is acceptable.
Drill-out the temporary fasteners that held the canopy to the frame, then rivet the canopy and skirt to the
canopy frame.
Because the C-802 canopy skirt is an epoxy/fiberglass part, those builders desiring an absolutely perfect fit
to the fuselage can add local build-ups of epoxy and fiberglass to fill any undesirable gaps between the
canopy skirt and fuselage. The extra material thickness can then be removed from the outside surface of
the skirt. Rivet heads may also be covered, if desired.
INSTALLING THE CANOPY LATCH
Install the C-654-1 canopy latch, WD-642 inside latch handle, C-655 spring, C-656 outside latch handle,
and C-667 bushing to the canopy frame using the hardware called-out on DWG 44, View Z-Z’ and the
“Latch Detail” view.
Slide the canopy all the way forward to the closed position to check for proper latch engagement.
The C-654-1 latch is designed to align with and engage the small diameter portion of the latch pin on the
WD-814 windscreen support weldment. C-654-1 may be slightly bent either inboard or outboard as required
to achieve proper latch to pin alignment.
Proper latch engagement should not exert very much forward pull on the canopy. Excessive forward pull
will do nothing more than distort the canopy and degrade the fit of the canopy to the fuselage. As previously
described, the forward travel of the canopy is limited by the engagement of the anchor pin and anchor
block; attempting to pull the canopy beyond this only causes distortion. It might be necessary to remove
material from the “elbow” of C-654-1 to achieve the correct amount of latch pull.
After you have your RV-8 finished and flying, you may want to recall this nuance of the canopy latching
function. Use the right combination of sliding speed and arm muscle to fully “seat” the canopy closed before
engaging the latch. Slowly sliding the canopy forward just enough to engage the latch and letting the latch
geometry pull the canopy the last bit of travel will probably not fully engage the anchor pin and block and
will pull the canopy into a distorted shape.
Attach the fixed windscreen portion of the canopy to the WD-814 windscreen support weldment using the
method and hardware shown on DWG 44, Section B-B’. Use the same drilling sequence here as was used
when attaching the canopy to the frame. Some additional minor trimming of the lower outboard edges of the
windscreen may be necessary to achieve a good fit to the windscreen support weldment. Smooth the cut
edges before proceeding further.
INSTALLING WINDSHIELD MOLDING STRIP
The following directions were written by an expert RV builder, known for the beautiful finish around his
canopies: They were written during the installation of a sliding canopy, but the techniques work equally well
for the strip around the front of the tip-up.
If you choose to mold your own fairing, begin by cleaning the aluminum skin. Several builders have
reported markedly better adhesion after they etched the skin with a mild phosphoric acid, but don’t get any
of this on the windshield! The molding should continue around the base of the windscreen back to the
point where the windscreen is under the aluminum skin. At this point the fiberglass molding is to be faired
smoothly into the skin line.
Imagine (or draw on a sheet of paper) a cross section view of the fwd base of the windshield to the top deck
of the fuselage. It will be an inside radius. Cut out about a 4" diameter circle in poster board or similar and
hold on edge at the base of the windshield. Where the circle touches the windshield and the skin is about
where the fiberglass will end on each. Also notice that the space formed by the circle that you want to fill
with fiberglass is not the same thickness across the whole section. This is why you can't use cloth all one
width (unless you want to do more sanding than any metal airplane builder should have to do).
A couple of general tips -
The closer you get to your finished shape, and the more accurately you lay up the glass/resin, the less
finish work (read: sanding) will be involved.
Make sanding tools in the exact shape/radius for the areas you wish to sand. For example: All around the
forward base of the windshield, you will be sanding a varying inside radius. Find some type of round tube
(thick wall PVC pipe works very well) that you can glue different grits of sandpaper to that has the radius
you want the finished shape to be. I use about a 3-4” inch radius and glue sandpaper with spray contract
adhesive.
Before doing any glass layups you need to do some prep work.
First, figure out where the edges of your finished glass work will be on the plexi. Use your round circle