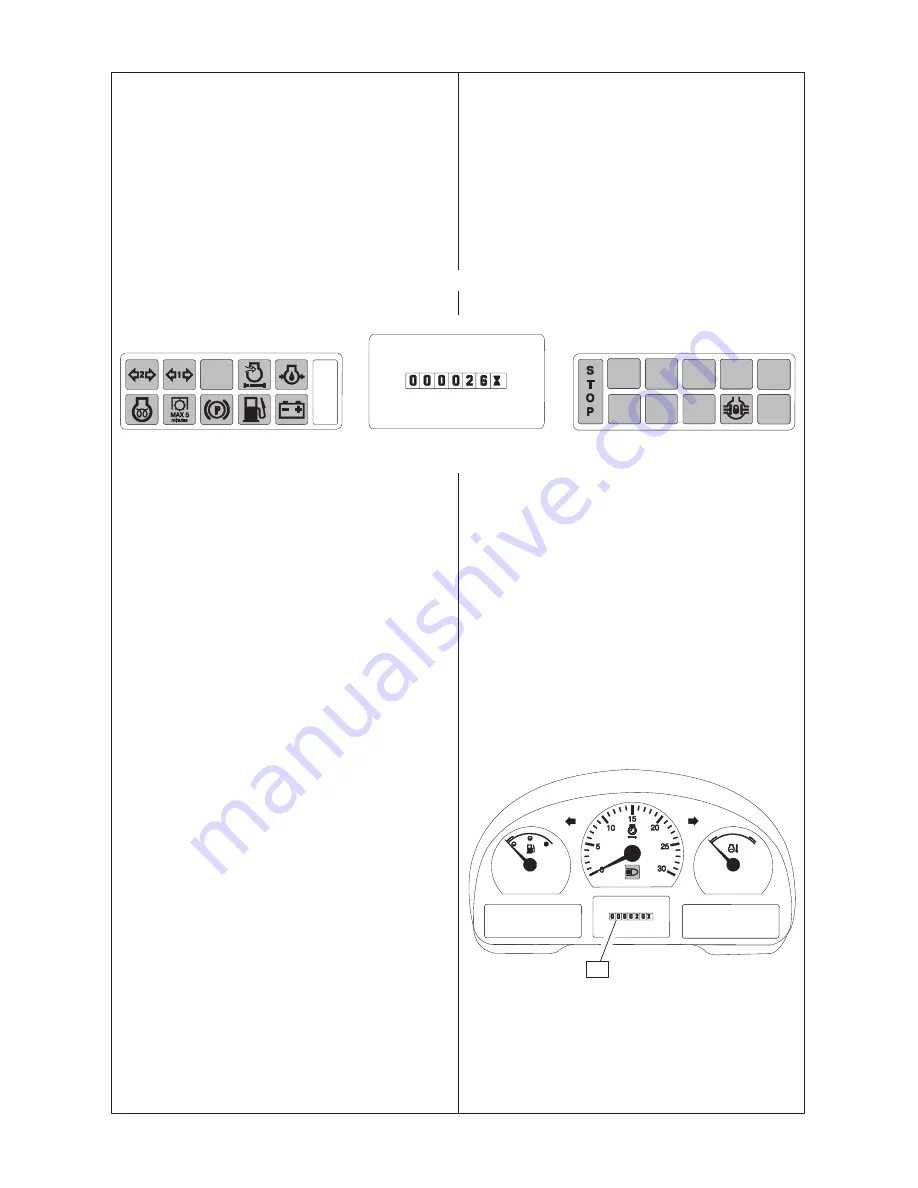
---31---
D. Instruments and controls
D 2.2.2.3.
Coolant thermometer (2
.3
)
The white zone
shows the limits for the
normal
operating
temperature.
Stop
the engine if the needle moves into the
red zone
.
D 2.2.2.4.
Indicator lights for direction indica-
tor (2
.4
)
There is an indicator light for the right and left direction
indicators.
D 2.2.2.5.
Indicator light for main beam (2
.5
)
This indicator light comes on, when the main beam is on.
D 2.2.2.6.
Indicator lights on instrument panel (2
.6
)
1
2
3
4
6
7
8
9
10
11
12
13
14
15
16
17
18
19
20
21
22
5
69--- 23
1 Direction indicator warning light for second trailer
(green, if one of the bulbs on the vehicle has failed, this
light will not come on)
2 Direction indicator warning light for first trailer (green, if
one of the bulbs on the vehicle has failed, this light will
not come on)
3 Not in use
4 Engine air cleaner warning light for blocked filter (yel-
low), filter must be serviced
5 Engine oil pressure (red) is too low
6 Not in use
7
Engine STOP
(red)
is flashing. The tractor and the
engine must be stopped immediately. Must only be
continued in an emergency, e.g. the tractor can be
moved to the roadside.
8 Not in use
9 Not in use
10 Not in use
11 Not in use
12 Not in use
13 Thermostart---glow (yellow) is on when the starter
switch is in the glow position
14 Rear power take---off (yellow) is disengaged with PTO
clutch lever, max 5 min
15 Parking brake (red) is applied
16 Low fuel level (yellow), comes on when about 14 l fuel
is left without extra tank
17 Battery charging (red) is on when charging does not
operate
18 Not in use
19 Not in use
20 Not in use
21 Differential lock (yellow) is engaged
22 Not in use
The stop indicator light is operated at the same as the
engine oil pressure indicator light.
If only the central warning light (STOP) starts to flash, the
engine temperature is too high (can be seen also on the
temperature gauge).
CAUTION: If the central warning light (stop) starts to
flash when the tractor has been driven the engine
must be stopped immediately and the fault must be
repaired before continuing again
.
When the starter switch is turned on to position 1, the
following indicator lights must come on:
--- engine oil pressure (
5
)
--- stop light is flashing (
7
)
--- parking brake (
15
), when the parking brake is applied
--- battery charging (
17
)
D 2.2.2.7.
Infoline---instrument panel (as stan-
dard), operating hour meter (2
.7
)
2
.7
69--- 24
The hourmeter always shows the total number of hours
worked.
Summary of Contents for 600
Page 1: ...Operator s manual 600 900...
Page 111: ...110 J Specifications J 13 Wiring diagram component list on pages 108 109 33202000O 69 1 69 2...
Page 112: ...111 J Specifications Wiring diagram component list on pages 108 109 69 3 69 4...
Page 113: ...112 J Specifications Wiring diagram component list on pages 108 109 69 5...
Page 142: ...Ref no 39 179 21 9 11 2002 Printed in Finland by Kopijyv English...