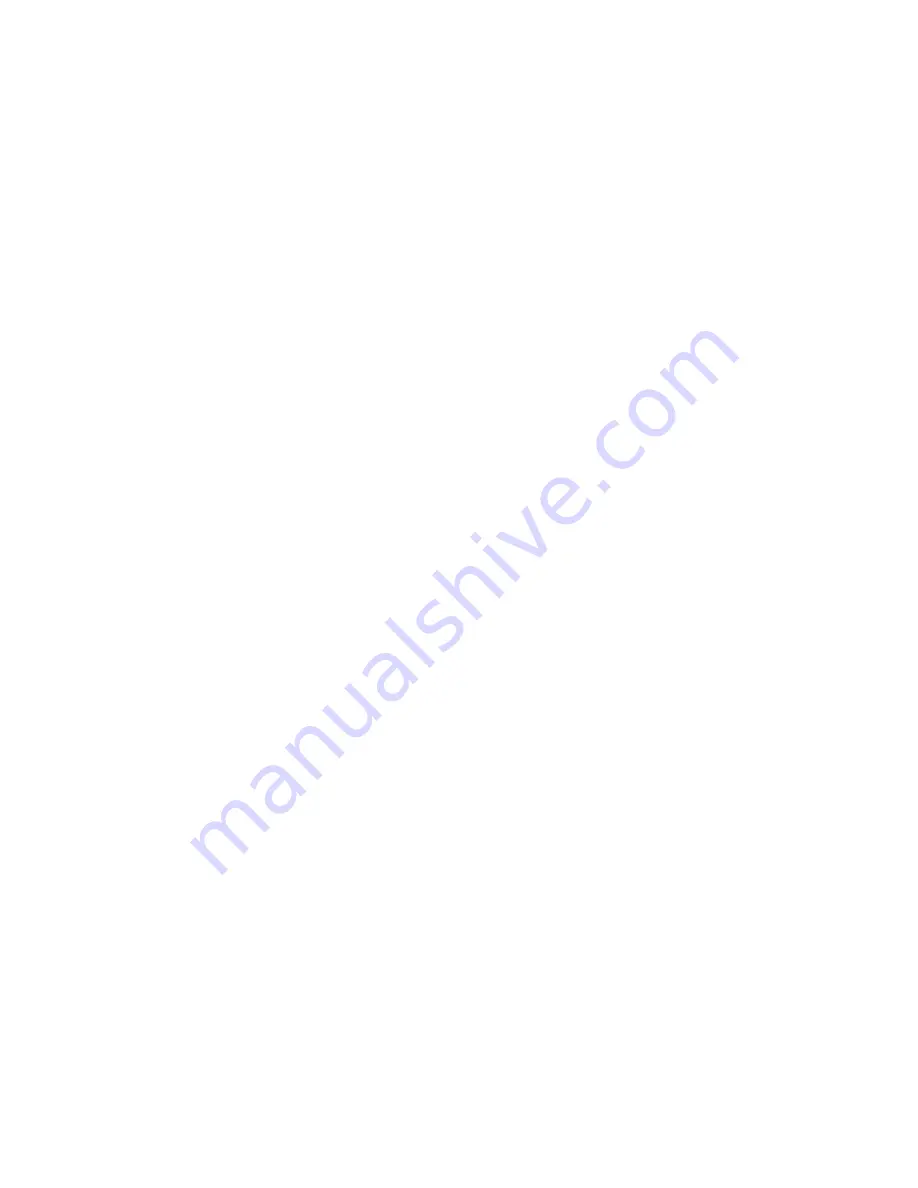
46
g. all necessary safety and precautionary measures shall have been taken and adhered to,
and all measures shall have been taken and adhered to necessary to observe the
applicable government regulations in the context of assembly/installation;
h. the products shipped shall be available at the correct site at the commencement of and
during assembly.
4. Defects not covered by the guarantee are those which occur partially or wholly as a result of:
A. non-observance of the operation and maintenance instructions or other than foreseeable
normal usage;
B. normal wear and tear;
C. assembly/installation by third parties, including the principal;
D. the application of any government regulation regarding the nature or quality of the material
used;
E. materials or goods used in consultation with the principal;
F. materials or goods provided by the principal to the contractor for processing;
G. materials, goods, working methods and constructions insofar as are applied at the express
instruction of the principal, and materials or goods supplied by or on behalf of the principal.
H. components obtained from third parties by the contractor insofar as that party has given no
guarantee to the contractor.
5. If the principal fails to fulfil any obligation properly or on time ensuing from the agreement
concluded between the principal and the contractor or any agreement connected to it, the
contractor shall not be bound by any of these agreements to any guarantee regardless of how it
is referred to. If, without previous written approval from the contractor, the principal commences
disassembly, repair or other work on the product or allows it to be commenced, then every
agreement with regard to guarantee shall be void
6. Claims regarding defects must be submitted in writing as quickly as possible and not later than 14
days after the discovery of such. All claims against the contractor regarding faults shall be void if
this term is exceeded. Claims pertaining to the guarantee must be submitted within one year of
the valid complaint on penalty of invalidity.
7. If the contractor replaces components/products under the terms of his guarantee obligations, the
replaced components/products shall become the property of the contractor.
8. Unless otherwise agreed, a guarantee on repair or overhaul work carried out by the contractor or
other services shall only be given on the correctness of the manner in which the commissioned
work is carried out, this for a period of 6 months. This guarantee only covers the single obligation
of the contractor to carry out the work concerned once again in the event of unsound work. In this
case, subarticle 3A shall apply equally.
9. No guarantee shall be given regarded the inspection conducted, advice given and similar
matters.
10.Alleged failure to comply with his guarantee commitments on the part of the contractor shall not
absolve the principal from his obligations ensuing from any agreement concluded with the
contractor.
11.No guarantee shall be given on products which form a part of, or on work and services on, goods
older than 8 years.
Summary of Contents for VISCOSENSE 2
Page 24: ...23 Figure 12 External connections at interface box 12...
Page 37: ...36 16 CERTIFICATES Certificates are delivered separately...
Page 39: ...38 Figure 19 Dimensions of ViscoSense 2 sensor All dimensions in millimetres 19...
Page 40: ...39 Figure 20 Dimensions of ViscoSense 2 sensor All dimensions in millimetres 20...
Page 41: ...40 Figure 21 Dimensions of ViscoSense 2 sensor All dimensions in millimetres 21...