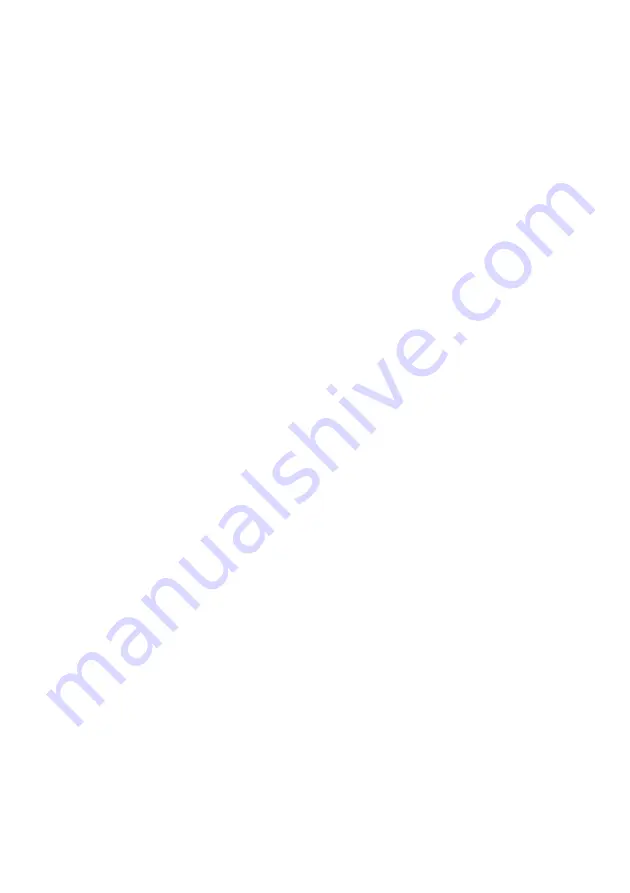
© 2018 Utilicor Technologies Inc.
minicor-3 V1.5
21
Tips for a Successful Coring Operation
(1)
Mark the area to be cored with a paint slash across the core area
before beginning to core. This will help to properly orient the core when
it comes time for reinstatement.
(2)
Before the coring process begins, manipulate the tilt controls on the
skid-steer to make sure the
minicor-3
is level and flush to the ground.
(3)
Ensure that the appropriate rate of water is flowing through the pilot bit
and the adapter plate inside the drum. Periodically check for water
flow during the coring operation. If the hole in the pilot bit becomes
blocked with asphalt or other debris, remove build-up by inserting a
thick gauge wire into center hole to clean it out.
Do not core without
adequate water flow to the centre pilot bit.
(4)
Let the diamond tipped cutting drum do the work of cutting without
excess pressure being applied. Slow, continuous turning of the orbital
control wheel will allow the coring teeth to work and cut through the
pavement without experiencing drum kick back, or stalling of the
hydraulic motor. You are applying too much downward pressure if the
drum stops turning, or if the
minicor-3
lifts off the ground.
(5)
Remember to raise the coring drum completely out of the cut area
periodically during the coring operation. This will help to remove any
build up of suspended solids and cutting debris that can cause the
core to become lodged in the drum. Keep the cut space surrounding
the core or “kerf” clean and free of debris.
(6)
You will know you are through the concrete / asphalt pavement when
the slurry changes color, and begins to include roadbed materials such
as sand, gravel, etc. The sound emitted by the bi-cone pilot bit
(typically a "rumble") will change, and not be as noticeable when it cuts
through the bottom of the pavement. Core for another 1"-2" more to
compensate for the additional length of the pilot bit and for any slant or
unevenness in the core bottom.