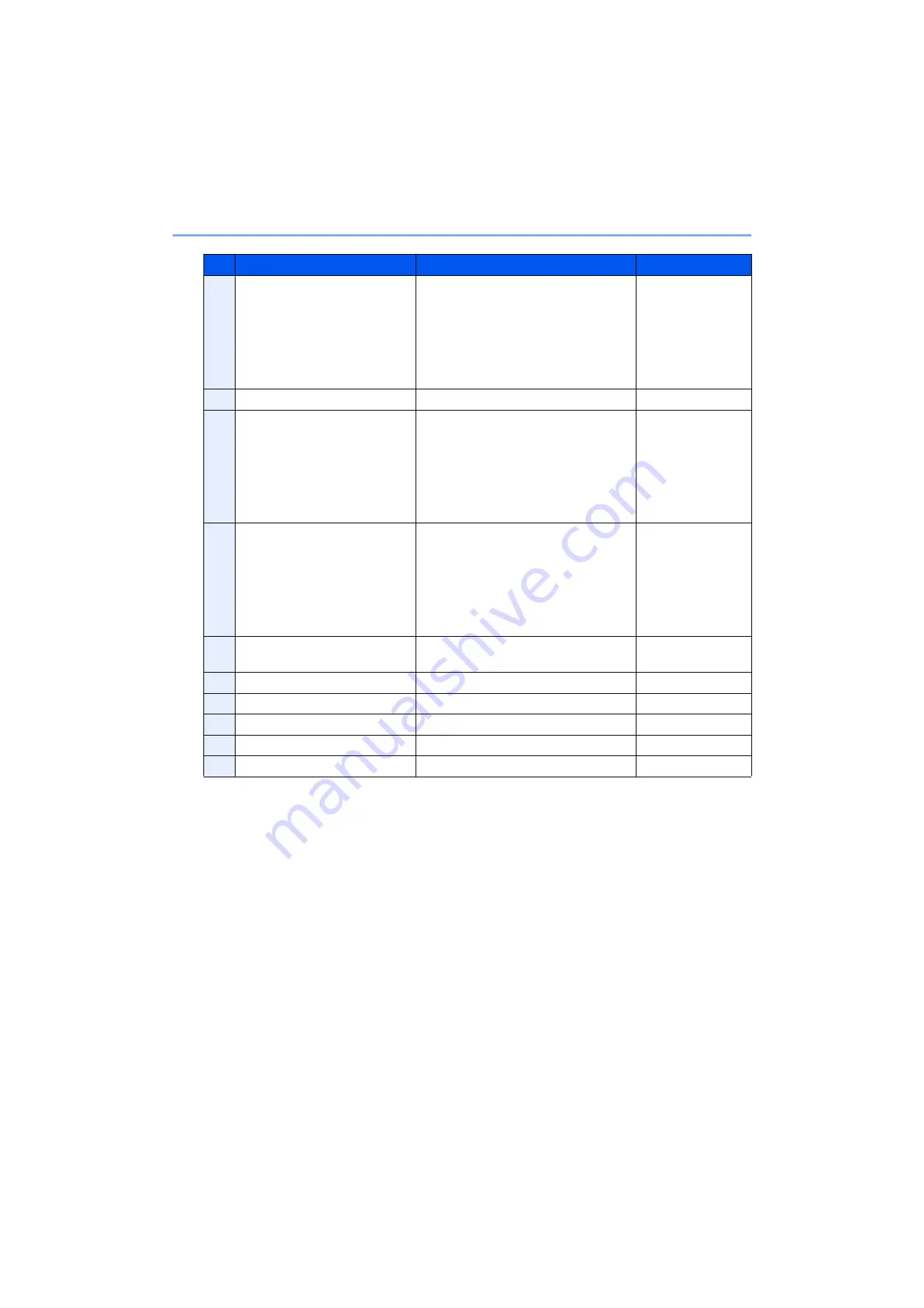
3-12
Machine Design
>
Electric parts
[CONFIDENTIAL]
*100V
、
*2: 120 V
、
*3: 220-240 V
、
*4: 240 V
、
*5: 45 ppm model
、
*6: 50 ppm model
、
*7: 55 ppm model
、
*8: 60 ppm model
、
*9: 50/
55/60 ppm model
11
Eject sensor
-
(FK-3201)
(FK-3202)
(FK-3200)
(FK-3301)
(FK-3302)
(FK-3300)
-
(302V393050)*5,*1
(302V393060)*5,*2
(302V393040)*5,*3,*4
(302TP93020*9,*1
(302TA93050)*9,*2
(302TA93040*9,*3,*4
12
Fuser pressure release sensor
PARTS SENSOR OPT SP
303M89426_
13
Fuser thermistor 1
-
(FK-3201)
(FK-3202)
(FK-3200)
(FK-3301)
(FK-3302)
(FK-3300)
-
(302V393050)*5,*1
(302V393060)*5,*2
(302V393040)*5,*3,*4
(302TP93020*9,*1
(302TA93050)*9,*2
(302TA93040*9,*3,*4
14
Fuser thermistor 2
-
(FK-3201)
(FK-3202)
(FK-3200)
(FK-3301)
(FK-3302)
(FK-3300)
-
(302V393050)*5,*1
(302V393060)*5,*2
(302V393040)*5,*3,*4
(302TP93020*9,*1
(302TA93050)*9,*2
(302TA93040*9,*3,*4
15
Toner sensor
-
(DV-3100)
-
(302LV9308_)
16
Lift sensor *1
PARTS SENSOR OPT SP
303M89426_
17
Interlock switch
INTER LOCK SWITCH
2FB2716_
18
Rear cover switch
SW.PUSH
7SP0H01
19
Waste toner sensor
PARTS TONER FULL DETECT ASSY SP
302LV9412_
20
Power source switch
PARTS PWB ASSY SWITCH SP
302LV9421_
No.
Name used in service manual
Name used in parts list
Part. No.
Summary of Contents for CA-3100
Page 118: ...4 20 Maintenance Assembly and disassembly a d c f e e c ...
Page 131: ...4 33 Maintenance Assembly and disassembly a b c c d c ...
Page 134: ...4 36 Maintenance Assembly and disassembly c b a b ...
Page 146: ...4 48 Maintenance Assembly and disassembly Optional items a b c d ...
Page 148: ...4 50 Maintenance Assembly and disassembly Optional items a b c ...
Page 271: ... CONFIDENTIAL 2 IB 51 IB 51 Wireless Interface INSTALLATION GUIDE ...
Page 274: ...付録 Installation guide CONFIDENTIAL 3 IB 32B IB 32B IEEE1284 Interface INSTALLATION GUIDE ...
Page 282: ... CONFIDENTIAL 3 5 6 4 1 2 1 2 3 1mm 㟝㫴G㤵㣠 1 2 㛅 G㣙㾌 PF 3100 㦹㢨G㣰G㥐ᶤ ...
Page 283: ... Installation guide 6 HD 6 HD 7 HD 6 HD 7 INSTALLATION GUIDE ...
Page 285: ... Installation guide 7 CA 3100 CA 3100 INSTALLATION GUIDE ...