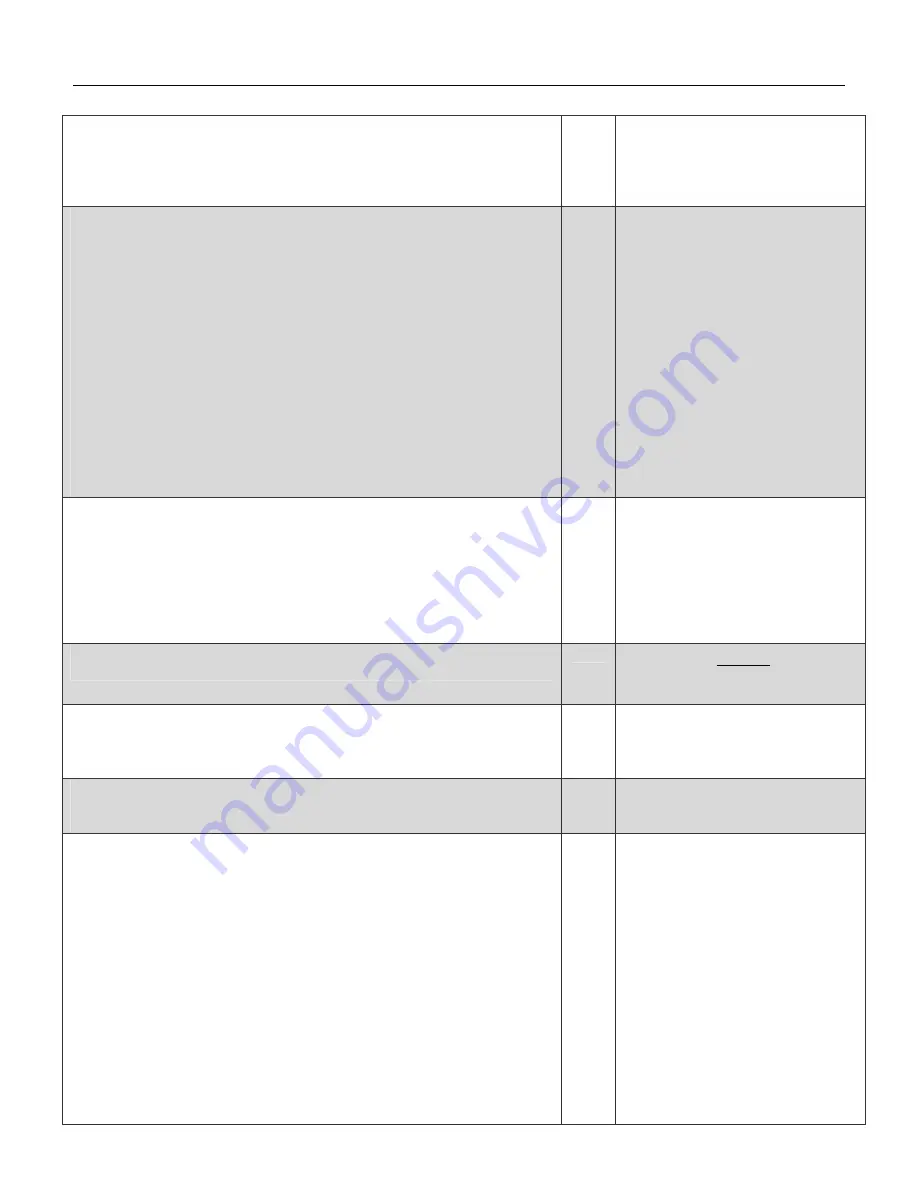
4-78 DRIVE PROGRAMMING
application time. During this period, the HOLD ZERO
SPEED (M06B19) and RAMP HOLD (M02B36) parameters
are set to 1 and so the drive is enabled with zero speed
reference. This ensures that the motor remains stationary
while the brake is being applied.
M12P43 BRAKE POS CONTRL
Closed loop parameter
If this parameter is set to 0, then ramp hold only is
applied when the drive is not active and until the end of
the post-brake release delay to ensure that the speed
reference remains at zero until the brake has released. If
this parameter is set to 1 the position controller is also
enabled (M15P07 = RIGD FFWD) and the local position
reference source is selected (M15P01 = LOCAL REF,
M15B21 = 1) during the period when ramp hold is active.
Assuming parameter M15B08 (ABS POS ENABLE) is set to
its default value of 0, the position controller can help limit
the movement of the motor when the brake is released.
When parameter M12P43 is changed from 1 to 0,
parameter M15P01 is set to “DRIVE PG” and M15P07 is set
to “DISAB POS”. Only active if M12B44 (EN TORQ
PROVING) = 0.
R-W
Range: 0 or 1
Default: 0
M12B44 EN TORQ PROVING
Closed loop parameter
If set to 1, the Closed loop mechanical brake sequence will
build-up a positive torque in a direction to lift the load
prior to setting M12B34 (BRAKE RELEASE) to 1 which
releases the mechanical brake. If M12B44 is set to 0, the
Closed loop mechanical brake sequence will hold zero
speed or zero position while the mechanical brake is
applied and for a time delay after it is released.
R-W
Range: 0 or 1
Default:
M12P45 TORQ PROVING REF
Closed loop parameter
Sets the Torque Proving level in percent of rated torque.
R-W
Range: 0 to
%
100
06
P
05
M
35
P
11
M
Default: 20.0
M12P46 TORQPROVING TOUT
Closed loop parameter
The Torque Proving Time Out time is the allowed time for
drive output torque to reach the level set by M12P45
before a “TORQ PROV” fault is generated.
R-W
Range: 0 to 100.0 Sec
Default: 0.5
M12B47 TORQPROOF STATUS
Closed loop parameter
M12B47 = 1 indicates that the drive output torque has
reached the torque proving level set by M12P45.
R-O
Range: 0 or 1
Default:
M12B48 EN BRAKE ACKNLDG
Closed loop parameter
If set to 1, the Closed loop mechanical brake sequence will
look for a “feedback” signal from the mechanical brake to
insure that it is either released or applied before
continuing with sequencing.
If M12B48 is set to 1, the Closed loop mechanical brake
sequence will wait for M12B49 (BRAKE ACK FEEDBK) to be
a 1 and then apply the POSTBRAK REL DLY (M12P41) to
allow for the mechanical brake release time before
continuing with sequencing. It will also wait for M12B49
(BRAKE ACK FEEDBK) to be a 0 and then apply the BRAKE
APPLY DLY (M12P42) to allow for the brake apply time
before continuing with the sequencing.
If M12B48 is set to 0, the Closed loop mechanical brake
sequence will just use the POSTBRAK REL DLY (M12P41)
R-W
Range: 0 or 1
Default:
Summary of Contents for PHOENIX EX
Page 1: ...INSTRUCTION MANUAL PHOENIX EX 3 TO 3500 HP VECTOR AC DRIVE ...
Page 12: ...1 8 INTRODUCTION END INTRODUCTION SECTION ...
Page 28: ...2 16 INSTALLATION AND WIRING Figure 2 3 Recommended Power Wiring ...
Page 32: ...2 20 INSTALLATION AND WIRING Figure 2 5 Control Logic and Signal Wiring ...
Page 56: ...Figure 4 2 Menu 1 Frequency Reference Limits and Filters 4 2 MENU AND PARAMETER DESCRIPTION ...
Page 57: ...Figure 4 3 Menu 2 Ramps MENU AND PARAMETER DESCRIPTION 4 3 ...
Page 58: ...Figure 4 4 Menu 3 Speed Input and Speed Loop 4 4 MENU AND PARAMETER DESCRIPTION ...
Page 59: ...MENU AND PARAMETER DESCRIPTION 4 5 Figure 4 5 Menu 4 Current Limits Torque Flux Control ...
Page 60: ...4 6 MENU AND PARAMETER DESCRIPTION Figure 4 6 Menu 5 Motor Control ...
Page 61: ...MENU AND PARAMETER DESCRIPTION 4 7 Figure 4 7 Menu 6 Operational Modes ...
Page 62: ...Figure 4 8 Menu 7 Analog Inputs and Outputs 4 8 MENU AND PARAMETER DESCRIPTION ...
Page 66: ...4 12 MENU AND PARAMETER DESCRIPTION Figure 4 12 Menu 11 Miscellaneous ...
Page 68: ...4 14 MENU AND PARAMETER DESCRIPTION Figure 4 14 Menu 12 Open Loop Brake Function 2 of 5 ...
Page 69: ...MENU AND PARAMETER DESCRIPTION 4 15 Figure 4 15 Menu 12 Closed Loop Brake Function 3 of 5 ...
Page 70: ...4 16 MENU AND PARAMETER DESCRIPTION Figure 4 16 Menu 12 Closed Loop Brake Function 4 of 5 ...
Page 71: ...MENU AND PARAMETER DESCRIPTION 4 17 Figure 4 17 Menu 12 Closed Loop Brake Function 5 of 5 ...
Page 73: ...Figure 4 19 Menu 14 PID Control Loop MENU AND PARAMETER DESCRIPTION 4 19 ...
Page 74: ...Figure 4 20 Menu 15 Position Control 1 of 2 4 20 MENU AND PARAMETER DESCRIPTION ...
Page 75: ...MENU AND PARAMETER DESCRIPTION 4 21 Figure 4 21 Menu 15 Position Control 2 of 2 ...
Page 76: ...Figure 4 22 Menu 17 2nd Motor Parameters 4 22 MENU AND PARAMETER DESCRIPTION ...
Page 153: ...APPENDIX A 3 Standard Drive with Manual Bypass Setup Diagram 2 of 2 ...
Page 155: ...APPENDIX A 5 Interconnect for Option Boards 3000 4040 120 3000 4050 120 ...
Page 156: ...APPENDIX A 6 Isolated Communication Card P N 3000 4135 with Jumper on Position 1 1 of 3 ...
Page 157: ...APPENDIX A 7 Isolated Communication Card P N 3000 4135 with Jumper on Position 2 2 of 3 ...
Page 158: ...APPENDIX A 8 Isolated Communication Card P N 3000 4135 3 of 3 Mounting Diagram ...
Page 162: ...APPENDIX A 12 Digital Encoder Card P N 3000 4140 1 3 of 3 Mounting Diagram ...
Page 164: ...APPENDIX A 14 I O Expansion Board 3000 4150 2 of 2 Mounting Diagram ...
Page 167: ...APPENDIX A 17 Digital Encoder 2 3000 4160 Page 3 of 3 Mounting Diagram ...
Page 168: ...APPENDIX A 18 THIS PAGE INTENTIONALLY LEFT BLANK ...