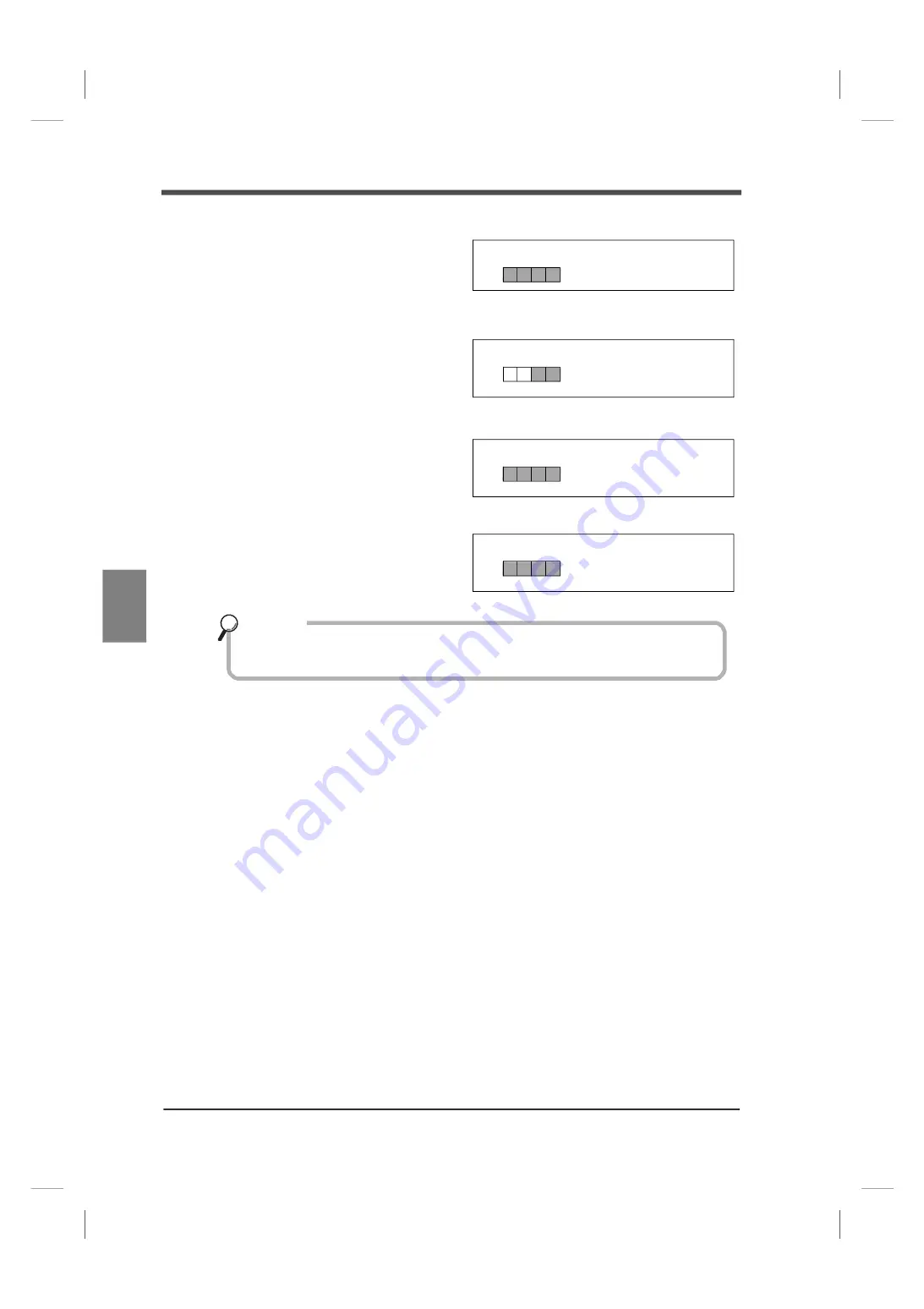
120
6
Useful Functions
120
U
se
fu
l F
un
cti
on
s
Chapter
6
■
Print count
Set print count. Also used as an accumulation
count setting even when not in printer mode.
■
Year setting (setting mode 7-7)
Set current year. Year between 2000 and 2099
can be set.
■
Date setting (setting mode 7-8)
Set current date.
■
Time setting (setting mode 7-9)
Set current time.
[Print count] (setting mode 7-6)
(Input range: 0 to 9999)
[Print count] (setting mode 7-7)
(Input range: 00 to 99)
0
2
Y Y Y Y
[Date setting] (setting mode 7-8)
(Input range: MM: 01 to 12
M M D D
DD: 01 to 31)
[Time setting] (setting mode 7-9)
(Input range: hh: 00 to 23
h h m m
mm: 00 to 59)
Year, date and time work only when equipped with RS-232C interface for printer
connection (option).
Key point
Summary of Contents for F701+
Page 1: ...01AUG2020REV 1 03 WEIGHING INDICATOR F701 OPERATION MANUAL ...
Page 149: ......