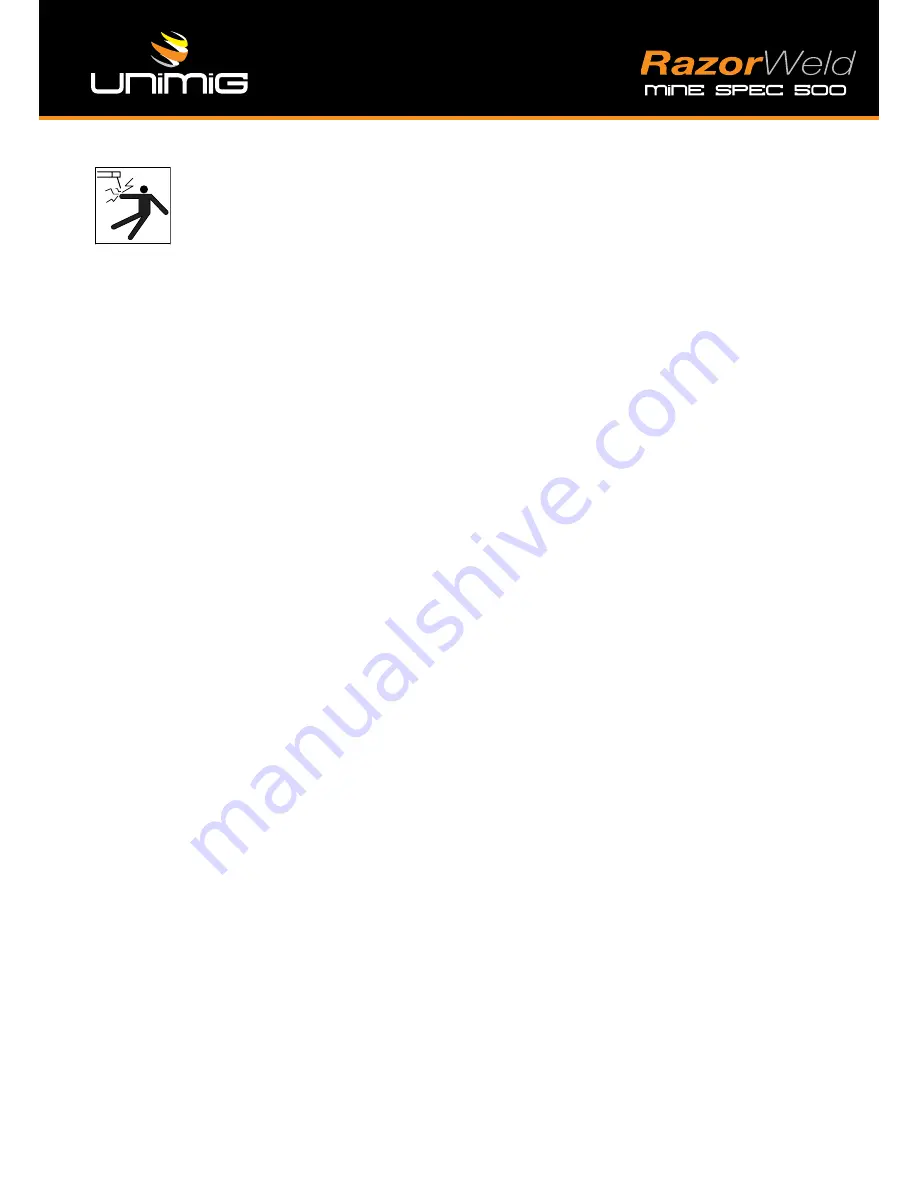
5
ELECTRIC SHOCK CAN KILL
Electric shock: It can kill.
Touching live electrical parts can cause fatal shocks or severe burns.
The electrode and work circuit is electrically live whenever the output is on.
The input power circuit and internal machine circuits are also live when power is on. In Mig/Mag
welding, the wire, drive rollers, wire feed housing, and all metal parts touching the welding wire are
electrically live. Incorrectly installed or improperly grounded equipment is dangerous.
• Connect the primary input cable according to Australian and New Zealand standards and regulations.
• Avoid all contact with live electrical parts of the welding circuit, electrodes and wires with bare hands.
The operator must wear dry welding gloves while he/she performs the welding task.
• The operator should keep the work piece insulated from himself/herself.
• Do not use AC output in damp areas .if movement is confined, or if there is a danger of falling.
• Disconnect input power or stop engine before installing or servicing this equipment .lockout/ tagout input power
according to OSHA 29 CFR 1910.147(see safety standards)
• Properly install and ground this equipment according to its owner’s manual and national, state and local code.
• When making input connections, attach proper grounding conductor first-double-check connections
• Turn off all equipment when not in use.
• If earth grounding of the work-piece is required , ground it directly with a separate cable
• Do not touch the electrode if you are in contact with the work, ground or another electrode from a different welder
• Use only well-maintained equipment, repair or replace damaged parts at once. Maintain unit according to the
manual.
• Wear a safety harness, if working above floor level
• Keep all panels and covers securely in place.
• Clamp cable work with good metal-to-metal contact to work-piece or work cable as near the weld as practical.
• Insulate work clamp when not connected to work-piece to prevent contact with any metal object.
• Do not connect more than one electrode or work cable to any single weld output terminal
Significant dc voltage exists in inverters after stopping engine
• Stop engine on inverter and discharge input capacitors according to instructions in maintenance section before
touching any parts
• Keep cords dry, free of oil and grease, and protected from hot metal and sparks.
• Frequently inspect all cables for wear and tear, replace the cable immediately if damaged,
bare wiring is dangerous and can kill.
• Do not use damaged, under sized, or badly joined cables.
• Do not drape cables over your body.
• RCD safety switch is fitted to this equipment to detect any leakage of current to earth.
Summary of Contents for RazorWeld MS500
Page 72: ...72 Circuit diagram for LN 25P wire feeder adapter ...
Page 73: ...73 Circuit diagram for engine control system ...
Page 74: ...74 Circuit diagram for generator output welding power and auxiliary power ...
Page 75: ...75 Circuit diagram for welding power source ...
Page 76: ...76 Circuit diagram for welding power source ...
Page 81: ...81 ...
Page 82: ...82 ...
Page 83: ...83 ...