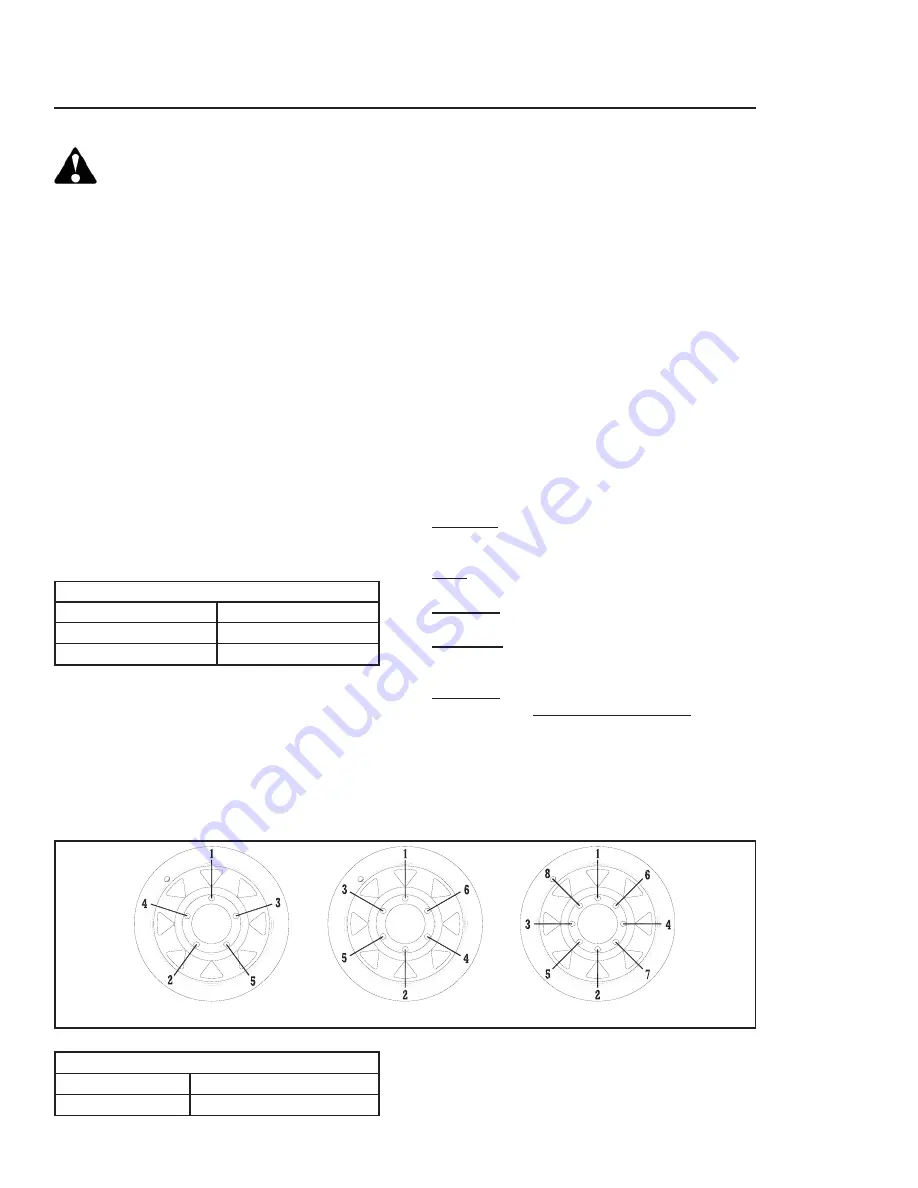
2-10
Service
TIRE PRESSURE
The following is to be used as a
general guide
for tire infl ation and fi gures can vary depending
on specifi c brand of tire used.
It is important
that
tires are inspected after unit is loaded.
Start with minimum pressure indicated. The tire
should stand up with no side-wall buckling or dis-
tress as tire rolls. Record the pressure needed
to support the full load and maintain this pres-
sure to achieve proper tire life.
Do not exceed
maximum recommended tire pressure.
Recommended......100 PSI maximum.
TIRE WARRANTY
For questions regarding new tire warranty,
please contact your local original equipment tire
dealer. Used tires carry no warranty. Follow-
ing are phone numbers and Websites for your
convenience:
Firestone
www.fi restoneag.com
Phone
800-847-3364
Titan
www.titan-intl.com
or
Phone
800-USA-BEAR
Goodyear
Fax 515-265-9301
Trelleborg
www.trelleborg.com
Phone
866-633-8473
Greenball
www.greenball.com
Phone nearest location:
California
800-937-5204
Georgia
800-283-4569
Florida
800-935-0200
Indiana
800-426-4068
Pennsylvania
800-869-6787
Tennessee
800-946-9412
Ohio
800-840-7295
(All tire pressures in psi)
WHEEL TORQUE REQUIREMENTS
CAUTION! IMPROPERLY TORQUED
WHEEL NUTS/BOLTS CAN CAUSE A
LOSS OF IMPLEMENT CONTROL AND MA-
CHINE DAMAGE. TORQUE WHEEL NUTS/
BOLTS TO VALUES IN TABLE. CHECK
TORQUE BEFORE INITIAL USE, AFTER ONE
HOUR OF UNLOADED USE OR AFTER FIRST
LOAD, AND EACH LOAD UNTIL WHEEL NUTS/
BOLTS MAINTAIN TORQUE VALUE. CHECK
TORQUE EVERY 10 HOURS OF USE THERE-
AFTER. AFTER EACH WHEEL REMOVAL
START TORQUE PROCESS FROM BEGINNING.
WARRANTY DOES NOT COVER FAILURES
CAUSED BY IMPROPERLY TORQUED WHEEL
NUTS/BOLTS.
Failure to check torque before fi rst load may
damage wheel nut/bolt seats. Once seats are
damaged, it will become impossible to keep nuts/
bolts tight. Tighten nuts/bolts to the applicable
torque value shown below. Start all nuts/bolts by
hand to prevent cross threading. Torque nuts/
bolts in the recommended sequence as shown
in Diagram 1.
DIAGRAM 1
WHEEL HARDWARE
SIZE
FOOT-POUNDS
1/2-20 (UNF)
75 FT.-LBS.
9/16-18 (UNF)
110 FT.-LBS.
WHEEL TORQUE CHART & TIRE SPECIFICATIONS
Nut/Bolt Location:
1/2-20 (UNF)
Single Wheels
9/16-18 (UNF)
Single Wheels
5 BOLT
6 BOLT
8 BOLT
Summary of Contents for Unverferth 2750
Page 12: ...12 NOTES March 2013...
Page 28: ...Operation 1 16 NOTES...
Page 42: ...2 14 Service MASTER DISCONNECT SWITCH ELECTRICAL SCHEMATIC...
Page 44: ...2 16 Service TRAILER LIGHTING BRAKE ELECTRICAL SCHEMATIC...
Page 45: ...2 17 Service SEED TANK LIGHTING ELECTRICAL SCHEMATIC...
Page 46: ...2 18 Service NOTES...
Page 64: ...3 18 Assembly NOTES...
Page 65: ...4 1 Parts SECTION IV PARTS...
Page 66: ...4 2 Parts OM04430 BOX DECALS 14 14 15...
Page 68: ...4 4 Parts LADDER COMPONENTS OM 04435...
Page 70: ...4 6 Parts DOOR WINDOW PIVOT COMPONENTS OM04431 Revised 082310 1 February 2013...
Page 74: ...4 10 Parts HOPPER COMPONENTS FOR 6 TUBE CONVEYOR OM04428 February 2013...
Page 78: ...4 14 Parts IDLER END COMPONENTS FOR 6 TUBE CONVEYOR OM04427 26 February 2013...
Page 80: ...4 16 Parts IDLER END COMPONENTS FOR 8 TUBE CONVEYOR February 2013...
Page 82: ...4 18 Parts DISCHARGE SPOUT COMPONENTS FOR 6 TUBE CONVEYOR OM04426 Revised 082310 1...
Page 84: ...4 20 Parts DISCHARGE SPOUT COMPONENTS FOR 8 TUBE CONVEYOR OM04539B...
Page 94: ...4 30 Parts CABLE RETURN TARP SYSTEM COMPONENTS February 2013...
Page 100: ...4 36 Parts AXLE WHEEL COMPONENTS Revised 082310 1...
Page 102: ...4 38 Parts UNDERCARRIAGE ELECTRICAL COMPONENTS 24896 WIRING HARNESS...
Page 108: ...4 44 Parts OPTIONAL GOOSE NECK HITCH COMPONENTS Front View Rear View February 2013...
Page 111: ...4 47 Parts NOTES February 2013...
Page 112: ...L MANUALS SEEDTENDER 27260 INDD MARCH 2013 3 JUNE 2014 4 MARCH 2015 4 www unverferth com...