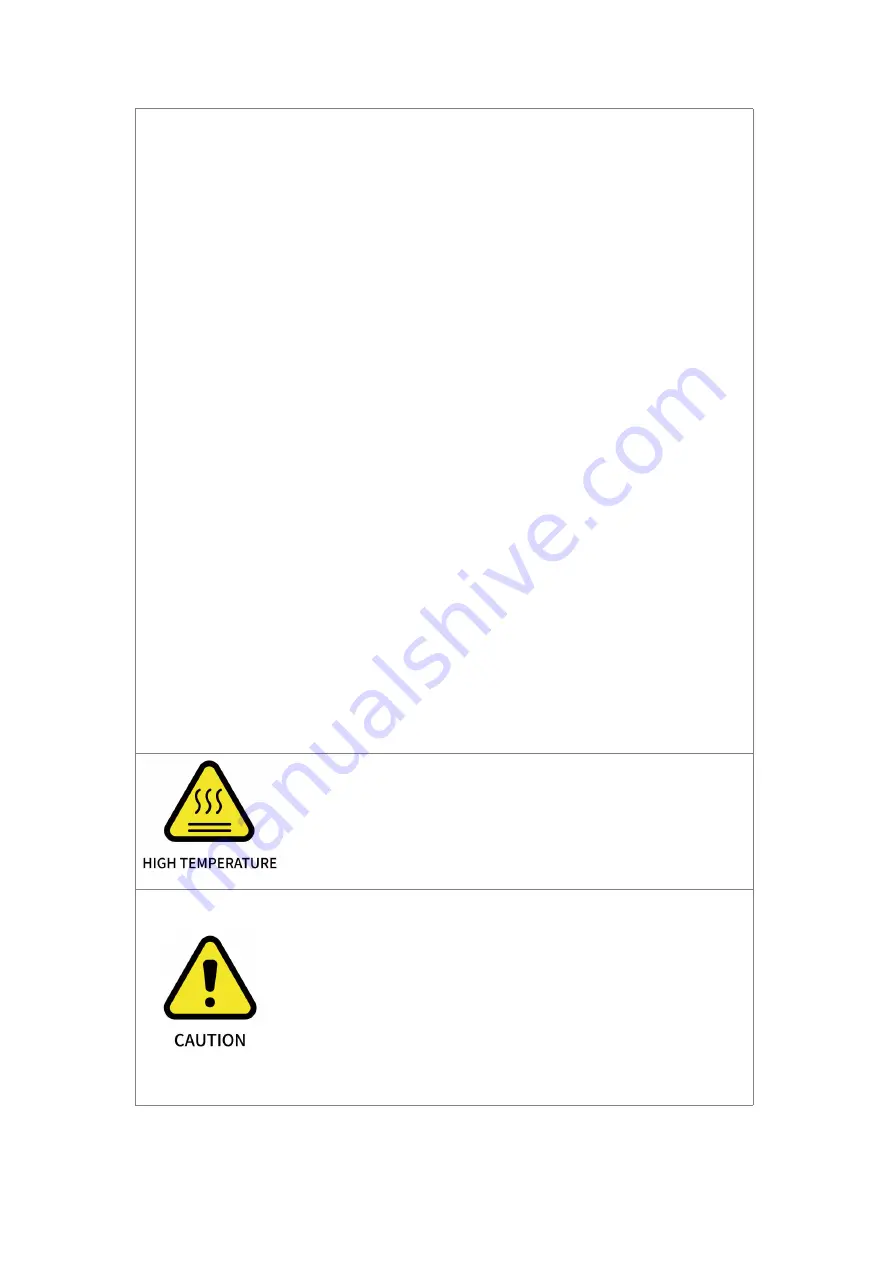
16
before each use (e.g. the operational safety and the possible
damage of the robotic arm and other device systems).
5. Preliminary testing and inspection for both robotic arm and
peripheral protection system before production is essential.
6. The operator must be trained to guarantee a correct
operation procedure when using SDK(Python/ROS/C++)
and graphical interface xArm Studio.
7. A complete safety assessment must be recorded each time
the robotic arm is re-installed and debugged.
8. When the robotic arm is in an accident or abnormal
operation, the emergency stop switch needs to be pressed
down to stop the movement, and the posture of the robotic
arm will slightly brake and fall.
9. The xArm joint module has brakes inside, which will
remain manipulator’s pose when a power outage occurs.
10. When the robotic arm is in operation, make sure no people
or other equipment are in the working area.
11. When releasing the brakes of xArm, please take protective
measures to prevent the robotic arm or operator from
damage or injury.
12. When connecting the xArm with other machinery, it may
increase risk and result in dangerous consequences. Make
sure a consistent and complete safety assessment is
conducted for the installation system.
1. The robotic arm and Control Box will generate heat during
operation. Do not handle or touch the robotic arm and
Control Box while in operation or immediately after the
operation.
2. Never stick fingers to the connector of the end-effector.
1. Make sure the robotic arm’s joints and tools are installed
properly and safely, and check the status for all circuits.
2. Make sure that there is enough space for the manipulator to
move freely.
3. Make sure that there is no obstacle in the robotic arm’s
working space.
4. The Control Box must be placed outside the working range
of the robotic arm to ensure the emergency stop button can