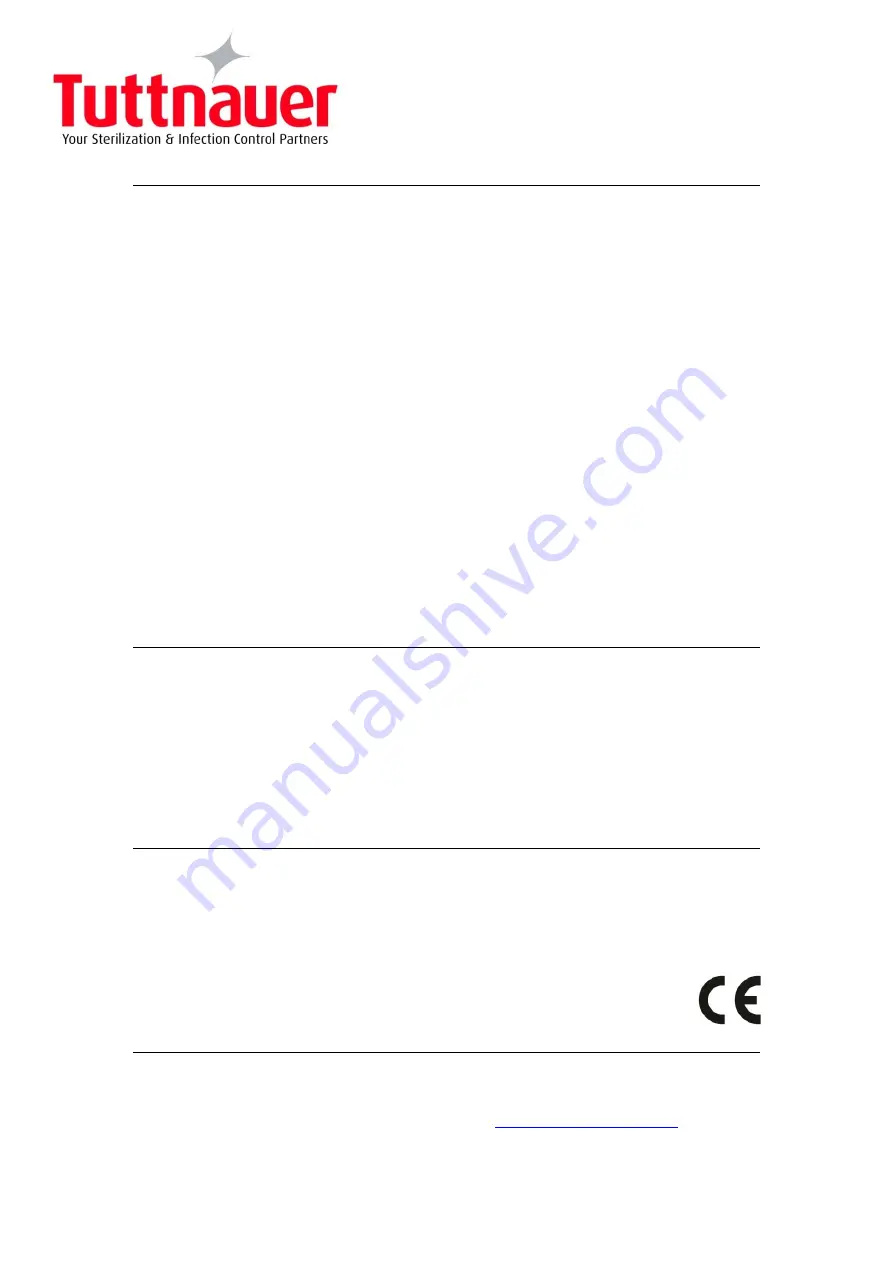
1.1.1
Operation and Maintenance
Manual
Electronic Laboratory Autoclaves
Models LABSCI 15LV
ELV-D: standard autoclave
C: optional system for fast cooling
PV: optional vacuum pump
BH: optional bio hazard filtration
WR: water recycling system
F: optional fan for super-fast cooling
Cat. No. MAN205-0448007EN Rev. L
Heidolph North America,
1235 N Mittel Blvd. Suite B Wood Dale IL 60191
Tel: 224-265-9600