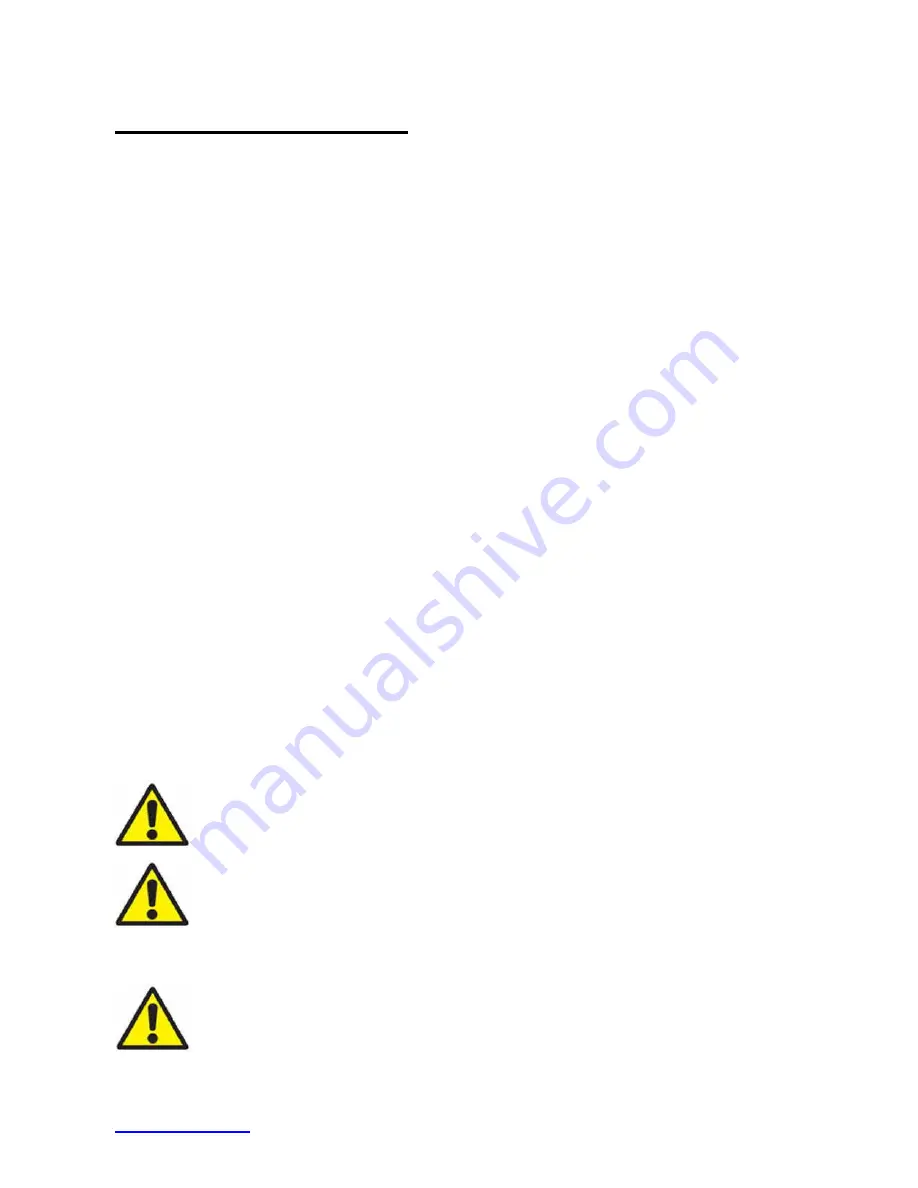
trinityhighway.com
5
Revision
A
November
2019
Limitations and Warnings
Trinity
Highway,
in
compliance
with
MASH
“Recommended
Procedures
for
the
Safety
Performance
of
Highway
Safety
Features”,
contracts
with
FHWA
approved
testing
facilities
to
perform
crash
tests,
evaluation
of
tests,
and
submittal
of
results
to
the
FHWA
for
review.
The
SS180
®
M
was
tested
to
meet
the
impact
criteria,
requirements,
and
guidelines
of
MASH.
These
tests,
specifically
set
forth
by
the
FHWA,
evaluate
product
performance
by
simulating
those
impacts
outlined
by
MASH
involving
a
typical
range
of
vehicles
on
our
roadways,
from
lightweight
cars
(approx.
2420
lb.
[1100kg])
to
full
size
pickup
trucks
(approx.
5000
lb.
[2270
kg])
as
specified
by
the
FHWA.
A
product
can
be
certified
for
multiple
Test
Levels.
The
SS180
®
M
is
certified
to
the
Test
Level
as
shown
below:
Test
Level
3:
62
mph
[100
km/h]
These
FHWA
directed
tests
are
not
intended
to
represent
the
performance
of
systems
when
impacted
by
every
vehicle
type
or
every
impact
condition
existing
on
the
roadway.
This
system
is
tested
only
to
the
test
matrix
criteria
of
MASH
as
approved
by
the
FHWA.
Trinity
Highway
expressly
disclaims
any
warranty
or
liability
for
injury
or
damage
to
persons
or
property
resulting
from
any
impact,
collision
or
harmful
contact
with
products,
other
vehicles,
or
nearby
hazards
or
objects
by
any
vehicle,
object
or
person,
whether
or
not
the
products
were
assembled
in
consultation
with
Trinity
Highway
or
by
third
parties.
The
SS180
®
M
is
intended
to
be
assembled,
delineated,
and
maintained
within
specific
state
and
federal
guidelines.
It
is
important
for
the
highway
authority
specifying
the
use
of
a
highway
product
to
select
the
most
appropriate
product
configuration
for
its
site
specifications.
The
customer
should
be
careful
to
properly
select,
assemble,
and
maintain
the
product.
Careful
evaluation
of
the
site
lay
out,
vehicle
population
type;
speed,
traffic
direction,
and
visibility
are
some
of
the
elements
that
require
evaluation
in
the
selection
of
a
highway
product.
After
an
impact
occurs,
the
debris
from
the
impact
should
be
removed
from
the
area
immediately
and
the
product
should
be
evaluated
and
restored
to
its
original
specified
condition
or
replaced
as
soon
as
possible.
All
components
and
assemblies
should
be
inspected
and
any
parts
that
are
damaged
should
be
replaced
with
original
Trinity
Highway
replacement
parts.
Contact
the
Customer
Service
Department
prior
to
repair
if
you
have
any
questions
(p.
3).
Warning:
It
is
the
responsibility
of
the
installer
to
ensure
that
the
SS180
®
M
and
delineation
used
meet
all
federal,
state,
specifying
agency,
and
local
specifications.
Warning:
It
is
the
responsibility
of
the
installer
to
ensure
that
your
assembly
meets
all
appropriate
Manual
on
Uniform
Traffic
Control
Devices
(MUTCD)
and
local
standards.
Host Vehicle Tare Weights should be between 6150kg and 11,000kg.
Warning: Roll-ahead distance is 6.4m. Plan your TMA deployment accordingly.
Summary of Contents for INGAL SS180 M
Page 40: ...trinityhighway com 38 Revision A November 2019...
Page 41: ...trinityhighway com 39 Revision A November 2019...
Page 42: ...SS180 M trinityhighway com 40 Revision A November 2019...
Page 43: ...626592 1 of 3 Support Frame Assembly trinityhighway com 41 Revision A November 2019...
Page 44: ...626592 2 of 3 trinityhighway com 42 Revision A November 2019...
Page 45: ...626592 3 of 3 trinityhighway com 43 Revision A November 2019...
Page 46: ...626605 Cartridge A 626605 trinityhighway com 44 Revision A November 2019...
Page 47: ...626611 Cartridge B Cartridge B trinityhighway com 45 Revision A S November 2019...
Page 48: ...626628 Miscellaneous Part Assembly trinityhighway com 46 Revision A November 2019...
Page 49: ...626614 Impact Face Assembly trinityhighway com 47 Revision A November 2019...
Page 50: ...626612 1 of 3 Hydraulic Control Assembly trinityhighway com 48 Revision A November 2019...
Page 51: ...626612 2 of 3 626612 2 of 3 trinityhighway com 49 Revision A November 2019...
Page 52: ...626612 3 of 3 trinityhighway com 50 Revision A November 2019...
Page 53: ...625152 Hydraulic Cylinder Assembly 625152 trinityhighway com 51 Revision A November 2019...
Page 54: ...626629 Pump Assembly 626629 trinityhighway com 52 Revision A November 2019...
Page 56: ...625180 2 of 4 trinityhighway com 54 Revision A November 2019...
Page 57: ...625180 3 of 4 trinityhighway com 55 Revision A November 2019...
Page 58: ...625180 4 of 4 trinityhighway com 56 Revision A November 2019...
Page 60: ...625143 2 of 3 625143 2 of 3 trinityhighway com 58 Revision A November 2019...
Page 61: ...625143 3 of 3 625143 3 of 3 trinityhighway com 59 Revision A November r 2019...
Page 62: ...616797 Underride Assembly trinityhighway com 60 Revision A November 2019...
Page 63: ...604382 Attachment Assembly trinityhighway com 61 Revision A November 2019...
Page 64: ...Notes trinityhighway com 62 Revision A November 2019...
Page 65: ......