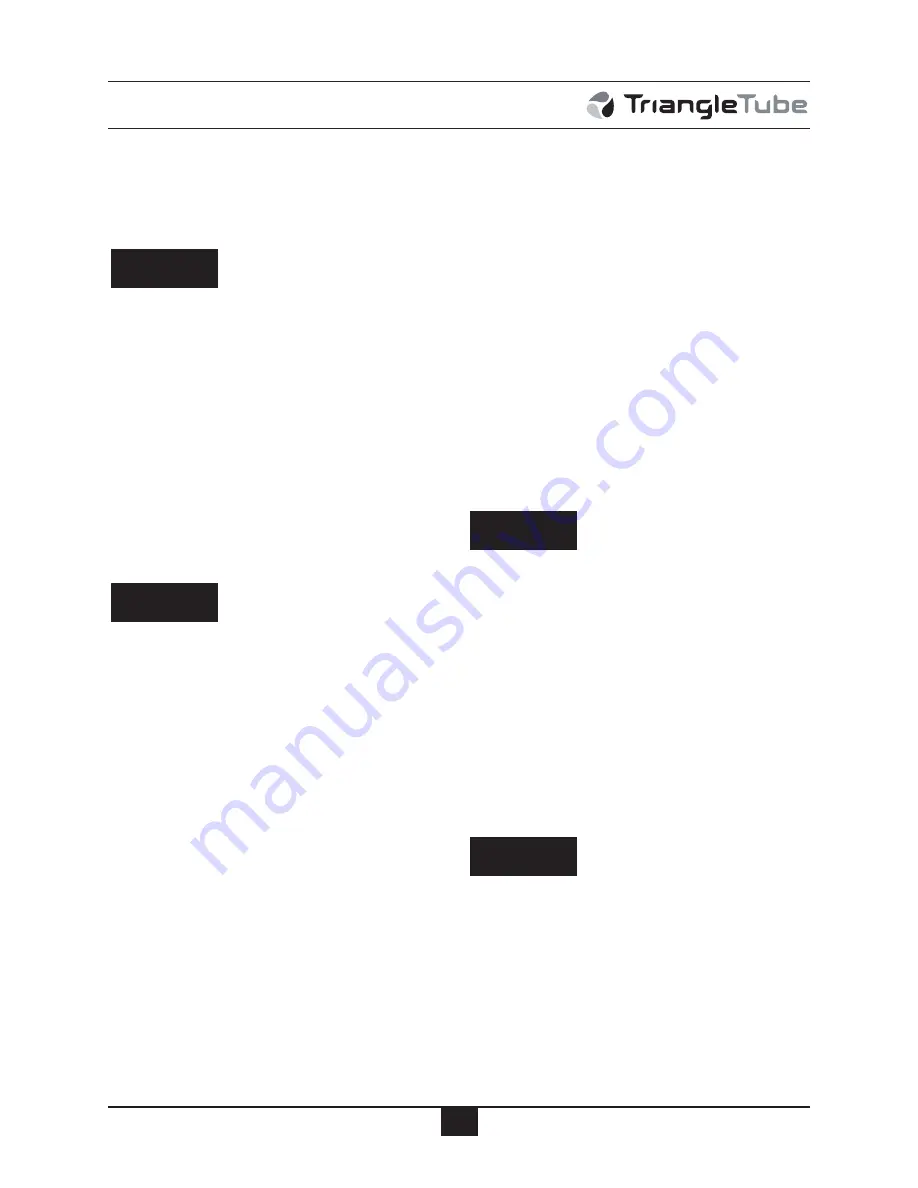
59
Maintenance Procedures
SECTION XVI - Maintenance
Procedures
Maintenance Procedures
The PRESTIGE Solo should be inspect-
ed and serviced annually, preferably at
the start of the heating season, by a qual-
ified service technician. In addition, the
maintenance and care of the unit as out-
lined on page 58 and further explained
on pages 59 through 64 should be per-
formed to assure maximum efficiency
and reliability of the unit. Failure to ser-
vice and maintain the PRESTIGE Solo
and the system components could result
in equipment failure, causing possible
severe personal injury, death or substan-
tial property damage.
The following information provides
detailed instruction for completing the
maintenance items outline in the mainte-
nance schedule on page 58. In addition
to this maintenance, the PRESTIGE
Solo should be serviced at the beginning
of the heating season by a qualified ser-
vice technician.
Reported Problems
Any problems reported by the owner should be
checked, verified and corrected before pro-
ceeding with any maintenance procedures.
Check Surrounding Area
Verify that the area surrounding the PRES-
TIGE Solo is free of combustible / flammable
materials or flammable vapors or liquids.
Remove immediately if found.
Verify that combustion air inlet area is free of
any contaminates. Refer to the materials listed
on page 5 of this manual. If any of these prod-
ucts are in the area from which the unit takes
its combustion air, they must be removed
immediately or the combustion air intake must
be relocated to another area.
Inspect Burner Area
Remove the boiler front jacket panel and ven-
turi inlet elbow.
Vacuum any dirt or debris from the
burner/blower components.
Re-install venturi inlet elbow and front jacket
panel when completed.
Do not use solvents to clean any of the
burner components. The components
could be damaged, resulting in unreli-
able or unsafe operation.
Check System Piping
Inspect all piping (water and gas) on the boiler
system for leaks and verify that the piping is
leak free and properly supported.
Inspect the fittings and components on the unit
and verify they are leak free.
Eliminate all boiler water system leaks.
Continual fresh make-up water will
reduce the heat exchanger life causing
boiler failure. Leaking water may also
cause severe property damage to the sur-
rounding area. Inspect the gas supply
piping using the procedure outlined on
Page 41.
WARNING
WARNING
NOTICE
WARNING
Summary of Contents for Prestige Slol 250
Page 61: ...55 Factory Setting Parameters FACTORY SETTING FOR PARAMETERS ...
Page 72: ...65 Replacement Parts 5 9 8 1 3 5 2 6 7 Fig 26 PRESTIGE Solo Jacket Components ...
Page 73: ...66 Replacement Parts 8 5 9 2 3 4 4 6 7 1 Fig 27 PRESTIGE Solo 60 Internal Components ...
Page 74: ...67 Replacement Parts 8 5 4 4 10 9 7 1 3 2 6 Fig 27A PRESTIGE Solo 175 250 Internal Components ...
Page 75: ...68 Replacement Parts 8 7 10 1 2 3 4 4 5 6 9 Fig 27B PRESTIGE Solo 399 Internal Components ...
Page 77: ...70 Replacement Parts 7 6 9 1 2 10 12 13 4 3 5 8 Fig 28A PRESTIGE Solo 399 Burner Components ...
Page 78: ...71 3 Fig 29 PRESTIGE Solo Electronic Components Replacement Parts ...
Page 80: ...73 Product Specifications Front View PRESTIGE Solo 175 250 ...
Page 83: ...76 Product Specifications Side View PRESTIGE Solo 175 250 ...