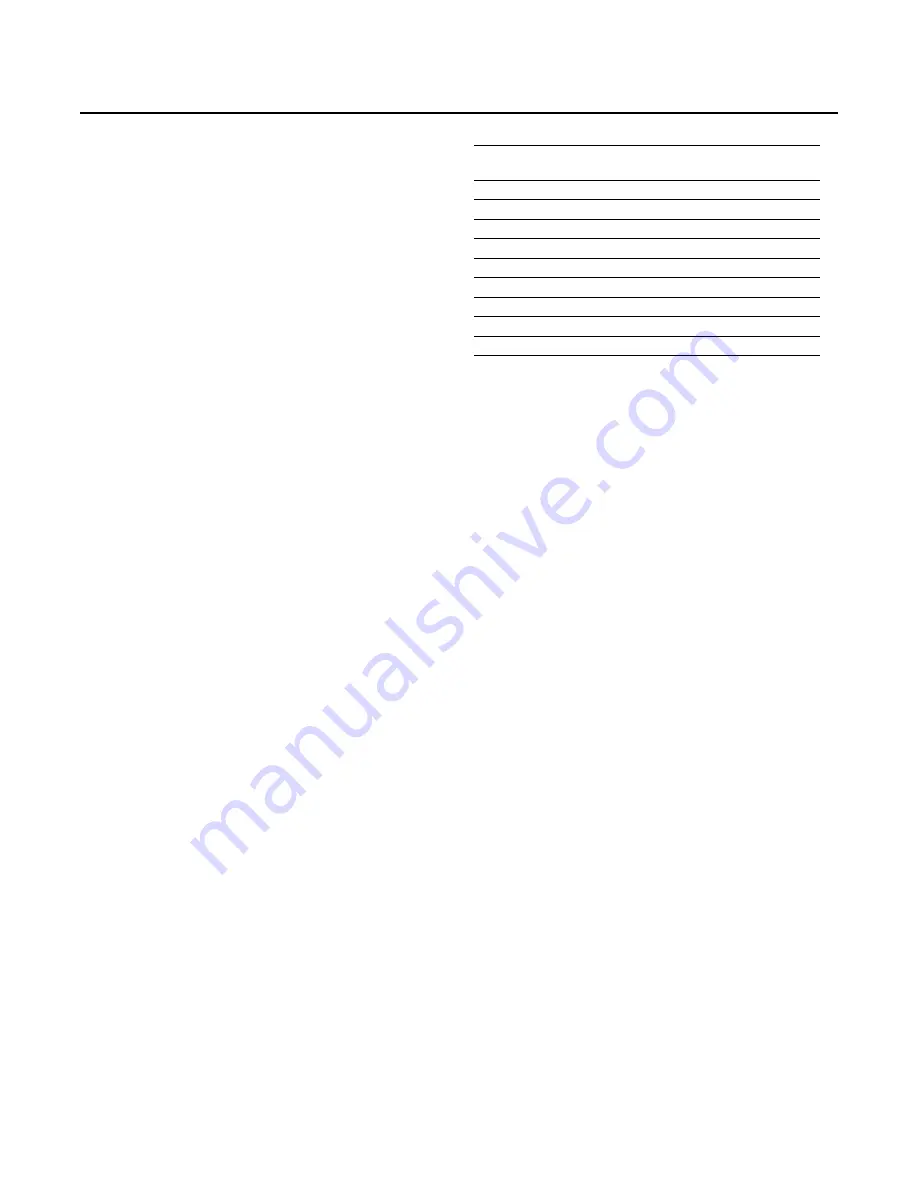
Troubleshooting
40
RT-SVX33E-EN
Zone Temperature Sensor (ZTS)
Service Indicator
The ZSM SERVICE LED is a generic indicator, that will
signal the closing of a Normally Open switch at any time,
providing the Indoor Motor (IDM) is operating. This
indicator is usually used to indicate a clogged filter, or an
air side fan failure.
The RTRM will ignore the closing of this Normally Open
switch for 2 (±1) minutes. This helps prevent nuisance
SERVICE LED indications. The exception is the LED will
flash 40 seconds after the fan is turned “On” if the Fan
Proving Switch is not made.
Clogged Filter Switch
This LED will remain lit the entire time that the Normally
Open switch is closed. The LED will be turned off
immediately after resetting the switch (to the Normally
Open position), or any time that the IDM is turned “Off”.
If the switch remains closed, and the IDM is turned “On”,
the SERVICE LED will be turned “On” again after the 2 (±1)
minute ignore delay.
This LED being turned “On”, will have no other affect on
unit operation. It is an indicator only.
Fan Failure Switch
When the “Fan Failure” switch is wired to the RTOM, the
LED will remain flashing the entire time the fan proving
switch is closed, indicating a fan failure, and it will shut the
unit operations down.
Condensate Overflow Switch
When the condensate overflow switch is closed, a drain
pan overflow condition is indicated and it will shut unit
operations down.
Zone Temperature Sensor (ZTS)
Tests
Note:
These procedures are not for programmable or
digital models and are conducted with the Zone
Sensor Module electrically removed from the
system.
Test 1: Zone Temperature Thermistor
(ZTEMP)
This component is tested by measuring the resistance
between terminals 1 and 2 on the Zone Temperature
Sensor. Below are some typical indoor temperatures, and
corresponding resistive values.
Test 2: Cooling Set Point (CSP) and
Heating Set Point (HSP)
The resistance of these potentiometers are measured
between the following ZSM terminals. Refer to the chart
above for approximate resistances at the given setpoints.
Cool SP = Terminals 2 and 3
Range = 100 to 900 Ohms approximate
Heat SP = Terminals 2 and 5
Range = 100 to 900 Ohms approximate
Test 3: System Mode and Fan Selection
The combined resistance of the Mode selection switch and
the Fan selection switch can be measured between
terminals 2 and 4 on the Zone Sensor. The possible switch
combinations are listed on the following page with their
corresponding resistance values.
Test 4: LED Indicator Test, (SYS ON, HEAT,
COOL & SERVICE)
Method 1
Testing the LED using a meter with diode test function. Test
both forward and reverse bias. Forward bias should
measure a voltage drop of 1.5 to 2.5 volts, depending on
your meter. Reverse bias will show an over Load, or open
circuit indication if LED is functional.
Method 2
Testing the LED with an analog Ohmmeter. Connect
Ohmmeter across LED in one direction, then reverse the
leads for the opposite direction. The LED should have at
least 100 times more resistance in reverse direction, as
compared with the forward direction. If high resistance in
both directions, LED is open. If low in both directions, LED
is shorted.
Method 3
To test LED’s with ZSM connected to unit, test voltages at
LED terminals on ZSM. A measurement of 32 VDC, across
an unlit LED, means the LED has failed.
Zone Temperature
Nominal ZTEMP
Resistance
Nominal CSP or
HSP Resistance
50 F°
10.0 C°
19.9 K-Ohms
889 Ohms
55 F°
12.8 C°
17.47 K-Ohms
812 Ohms
60 F°
15.6 C°
15.3 K-Ohms
695 Ohms
65 F°
18.3 C°
13.49 K-Ohms
597 Ohms
70 F°
21.1 C°
11.9 K-Ohms
500 Ohms
75 F°
23.9 C°
10.50 K-Ohms
403 Ohms
80 F°
26.7 C°
9.3 K-Ohms
305 Ohms
85 F°
29.4 C°
8.25 K-Ohms
208 Ohms
90 F°
32.2 C°
7.3 K-Ohms
110 Ohms