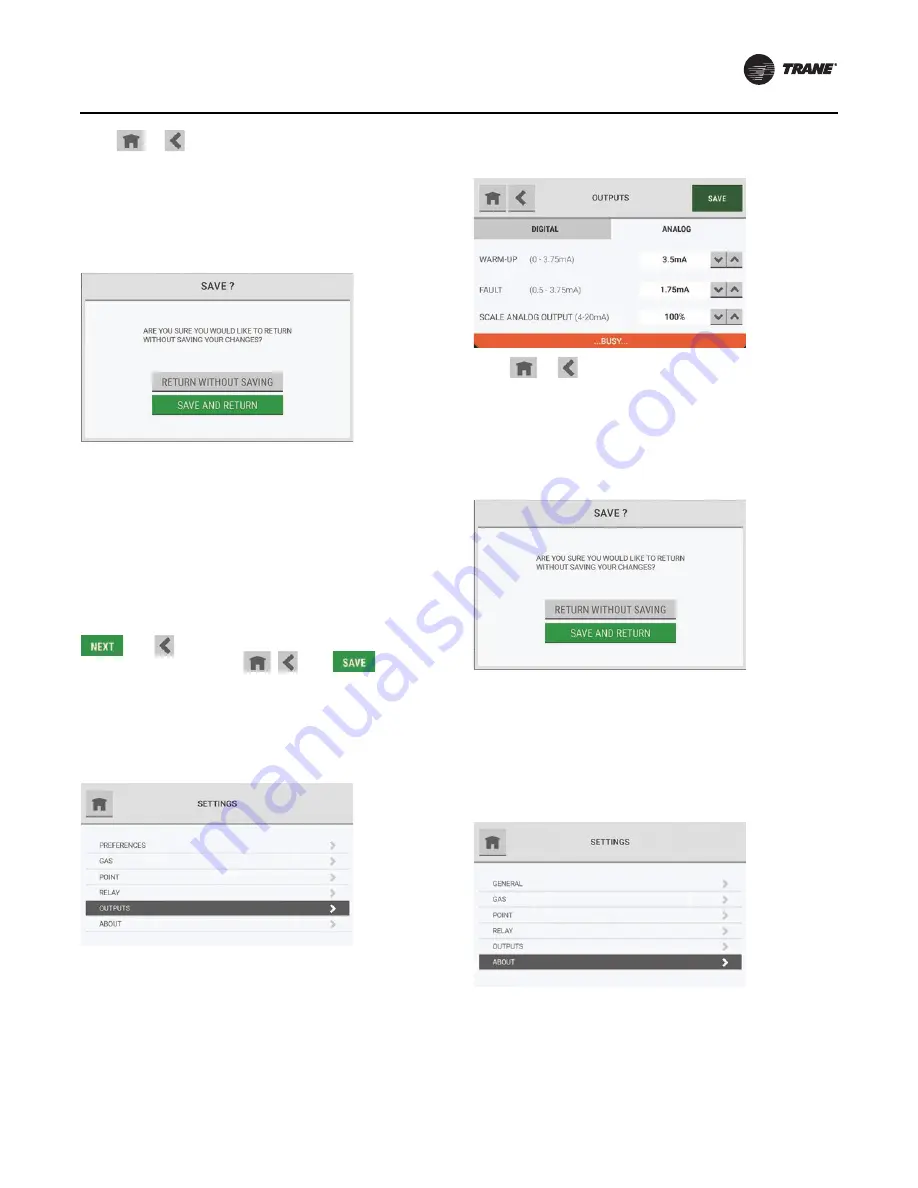
Routine Operation
RMWH-SVX001C-EN
39
If the
or
button is selected while the
Busy
message shows, a pop-up asks whether to abandon the
configuration changes.
•
To return to the
Configure Relays
screen without
saving the changes, select
Return without Saving
.
•
To save the changes and return to the
Configure
Relay
screen, select
Save and Return
.
When the configuration changes have been saved, the
Settings
screen shows.
Communications Output
Use the
Outputs
option to change the configuration
settings for digital and analog outputs.
Except for the buttons that show in the screen headers, the
screens and steps used to change the output settings are
the same as those used during the initial setup.
During the initial setup, the screen headers show the
and
buttons. During routine operation, the
screen headers show the
,
, and
buttons.
When a change is made to the configuration, the
Save
button becomes active.
On the
Settings
screen, select
Outputs
.
To adjust the output configuration settings, go to
“Communications Output,” p. 22
.
While the configuration is being updated, a
Busy
message
shows at the bottom of the
Outputs
screen.
If the
or
button is selected while the
Busy
message shows, a pop-up asks whether to abandon the
configuration changes.
•
To return to the
Outputs
screen without saving the
changes, select
Return without Saving
.
•
To save the changes and return to the
Outputs
screen,
select
Save and Return
.
When the configuration changes have been saved, the
Settings
screen shows.
About
The
About
option shows information about the device
and its component parts.
On the
Settings
screen, select
About
.
Summary of Contents for TruSense RMWH
Page 45: ...Diagnostics RMWH SVX001C EN 45 To see details about an error select it ...
Page 66: ......
Page 67: ......