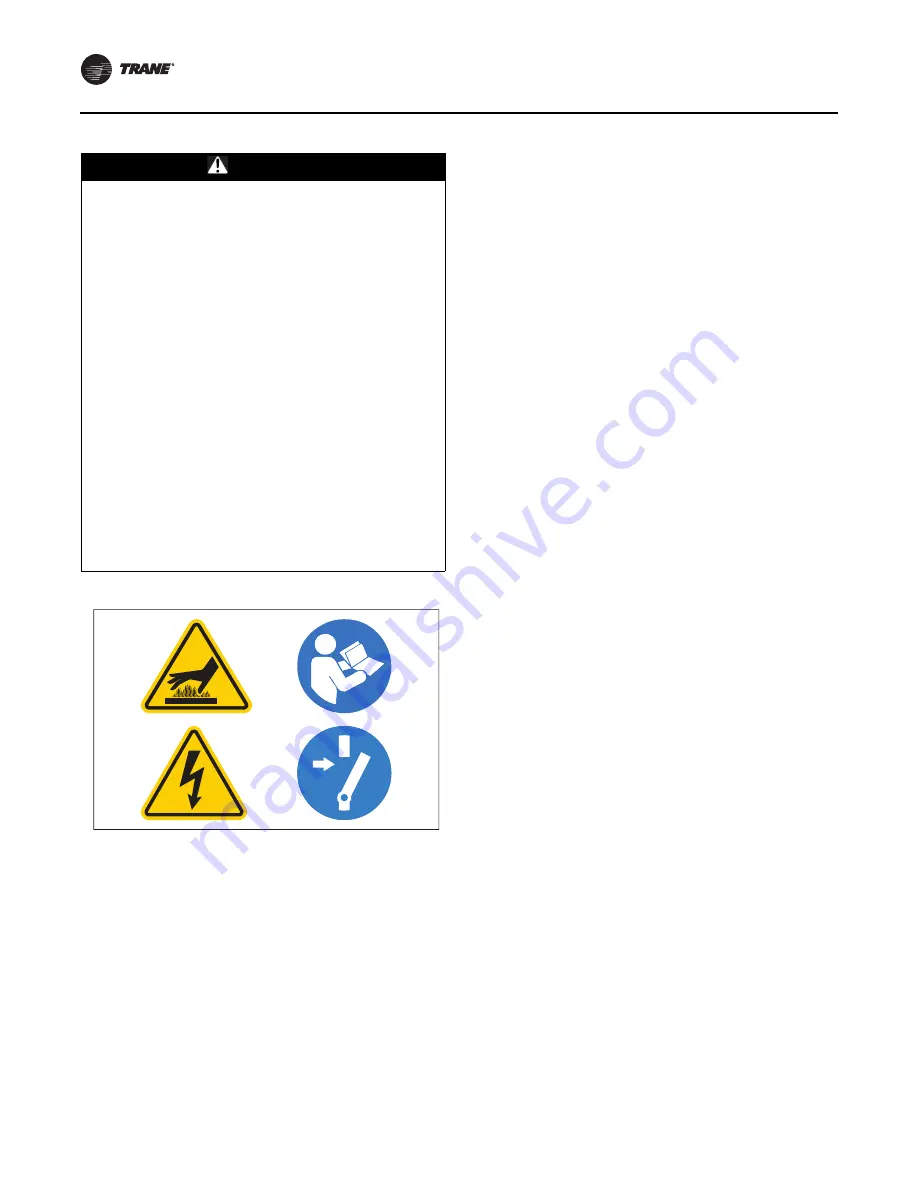
General Information
8
AFDE-SVU02F-EN
Note:
Graphic labels (shown above) are used for CE
application only.
Important:
•
Before servicing, disconnect all power sources and
allow at least 10 minutes for capacitors to discharge.
•
All electrical enclosures—unit or remote—are IP2X.
WARNING
Hazardous Voltage w/Capacitors!
Failure to disconnect power and discharge capacitors
before servicing could result in death or serious injury.
Disconnect all electric power, including remote
disconnects and discharge all motor start/run
capacitors before servicing. Follow proper lockout/
tagout procedures to ensure the power cannot be
inadvertently energized. For variable frequency drives
or other energy storing components provided by Trane
or others, refer to the appropriate manufacturer’s
literature for allowable waiting periods for discharge of
capacitors. Verify with an appropriate voltmeter that all
capacitors have discharged.
•
Before working on the controller, check to be sure
capacitors are discharged with a DC voltmeter on the
1000V scale. Charged capacitors require at least
10 minutes to discharge to less than 50Vdc after line
power is removed.
•
Before proceeding with the startup procedure,
disconnect and lockout all incoming power to the
drive controller!
For additional information regarding the safe discharge
of capacitors, see PROD-SVB06*-EN.
X39003893001A