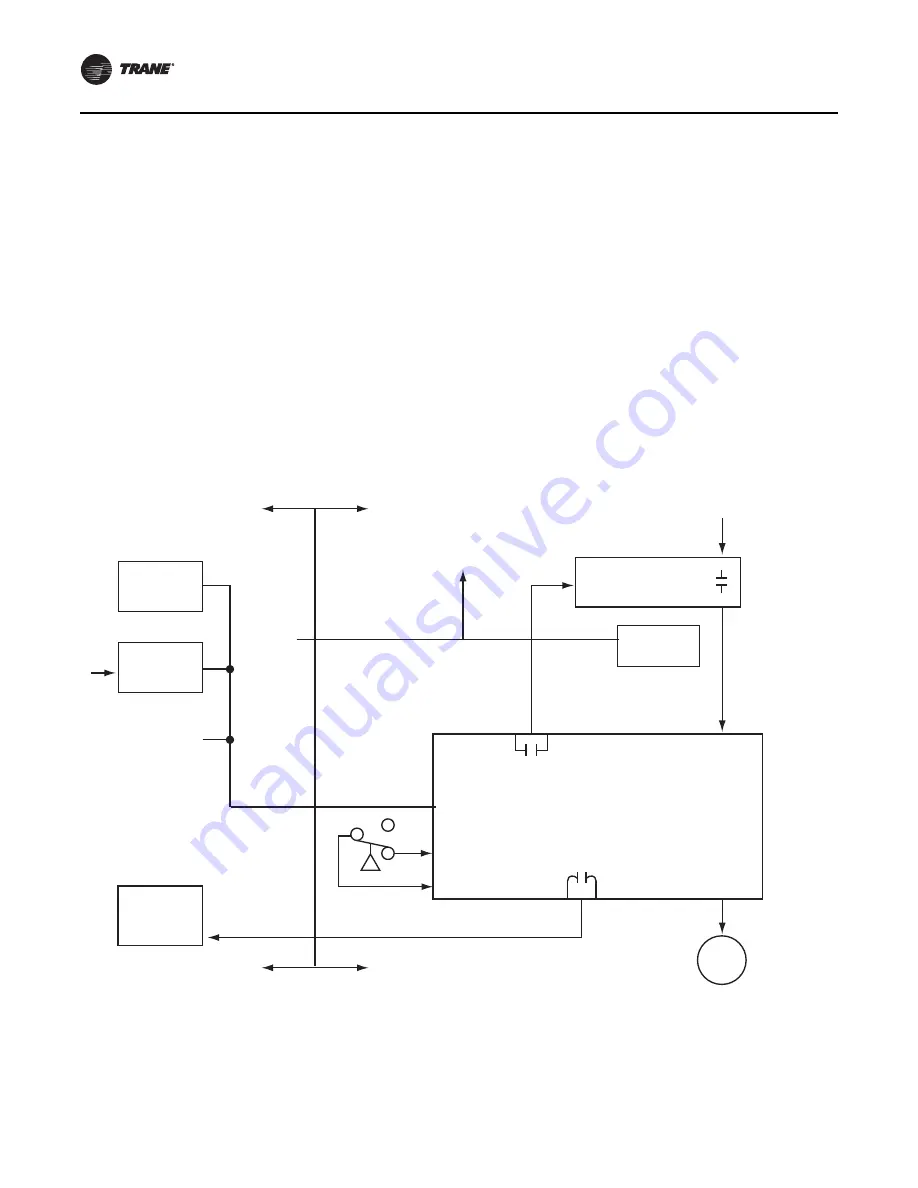
UC800 AFD Operation
42
AFDE-SVU02F-EN
UC800 Interface to Adaptive Frequency
Drive
Communications between the UC800 and the AFD are
handled via the Machine Bus
(“M-bus”) connected to the RS-485 AFD Comm Interface
module. Signals digitally sent over the M-bus include start,
stop, speed change, and drive faults.
At start of the compressor motor a signal corresponding to
the starting frequency (38 Hz) is sent to the drive.
The digital speed signal is set-up such that the AFD
operates over a 38–60 Hz frequency range.
AFD faults are sent over the M-bus to the UC800 controls
for communication on the Tracer AdaptiView display.
High Pressure Cutout – The inverter accepts a NC HPC
switch (at terminals 2X1-3 and 2X1-4. In the event of a
chiller high pressure condition, the HPC switch opens, the
drive shall shut down and de-energize the motor.
Output contacts are required to control the load of the
refrigerant/oil pump motor and the cooling circulating
pump. The contacts are Normally Open, and closed when
the AFD energizes the motor.
Note:
Unlike locked rotor amps associated with
electromechanical starters, the phase currents are
not expected to rise above 85 percent RLA prior to
1.6 seconds following the sending of the speed
signal, after which they then remain above
85 percent RLA until the compressor motor has
come up to speed.
An “Up-to-Speed” signal must occur before the Maximum
Acceleration Timer times out (plus 15 seconds) or a
MANUAL RESET (MMR) alarm will occur.
The block diagram (see
) shows the
communication of the starter module to Unit Mounted
Inverter Interface controls interconnecting circuits.
The Oil Pump Interlock load is 115 Vac, 3/4 hp reset.
Figure 19.
UC800 to unit mounted inverter interface block diagram
AFD
Chiller
UC800
Power Supply
Oil/Cooling
Pump
Interlock
To other
LLIDS
115/50/60
Power
4-wire
Machine Bus
24 Vdc Power
and Ground
115/50/60
Power
3-phase line
Circuit Breaker
line in with
115 Vac
115 Vac
HPC
24 Vdc Sense
Adaptive Frequency Drive
Motor
AFD
Chiller
Recomm
HPC
24 Vdc
Out
24 Vdc
In