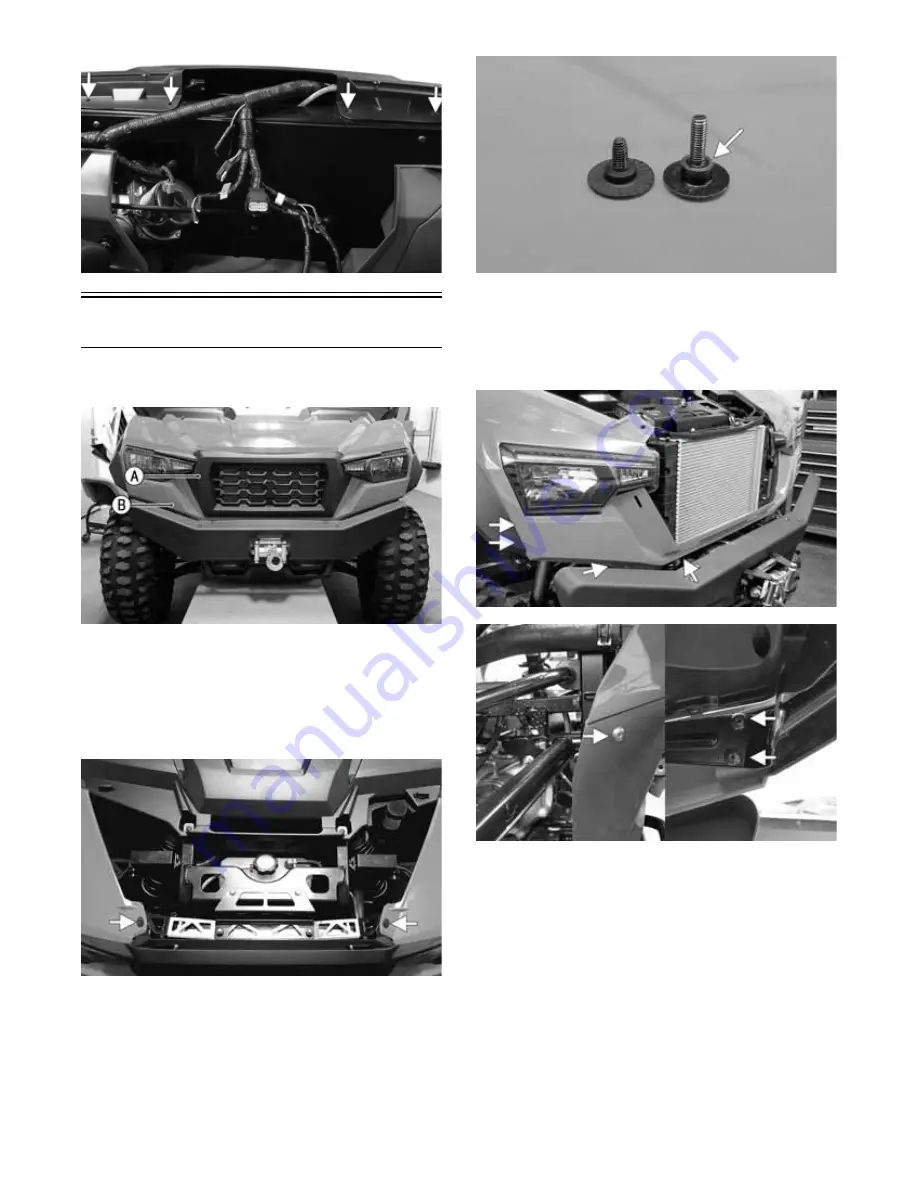
37
MOD252
Front Fascia/Grille
Grille (A)
Fascia (B)
MOD013A
REMOVING
1. Remove the hood; then the two T30 cap screws
securing the grille and front fenders.
NOTE: Take note of the higher shoulder and longer
thread for fastening through multiple panels.
MOD044C
MOD133A
2. There are four cap screws per side that secure the
bottom of the front fascia.
3. Remove the three T20 cap screws securing the outer
front of the fascia; then remove them from the oppo-
site side.
MOD134A
MOD140A
4. Remove the two T30 shouldered cap screws from the
center of the front fascia; then remove the front fas-
cia.
Summary of Contents for 800SX
Page 1: ...800SX SERVICE MANUAL p n 2263 005 9 20...
Page 2: ......
Page 189: ...187 NOTES...
Page 190: ...188 NOTES...
Page 191: ......
Page 192: ......