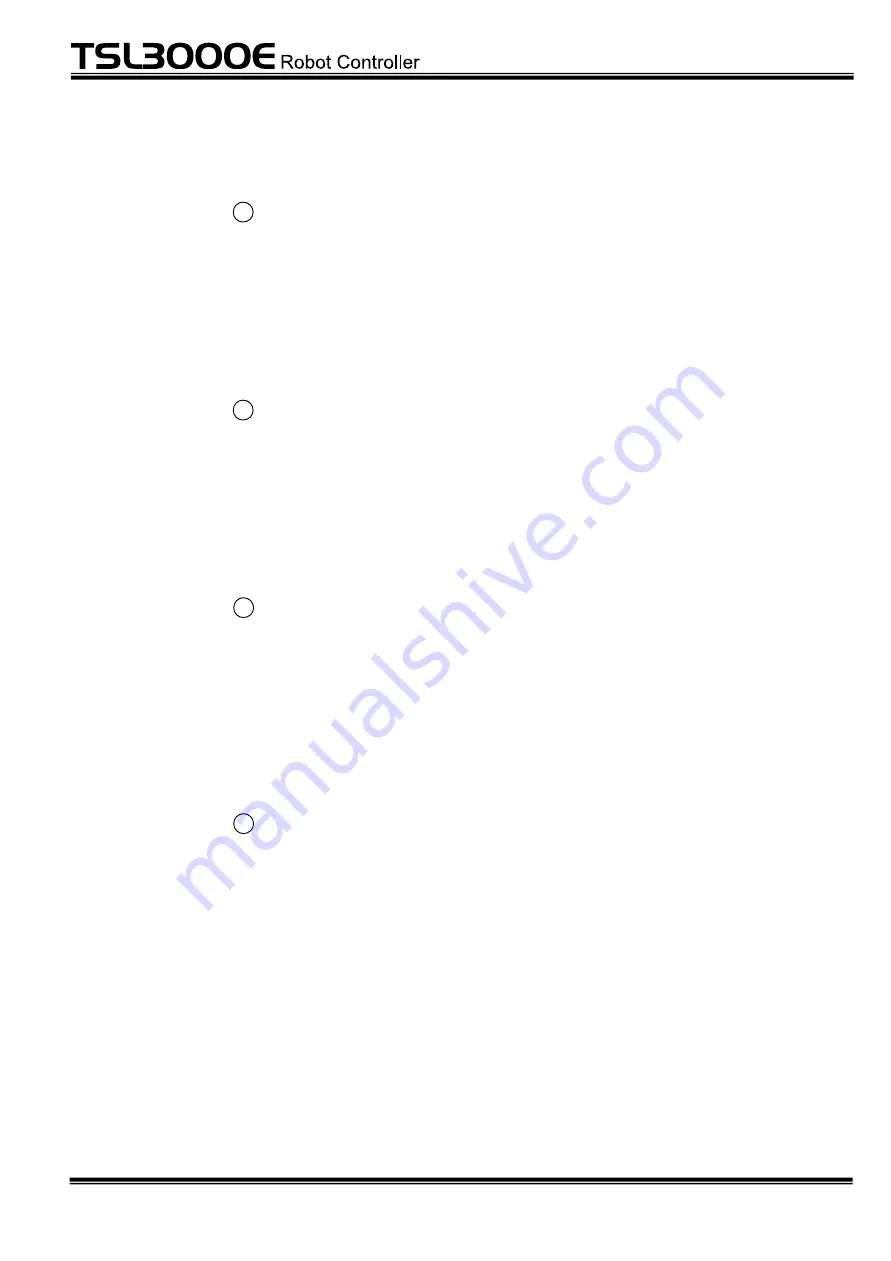
– 14 –
INTERFACE MANUAL
STE 85457
1.14 Fieldbus Cable "Fieldbus"
Fig. 1.1
–
11
(option)
This supports connection with fieldbus devices, which is available as an option
function in the TSL3000E/TSL3100E robot controller. PROFIBUS, DeviceNet, or
CC-Link can be selected as the type of fieldbus for the slave module. "FieldBUS" is
located in the top section of the front panel.
1.15 CONV Cable "CONV"
Fig. 1.1
–
13
(option with connector)
This is used to use the conveyor synchronization function. Use the encoder provided
with A- and B-phase signals having 90° phase and the output circuit having RS-422
differential output (line driver). The signal from the incremental encoder and the
input signal from the conveyor synchronization start trigger switch are required.
1.16 TRIG Cable "TRIG"
Fig. 1.1
–
14
(option with connector)
This cable comes standard with eight (8) trigger input functions. This is used for data
latch function, conveyor synchronization function, etc. The D-sub15-pin connector
located on the top of the front panel is "TRIG." Connector "TRIG" is used.
1.17 Extension I/O Signal Cable
1.17.1 Extension Input Signal Cable "INPUT (TR)"
Fig. 7.3
–
14
(option)
This is an interface which inputs an external signal from the external equipment to
remote I/O module TR48DIOCN/TR48DIOC. Like the external input signal cable,
the extension input signal cable is provided with twenty-eight (28) digital input
signals that can be programmed at the user's discretion, using the SCOL language
or PLC function. The extension input signal, together with the external output
signal or extension output signal, allows the robot controller to work in concert with
the external equipment. Connector "INPUT (TR)" is used.
Note:
To discriminate from the INPUT cable connector of the
TSL3000E/TSL3100E robot controller, the extension input signal cable
connector is referred to as "INPUT (TR)" in this manual.
Summary of Contents for TSL3000E
Page 128: ... z INTERFACE MANUAL STE 85457 ...