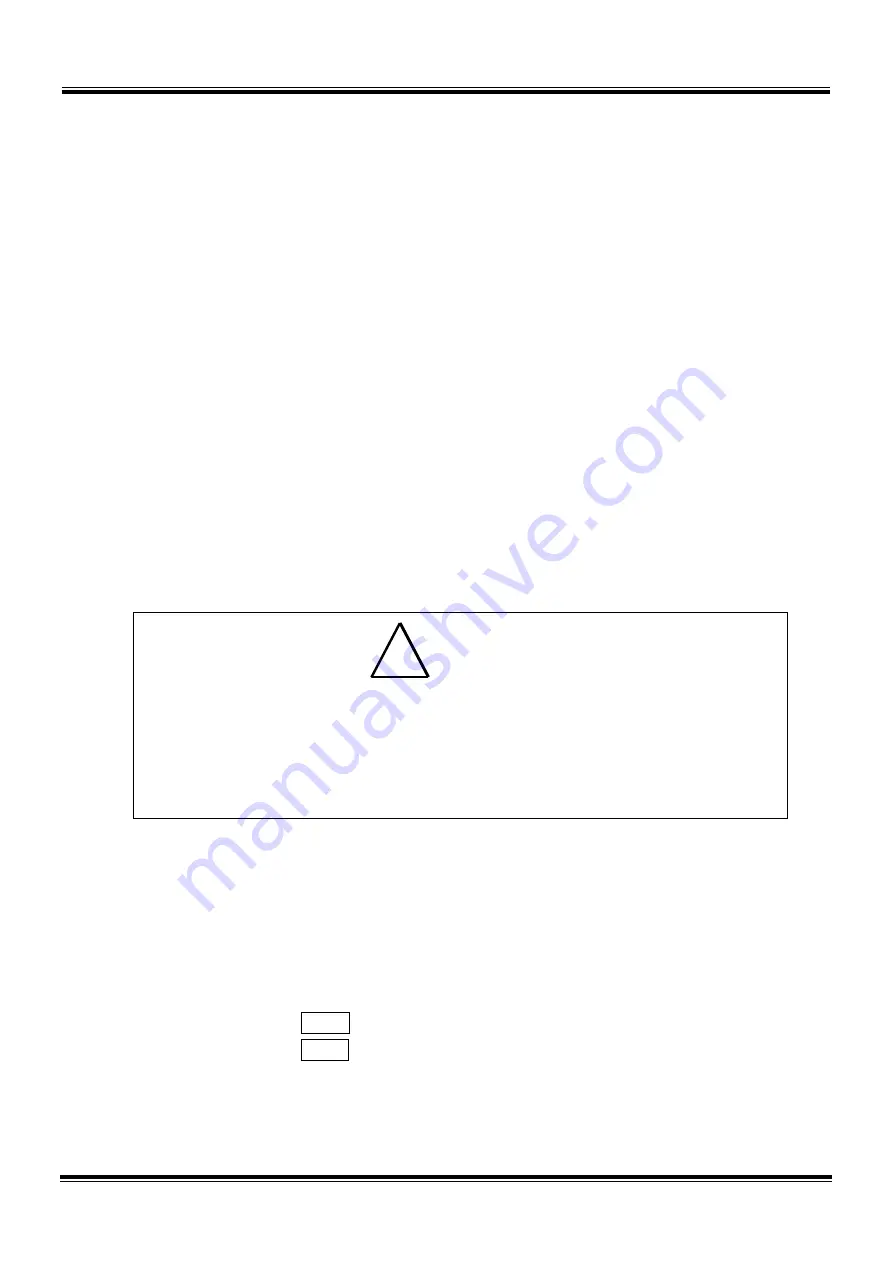
DUST- & DRIP-PROOF TYPE SPECIFICATIONS MANUAL
4. Tool
Interface
Mounting of a tool and tool signals are the same as in the standard robot.
For details, see the TH850A/TH1050A Installation and Transportation Manual provided
separately.
4.1 Tool
Wiring
Five (5) input signals are provided for sensors, etc. and four (4) control signals for
solenoid valves, etc. A power supply signal of DC24 V is also provided. They are
connected to the controller. The cables are connected to the connectors on the upper
side of the arm 2. The user should provide the following connector to connect the
cables.
Cannon connector (dust- and drip-proof type):
Type: JL04–2E–20–29P–R (Maker: JAE)
Adaptive cable: Conductive cross section area: 0.2 mm
2
~ 0.5 mm
2
Each connector and cable are connected by soldering.
!
DANGER
• Be sure to use the designated cables. Otherwise, fires or faults may be
caused.
• When connecting the connector and cables, make sure not to mistake the
terminal arrangement.
• After making the connection, use a tester, etc., to confirm the connection.
When controlling the robot from the sequencer (i.e., programmable ladder controller:
PLC), etc. installed separately, remove the motor cover from the base section, remove
connectors JOES and JOFS on the rear side, then connect the cables running from the
PLC, etc. through the cable clamp provided on the motor cover. (See Fig. 4.1.) For
ahead of the JOES and JOFS connectors, the user should prepare the following plug
connectors and connect the cables. The current is 1 A or less per cable.
Type of connector: JOES
SMP–07V–BC (Maker: J.S.T. Mfg.)
JOFS
SMP–06V–BC (Maker: J.S.T. Mfg.)
Type of contact:
BHF–001T–0.8SS (Maker: J.S.T. Mfg.)
Adaptive cable:
Conductive cross section area: 0.2 mm
2
~ 0.3 mm
2
STE 80765
– 29 –