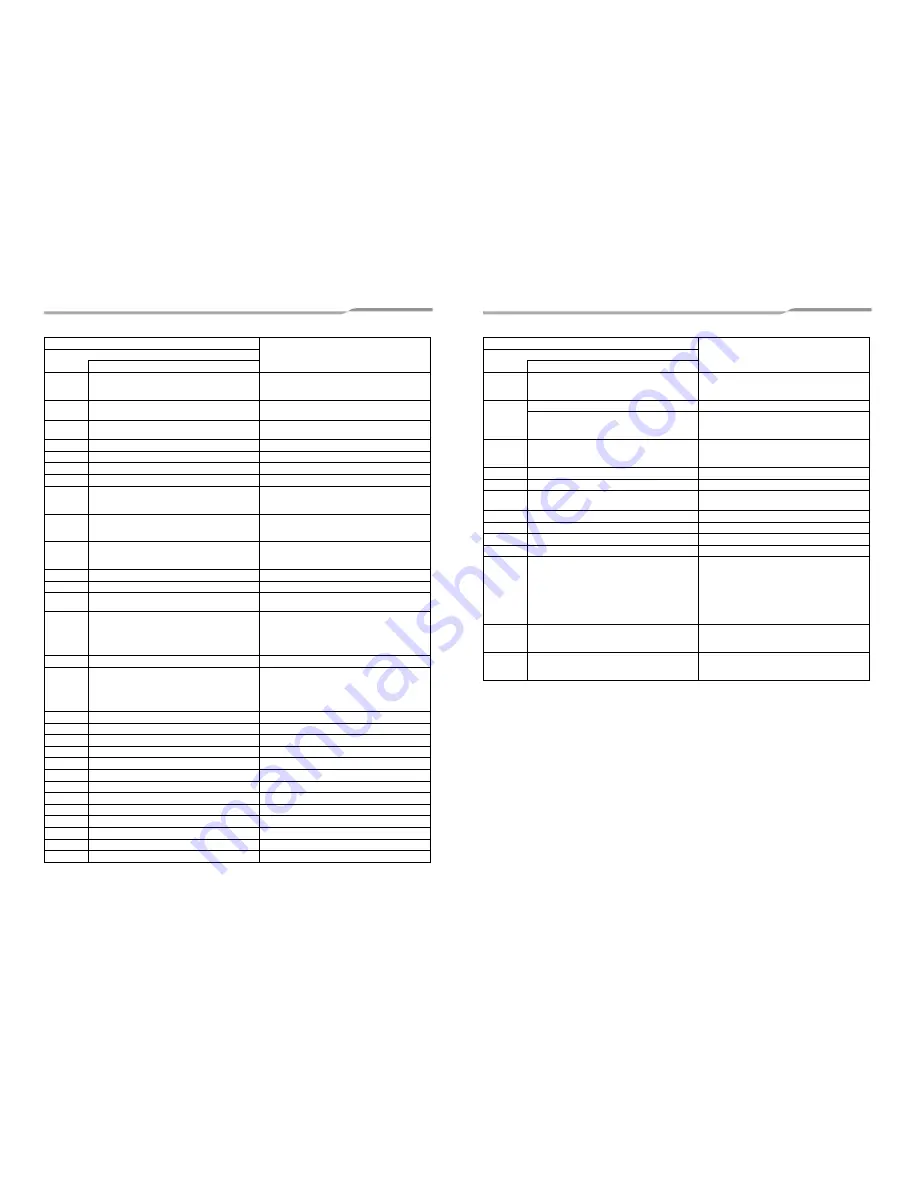
– 33 –
F13
01: Compressor 1
02: Compressor 2
03: Compressor 3
TH (Heat sink) sensor error
F15
—
Outdoor temp. sensor miswiring
Outdoor pressure sensor miswiring (TE1, TL)
F16
—
Outdoor temp. sensor miswiring
Outdoor pressure sensor miswiring (Pd, Ps)
F22
—
TD3 sensor error
F23
—
Ps sensor error
F24
—
Pd sensor error
F31
—
Outdoor EEPROM error
H01
01: Compressor 1
02: Compressor 2
03: Compressor 3
Compressor breaking down
H02
01: Compressor 1
02: Compressor 2
03: Compressor 3
Compressor error (Locked)
H03
01: Compressor 1
02: Compressor 2
03: Compressor 3
Current detection circuit error
H05
—
TD1 sensor miswiring
H06
—
Low pressure protective operation
H07
Detected outdoor unit number
Oil level down detection
(Indicated only on the header outdoor unit)
H08
01: TK1 sensor error
02: TK2 sensor error
03: TK3 sensor error
04: TK4 sensor error
05: TK5 sensor error
Temperature sensor error for oil level
H15
—
TD2 sensor miswiring
H16
01: TK1 oil circuit error
02: TK2 oil circuit error
03: TK3 oil circuit error
04: TK4 oil circuit error
05: TK5 oil circuit error
Oil level detector circuit error
H25
—
TD3 sensor miswiring
L02
—
Mismatch of the indoor unit and outdoor unit model
L04
—
Outdoor system address duplication
L06
Number of prior indoor units
Duplication of indoor units with priority
L08
—
Indoor unit group / address unset
L10
—
Outdoor unit capacity unset.
L17
—
Mismatch of the outdoor unit model
L18
Detected indoor unit address
Flow selector unit error
L28
—
Outdoor connected quantity over
L29
IPDU number information
(*1)
IPDU quantity error
L30
Detected indoor unit address
External interlock of indoor unit
L31
—
Other compressor errors
P03
—
Discharge temperature TD1 error
Check code
Check code name
Indication on 7-segment display on the outdoor unit
Auxiliary code
*1
PDU number information
01:Compressor 1
02:Compressor 2
03:Compressors 1 and 2
04:Compressor 3
05:Compressors 1 and 3
06:Compressors 2 and 3
07:Compressors 1, 2 and 3
08:Fan
09:Compressor 1 and fan
0A:Compressor 2 and fan
0B:Compressors 1, 2 and fan
0C:Compressor 3 and fan
0D:Compressors 1, 3 and fan
0E:Compressors 2, 3 and fan
0F:Compressors 1, 2, 3, and fan
P04
01: Compressor 1
02: Compressor 2
03: Compressor 3
High-pressure SW system operation
P05
00:
Phase missing / power failure detection
01: Compressor 1
02: Compressor 2
03: Compressor 3
Inverter DC voltage error (on compressor)
P07
01: Compressor 1
02: Compressor 2
03: Compressor 3
Heat sink overheat error
P10
Detected indoor unit address
Indoor overflow error
P13
—
Outdoor unit flow back error detected
P15
01: TS condition
02: TD condition
Gas leak detection
P17
—
Discharge temperature TD2 error
P18
—
Discharge temperature TD3 error
P19
Detected outdoor unit number
4-way valve inverse error
P20
—
High-pressure protective operation
P22
0 *: IGBT circuit
1 *: Position detection circuit error
3 *: Motor lock error
4 *: Motor current detected
C *: TH sensor temperature error
D *: TH sensor error
E *: Inverter DC voltage error
(outdoor unit’s fan)
Outdoor fan IPDU error
(NOTE)
Ignore 0-F appearing in the position of “*”.
P26
01: Compressor 1
02: Compressor 2
03: Compressor 3
G-TR short protection error
P29
01: Compressor 1
02: Compressor 2
03: Compressor 3
Compressor position detecting circuit error
Check code
Check code name
Indication on 7-segment display on the outdoor unit
Auxiliary code
65-EN
66-EN
Summary of Contents for MMY-MAP0804FT8-E
Page 37: ...EH99889397 ...