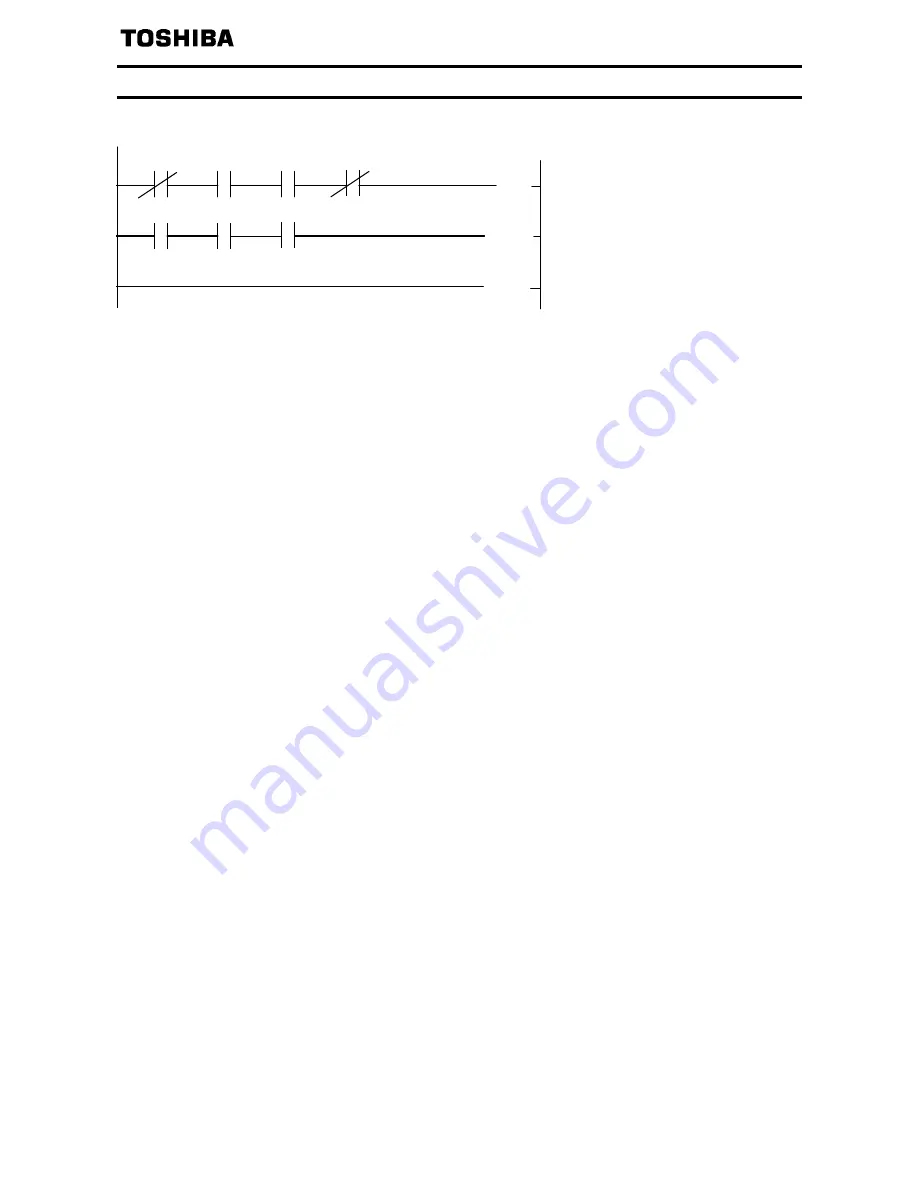
E658130
- 45 -
6.9.
Program example for resetting the inverter at inverter error
Example 9 shows a ladder logic to reset the station 2 inverter.
The above inverter reset using RY3A may be made only when an inverter error occurs.
Also, inverter reset can be made independently of the operation mode.
X0
X0F
X1
SW80.1
M
X103
X2
[ M0
[Y103A]
[ END
Check the ready of the station 2
Turn on the error reset request flag
(RY3A). Then, turn off the error
reset
request flag (RY3A) when the error
Example