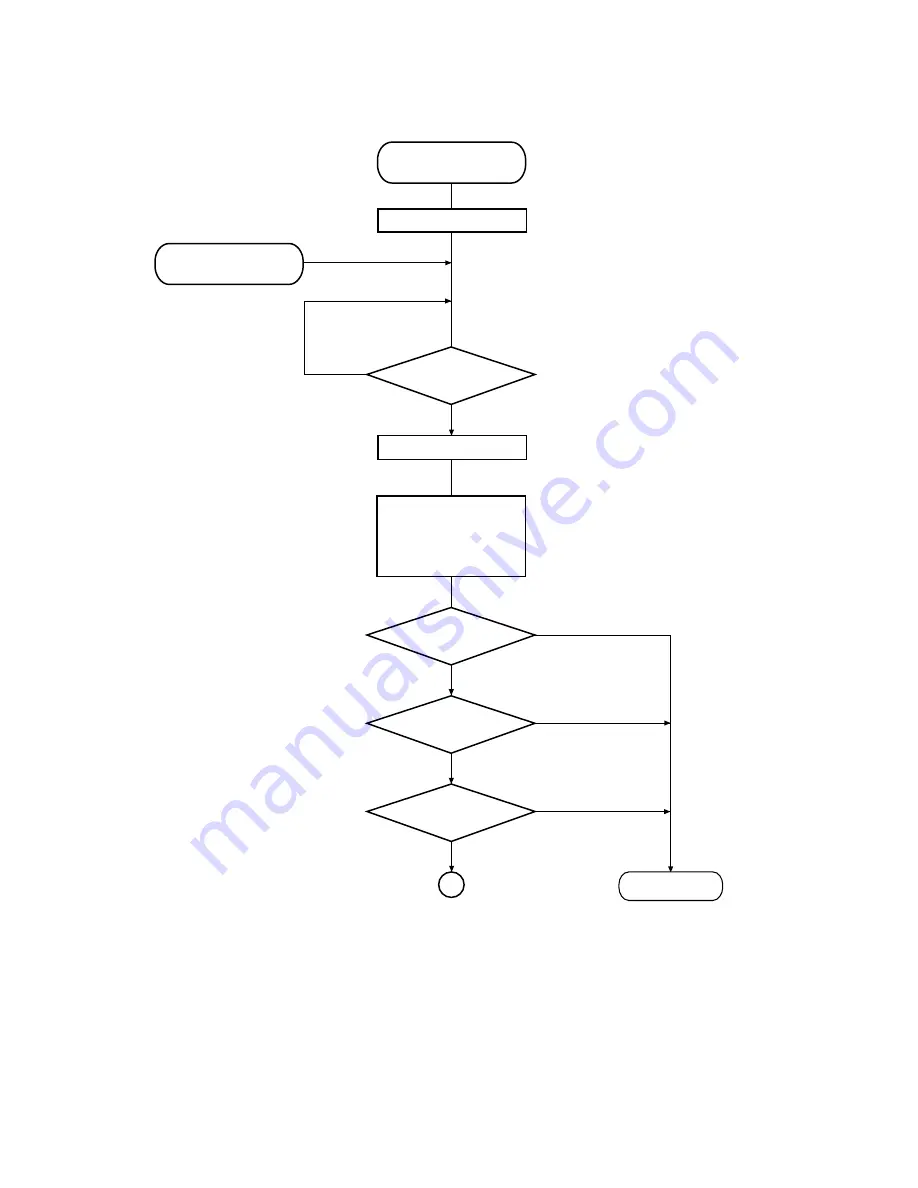
6570/5570 COPIER OPERATION
4 - 10
Mar. 1999 © TOSHIBA TEC
4.4
Flow Charts
4.4.1
Power ON to ready
YES
YES
NO
Start of initialization
A
Restart
Main switch ON
Cover open?
• SCN-MTR
• DCM-MTR
• STOP-MTR
• GUIDE-MTR
Heater lamp ON
NO
P-STP-SW
ON?
NO
NO
Paper jam
YES
YES
EXIT-SW
ON?
ADU-JAM-SW
ON?
DC power ON
“E03”
Summary of Contents for 4580
Page 1: ...SERVICE MANUAL DIGITAL PLAIN PAPER COPIER 8070 6570 5570 4580 ...
Page 231: ...6570 5570 DEVELOPER UNIT 12 28 Mar 1999 TOSHIBA TEC 3 Draw out the toner filter ...
Page 252: ...8070 6570 5570 4580 FUSER UNIT 14 6A Mar 1999 TOSHIBA TEC ...
Page 369: ...8070 6570 5570 4580 ADF 16 78 Mar 2000 TOSHIBA TEC 16 13 PC Board 1 PWA F LGC 794 ...
Page 370: ...Mar 2000 TOSHIBA TEC 16 79 8070 6570 5570 4580 ADF 2 PWA F SEN 794 ...
Page 374: ...Mar 1999 TOSHIBA TEC 18 1 6570 5570 PC BOARD 18 PC BOARD 1 PWA F SYS 300 ...
Page 375: ...6570 5570 PC BOARD 18 2 Mar 1999 TOSHIBA TEC 2 PWA F MTB 300 ...
Page 376: ...Mar 1999 TOSHIBA TEC 18 3 6570 5570 PC BOARD 3 PWA F LGC 300 ...
Page 377: ...6570 5570 PC BOARD 18 4 Mar 1999 TOSHIBA TEC 5 PWA F MOT 300 4 PWA F ADU 300 ...
Page 378: ...Mar 1999 TOSHIBA TEC 18 5 6570 5570 PC BOARD 6 PWA F SLG 300 7 PWA F SDV 300 ...
Page 379: ...6570 5570 PC BOARD 18 6 Mar 1999 TOSHIBA TEC 8 PWA F PLG 300 ...