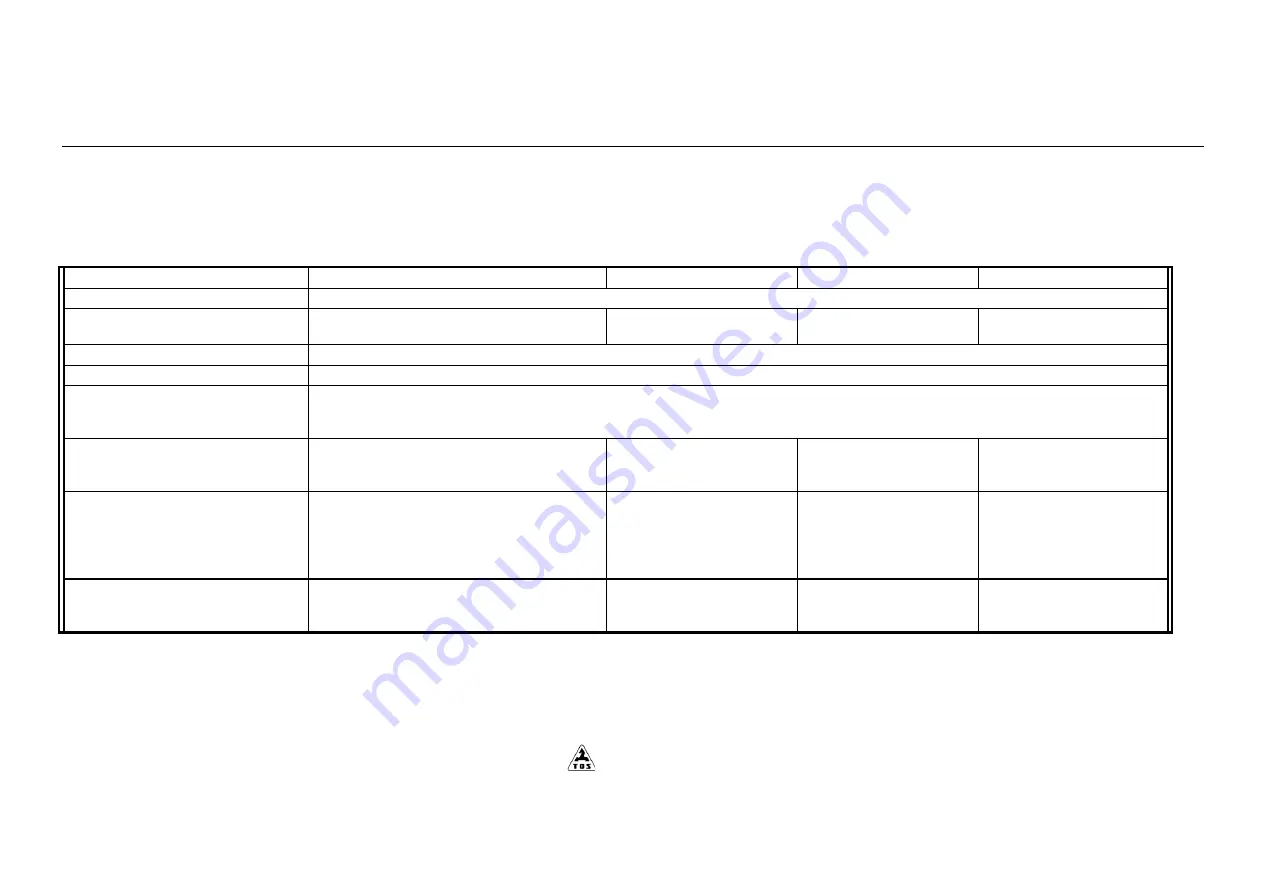
SUA 125 NUMERIC
34200003
TOS a.s. 02/2011
10
3. Heat risks:
No heat risks are occurred.
4. Noise risk with consequent:
Noise metering record.
4.1. Reduction of hearing
Motion of power and geared parts. Cutting
process. Noise resonance of machined material.
In course of machining.
In lathe proximity.
5. Vibration risks:
Vibration metering record.
6. Radiation risks:
Unrelated.
7. Risks caused by machined
materials and liquids used in
machining process:
7.1. Contact or inhalation of harmful
vapours of liquid, gas, mist, smoke and
dust.
Conditions in lathe proximity caused by
particles of machined material, drops of cutting
lubricant or arised mist
In course of machining
In lathe proximity.
7.2. Fire or explosion risk
Flammable machined material.
Mist making
Loss of cutting lubricant supply to the point of
machining. In line breakdown to the power
electric hydraulic or lubricant systems
In course of machining
In lathe proximity.
7.3. Biological and microbiological
risks
Contact with hydraulic or cutting lubricant
either in liquid state or in mist which consists of
chips,bacteria e.t.c....
In course of the working
process control and in
maintenance
In lathe proximity.
Summary of Contents for SUA 125 NUMERIC
Page 39: ...SUA 125 NUMERIC 34200003 TOS a s 02 2011 39...
Page 41: ...SUA 125 NUMERIC 34200003 TOS a s 02 2011 41...
Page 43: ...SUA 125 NUMERIC 34200003 TOS a s 02 2011 43 5 2 3 Brake Fig 5 2 Fig 5 2 6...
Page 46: ...SUA 125 NUMERIC 34200003 TOS a s 02 2011 46...
Page 48: ...SUA 125 NUMERIC 34200003 TOS a s 02 2011 48 5 2 6 Work spindle Fig 5 4...
Page 57: ...SUA 125 NUMERIC 34200003 TOS a s 02 2011 57...
Page 63: ...SUA 125 NUMERIC 34200003 TOS a s 02 2011 63 Hydraulic chart...
Page 64: ...SUA 125 NUMERIC 34200003 TOS a s 02 2011 64...
Page 68: ...SUA 125 NUMERIC 34200003 TOS a s 02 2011 68 Fig 5 8...
Page 70: ...SUA 125 NUMERIC 34200003 TOS a s 02 2011 70...
Page 75: ...SUA 125 NUMERIC 34200003 TOS a s 02 2011 75...
Page 93: ...SUA 125 NUMERIC 34200003 TOS a s 02 2011 93 Fig A transport locking...
Page 95: ...SUA 125 NUMERIC 34200003 TOS a s 02 2011 95...
Page 109: ...SUA 125 NUMERIC 34200003 TOS a s 02 2011 109 Fig B Working path length is 650 mm...
Page 110: ...SUA 125 NUMERIC 34200003 TOS a s 02 2011 110 Longitudinal stops Fig C...