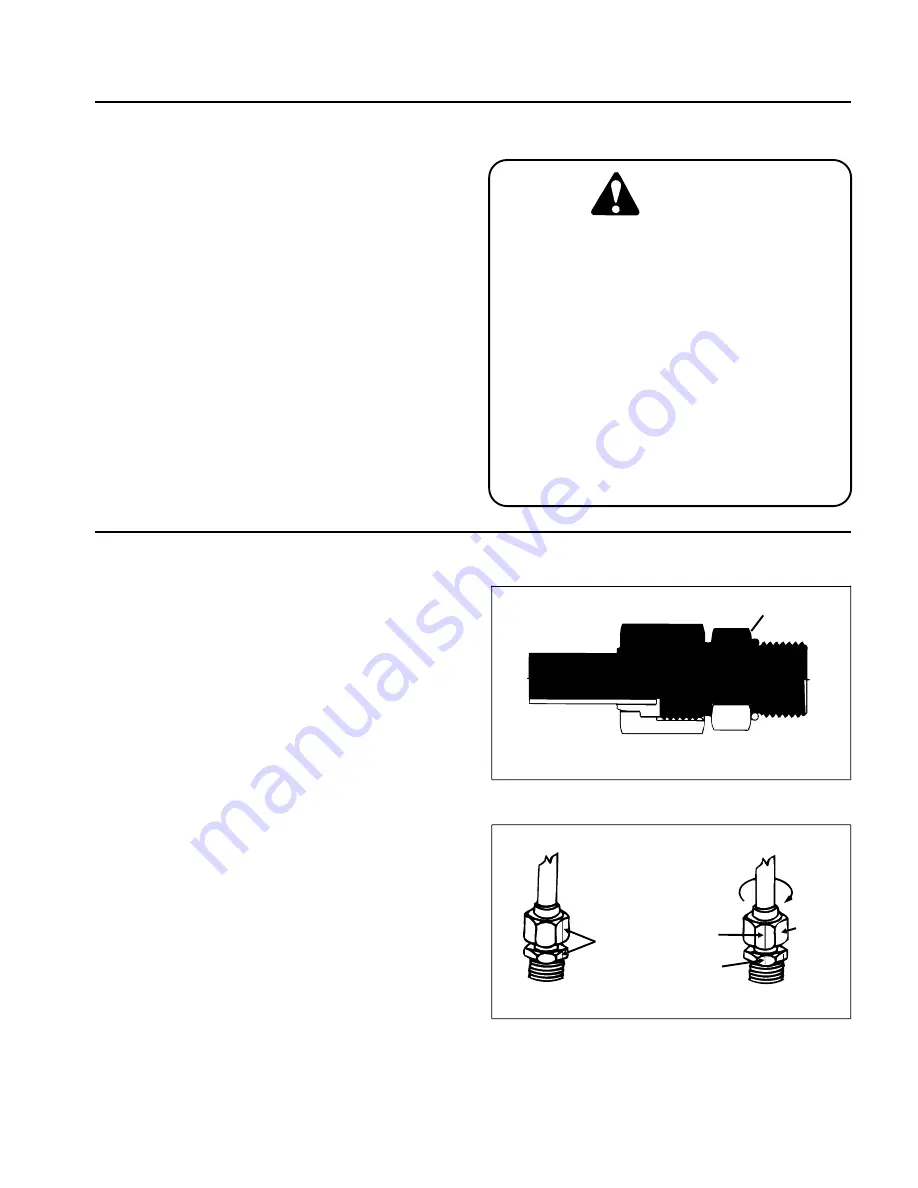
paper or
with this
Figure 2
Body
Sleeve
Seal
Final
General Information
Hydraulic Hoses
spect the hoses frequently for signs of deterioration or
damage.
gine and opening the bypass valve.
Keep body and hands away from pin hole
der high pressure. Use
cardboard,
escaping under pressure can have sufficient
hours by a doctor familiar
injury or gangrene may result.
Hydraulic Fitting Installation
O-Ring Face Seal (Fig. 2, 3)
1. Make sure both threads and sealing surfaces are free
of burrs, nicks, scratches, or any foreign material.
2. Make sure the O-ring is installed and properly seated
replaced any time the connection is opened.
3. Lubricate the O-ring with a light coating of oil.
been tightened.
Size
F.F.F.T.
4 (1/4 in. nominal hose or tubing)
.75
r
.25
6 (3/8 in.)
r
.25
8 (1/2 in.)
.75
r
.25
10 (5/8 in.)
r
.25
12 (3/4 in.)
r
.25
Nut
and Body
Position
Extend Line
Initial
Position
CAUTION
Hydraulic hoses are subject to extreme conditions such
as, pressure differentials during operation and exposure
to weather, sun, chemicals, very warm storage condi
tions or mishandling during operation or maintenance.
These conditions can cause damage or premature de
terioration. Some hoses, such as reel motor hoses, are
more susceptible to these conditions than others. In
When replacing a hydraulic hose, be sure that the hose
is straight (not twisted) before tightening the fittings. This
can be done by observing the imprint on the hose. Use
two wrenches; one to hold the hose straight and one to
tighten the hose swivel nut onto the fitting.
Before disconnecting or performing any work
on the hydraulic system, all pressure in the
system must be relieved by stopping the en-
leaks or nozzles that eject hydraulic fluid un-
not hands, to search for leaks. Hydraulic fluid
force to penetrate the skin and do serious
damage. If fluid is injected into the skin, it
must be surgically removed within a few
type of
in the groove. It is recommended that the O-ring be
4. Put the tube and nut squarely into position on the face
seal end of the fitting and tighten the nut until finger tight.
5. Mark the nut and fitting body. Hold the body with a
wrench. Use another wrench to tighten the nut to the
correct flats from finger tight (F.F.F.T.). The markings on
the nut and fitting body will verify that the connection has
.75
1.00
.75
Mark Nut
Finger
Tight
After
Proper
Tightening
16 (1 in.)
.75
r
.25
Figure 3
Hydroject 3010
Page 4 - 3
General Information
Summary of Contents for HydroJect 3010
Page 2: ...Hydroject 3010...
Page 4: ...Hydroject 3000 4000...
Page 10: ...Equivalents and Conversions Product Records and Maintenance Page 2 2 Hydroject 3010...
Page 44: ...Repairs Page 4 26 Hydroject 3010...
Page 72: ...Repairs Page 5 28 Hydroject 3010...
Page 102: ...This page is intentionally blank Repairs Page 6 28 HydroJect 3010...
Page 109: ...IRXU ORFDWLRQV 7RUTXH WR IW OE LJXUH GURMHFW 3DJH 5HSDLUV...
Page 118: ...This page is intentionally blank Electrical Diagrams Page 8 2 Hydroject 3010...
Page 119: ...Page 8 3 Electrical Schematic Hydroject 3010...
Page 120: ...Hydroject 3010 Main Harness Page 8 4...
Page 121: ...Page 8 5 Main Wiring Diagram Hydroject 3010...
Page 122: ...Hydroject 3010 Control Panel Harness Page 8 6...
Page 123: ...Hydroject 3010 Tiller Wire Harness and Diagram Page 8 7...
Page 124: ......