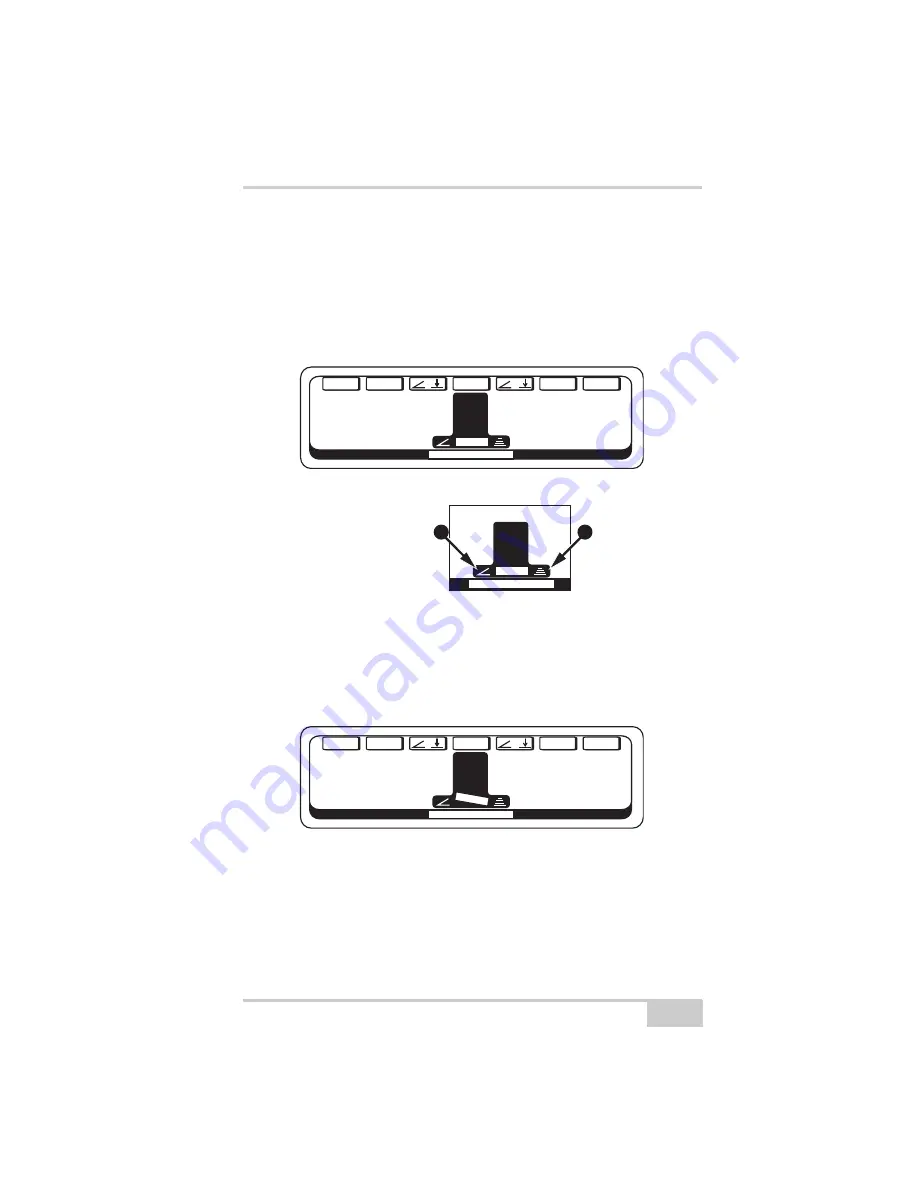
Control Box
P/N 7010-0344
2-3
The LCD (Liquid Crystal Display)
The LCD allows the operator to view text and graphic symbols that
represent elevation or slope settings that System Five is currently
maintaining for the left and right sides of the motorgrader.
• System Five in Control Mode during operation.
Figure 2-2.
Figure 2-3.
• 2.0% cross slope has been selected for the left side. The blade
symbol shows that the 2.0% slope is going down.
• The Sonic Tracker symbol indicates that Sonic Control has been
selected for the right side.
Figure 2-4.
0.0
F
T
CONTROL MODE
GAIN
SET
/
+
/
—
/
TRIM
MENU
0.0%
+
LEFT
RIGHT
A
B
CONTROL MODE
A = Slope Control
B = Sonic Control
0.0
F
T
CONTROL MODE
GAINS
SET
/
+
/
—
/
TRIM
MENU
2.0%
+
Summary of Contents for Motorgrader
Page 1: ...OTORGRADER 3YSTEM IVE4 ONTROL OX PERATORlS ANUAL...
Page 2: ......
Page 4: ...ECO 2955...
Page 8: ...Table of Contents Motorgrader System Five Operator s Manual Notes iv...
Page 22: ...System Overview Motorgrader System Five Operator s Manual Notes 1 12...
Page 58: ...Operation Motorgrader System Five Operator s Manual Notes 2 36...
Page 168: ...Safety Information Motorgrader System Five Operator s Manual Notes A 4...
Page 171: ......