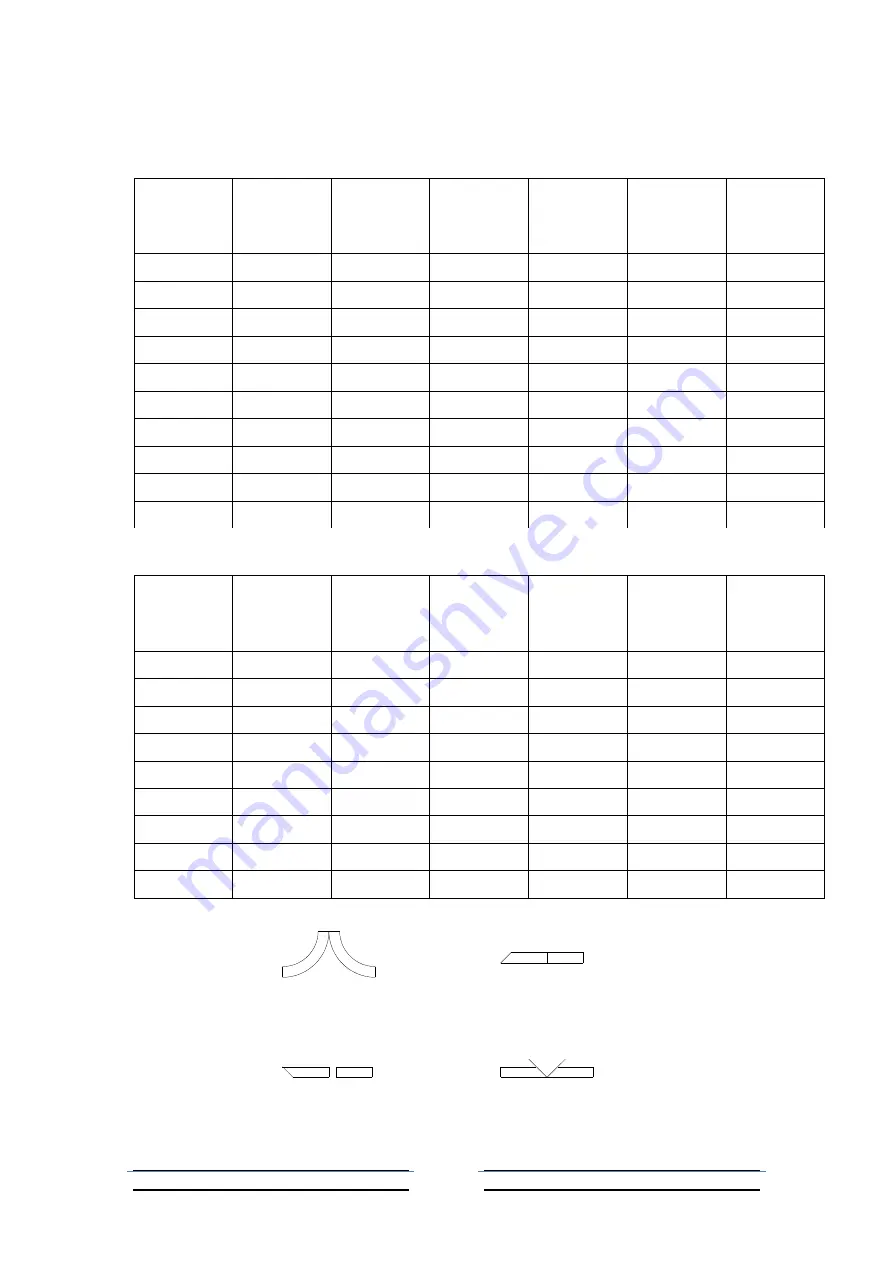
14
/
16
14
4. STAINLESS STEEL
(
SUS304
)
WELDING PARAMETER:
Steel
thickness
Tungsten
diameter
Wire
diameter
Welding
current
Argon flux
Clearance
size
Clearance
form
(mm)
(mm)
(mm)
(A)
(L/min)
(mm)
0.6
1.0
~
1.6
0
~
1.0
15
~
30
4
~
5
1
a
、
b
1.0
1.0
~
1.6
0
~
1.6
25
~
30
4
~
7
1
a
、
b
1.5
1.0
~
1.6
0
~
1.6
50
~
70
6
~
9
1
b
2.5
1.6
~
2.4
1.6
~
2.4
65
~
95
6
~
9
1
b
3.0
1.6
~
2.4
1.6
~
2.4
90
~
120
7
~
10
1
~
2
b
、
c
4.0
2.4
1.6
~
2.4
110
~
150
10
~
15
2
~
3
c
、
d
5.0
2.4
~
3.2
2.4
~
3.2
120
~
180
10
~
15
2
~
3
c
、
d
6.0
2.4
~
3.2
2.4
~
3.2
150
~
200
10
~
15
3
~
4
c
、
d
8.0
3.2
~
4.0
3.2
~
4.0
160
~
220
12
~
18
4
~
5
d
12.0
3.2
~
4.0
3.2
~
4.0
180
~
240
12
~
18
6
~
8
d
5. ALUMINUM WELDING PARAMETER
Aluminum
thickness
Tungsten
diameter
Wire
diameter
Welding
current
Argon flux
Clearance
size
Clearance
form
(mm)
(mm)
(mm)
(A)
(L/min)
(mm)
0.6
1.0
~
1.6
0
~
1.0
25
~
40
4
~
5
1
a
、
b
1.0
1.0
~
1.6
0
~
1.6
40
~
60
4
~
7
1
a
、
b
1.5
1.0
~
1.6
0
~
1.6
60
~
90
6
~
9
1
b
2.5
1.6
~
2.4
1.6
~
2.4
80
~
120
6
~
9
1
b
3.0
1.6
~
2.4
1.6
~
2.4
100
~
160
7
~
10
1
~
2
b
、
c
4.0
2.4
1.6
~
2.4
130
~
200
10
~
15
2
~
3
c
、
d
5.0
2.4
~
3.2
2.4
~
3.2
150
~
250
10
~
15
2
~
3
c
、
d
6.0
2.4
~
3.2
2.4
~
3.2
200
~
280
10
~
15
3
~
4
c
、
d
8.0
3.2
~
4.0
3.2
~
4.0
200
~
300
12
~
18
4
~
5
d
(c)
(d)
(a)
(b)
Summary of Contents for 597076
Page 1: ...1 16 1 ...