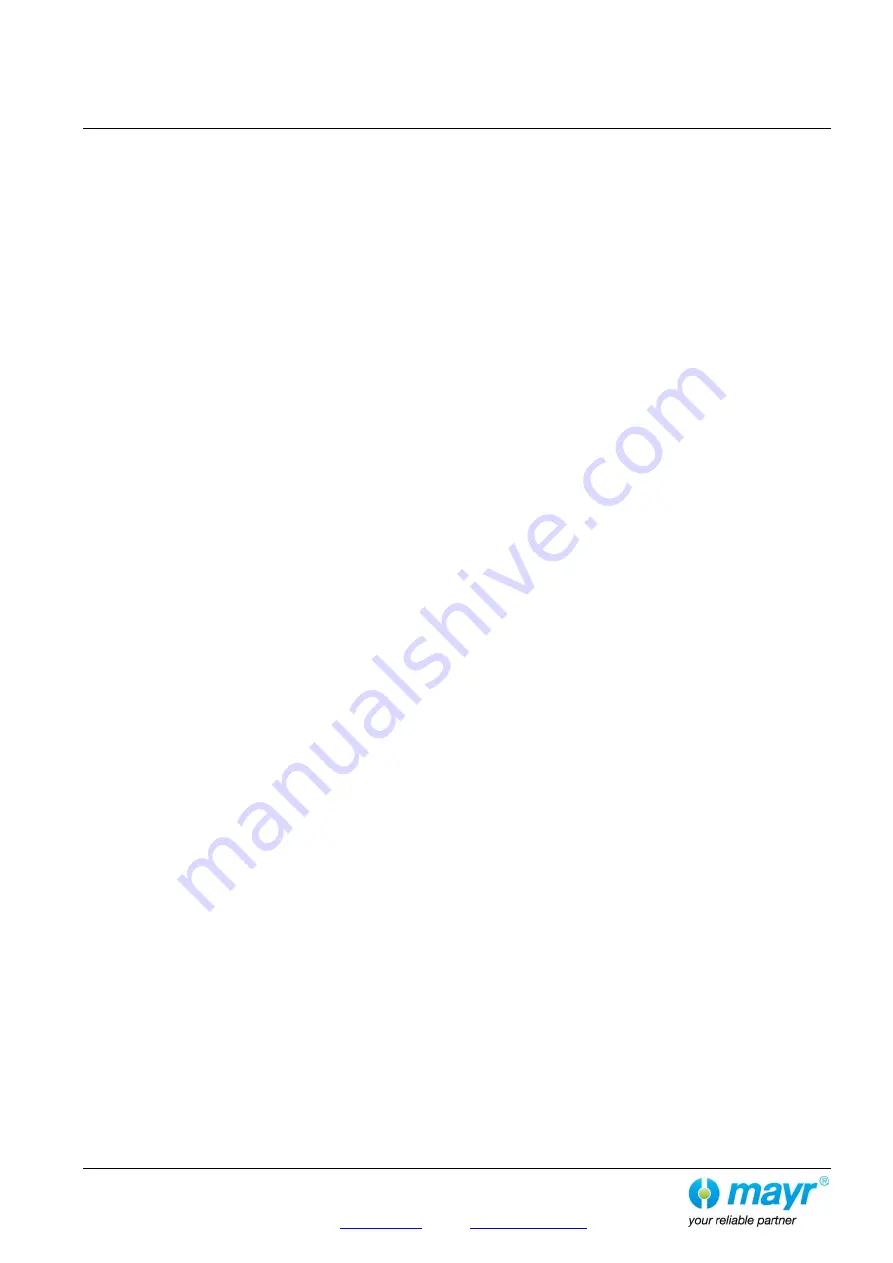
Installation and Operational Instructions for
ROBA-stop
®
-Z Type 892.101.0
Size 125
(E073 01 046 000 4 EN)
18/05/2022 TK/HW/SU
Chr. Mayr GmbH + Co. KG
Eichenstraße 1, D-87665 Mauerstetten, Germany
Phone: +49 8341 804-0, Fax: +49 8341 804-421
Page 9 of 16
www.mayr.com
, E-Mail:
Application
ROBA-stop
®
-Z brake for use as a holding brake with
occasional EMERGENCY STOP braking actions (max. 10
per day).
The max. permitted speed and friction work (see Technical
Data) must be observed.
Design
The ROBA-stop
®
-Z brake is a spring applied, electromagnetically
releasing dual circuit safety brake, which applies a defined
braking effect after the voltage is switched off or after a voltage
failure.
This brake is combined with a positive-locking, flexible coupling
(ROBA
®
-ES coupling) for connecting two shafts whilst
compensating for shaft misalignments.
The ROBA
®
-ES coupling compensates for axial, radial and
angular shaft misalignments.
Function
The ROBA-stop
®
-Z brake is a spring applied, electromagnetic
safety brake.
Spring applied function (brake):
In de-energized condition, thrust springs (8) press against the
armature disk (14). Rotor 2 (Item 6) is held between the armature
disk (14) and the brake plate (15), rotor 1 (Item 5) is held between
the brake body (2) and the machine wall via frictional locking.
The braking torque is introduced into the drive line via the
toothing of the rotors (5 and 6) and the hub (1).
Electromagnetic function (release):
Due to the magnetic force of the coil in the brake body (2), the
armature disk (14) is attracted against the spring pressure (8) to
the brake body (2). The brake is released and the brake rotors (5
and 6) with the hub (1) can rotate freely.
Safety brakes:
The ROBA-stop
®
-Z brake brakes reliably
and safely in the event of a power switch-off, a power failure or an
EMERGENCY STOP.
Scope of Delivery / State of Delivery
The ROBA-stop
®
-Z brake is pre-assembled.
On brake article number 8253118, the hub (12) is not included in
the standard scope of delivery.
Brake article number 8292346 is designed without hand release
(18).
The release monitoring (11) device is installed and set
manufacturer-side.
The brakes are set manufacturer-side to the braking torque
stipulated on order.
Please check the scope of delivery according to the Parts List as
well as the state of delivery immediately after receiving the goods.
mayr
®
will take no responsibility for belated complaints.
Please report transport damage immediately to the deliverer.
Please report incomplete delivery and obvious defects
immediately to the manufacturer.
Installation Conditions
The eccentricity of the shaft end in relation to the mounting
pitch circle must not exceed 0.2 mm.
The positional tolerance of the threads for the cap screws (3)
must not exceed 0.2 mm.
The axial run-out deviation of the screw-on surface to the
shaft must not exceed the permitted axial run-out tolerance of
0.05 mm
acc. DIN 42955 R.
The reference diameter is the pitch circle diameter for
securement of the brakes.
Larger deviations can lead to a drop in torque, to continuous
grinding on the rotors and to overheating.
The fit tolerance of the shaft must be selected so that the hub
toothing (1) is not widened. Widening of the toothing leads to
the rotors (5 and 6) jamming on the hub (1) and therefore to
brake malfunctions.
Recommended fit tolerance for the shaft: k6
The max. permitted joining temperature of 150 °C must not be
exceeded.
The O-rings (1.1) on the hub (1) must be lightly greased.
The rotors (5 and 6) and the brake surfaces must be oil and
grease-free.
A suitable counter friction surface (steel or cast iron) must be
used. Sharp-edged interruptions on the friction surfaces must
be avoided. Recommended surface quality in the area of the
friction surface Ra = 0.8 – 1.6 µm. The mounting surface must
be turned. The surface must be bare or FE-phosphated (layer
thickness approx. 0.5 µm) without oil.
If corrosion protection is applied, the device must be
inspected for possible effects on the braking torque.
In particular customer-side mounting surfaces made of
grey cast iron are to be rubbed down additionally with
sandpaper (grain
60 to 100).
The toothings of the hub (1) and the rotors (5 and 6) must not
be oiled or greased.
Friction value-increasing surface treatments are not
permitted.
Please abstain from using cleaning agents containing
solvents, as they could affect the friction material.