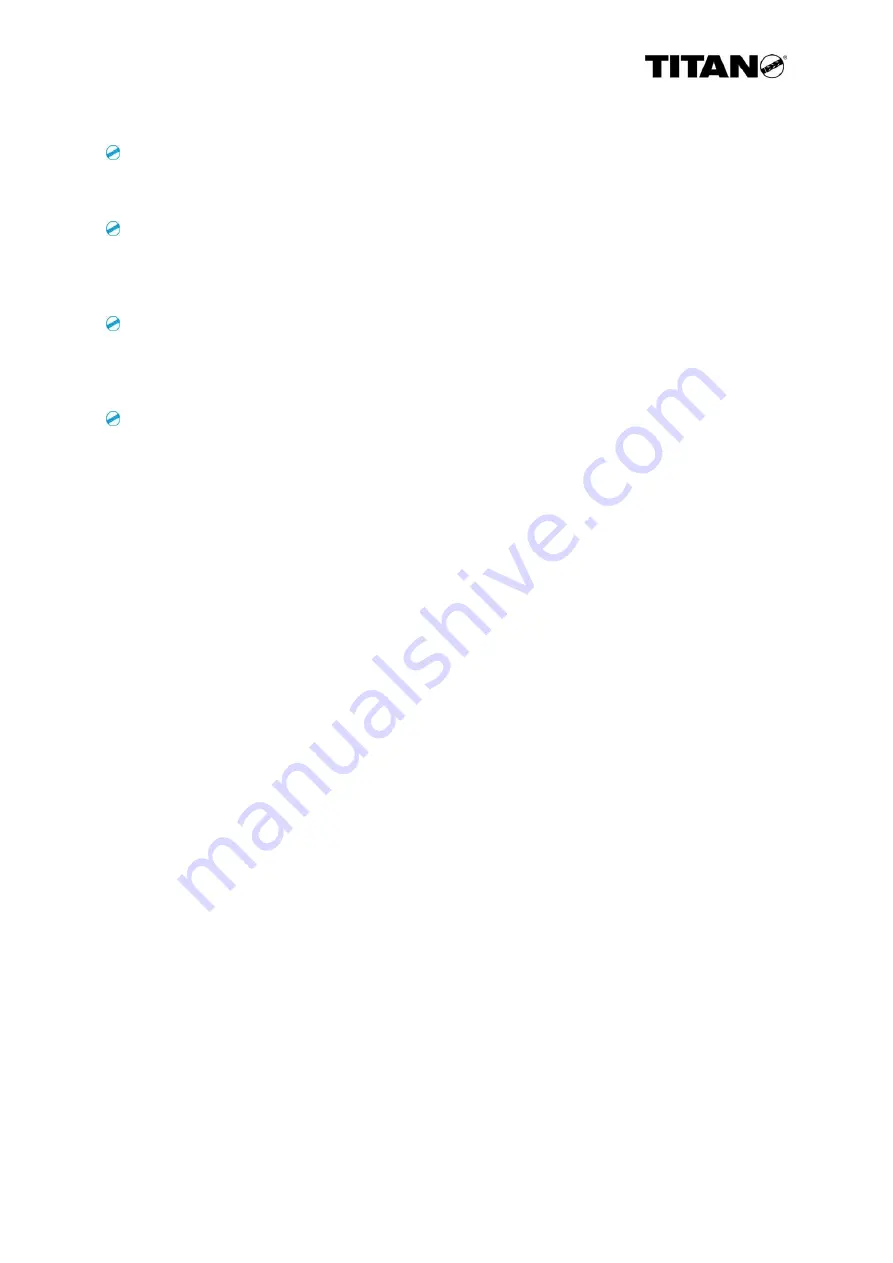
VS-32-L
6
Three compressed air motors and two compressed air cylinder perform all functions of
the strapping head.
Just compressed air being dewatered, filtered and oiled is used. Air pressure
(flow pressure with transport motor being switched on) should be 6 bar. The port cross
section of the feed line must be G 3/4“ or greater.
Air consumption per strapping operation with conduit dimensions amounting to 2000 x
1000 mm is 0,2 to 0,3 m³. Consumption during the transport of strap is
1,25 m³/min. The short-time peak consumption is at 2,5 m³/min.
The argon/welding gas consumption amounts to 2 l per seal. When a 50 l gas bottle
with a filling pressure of 200 bar is used, approx. 5000 seals are possible, in case of
300 bar approx. 7500 seals. The welding electrode can be ground approx. 100 times.
B 13 GB 07/10